CMMS Work Order: Insights & Implementation Strategies
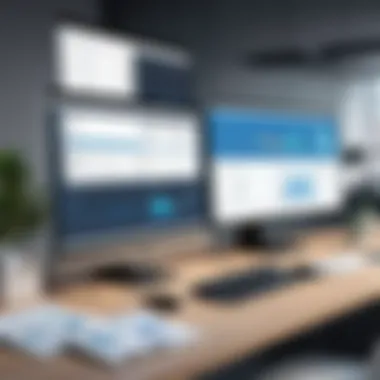
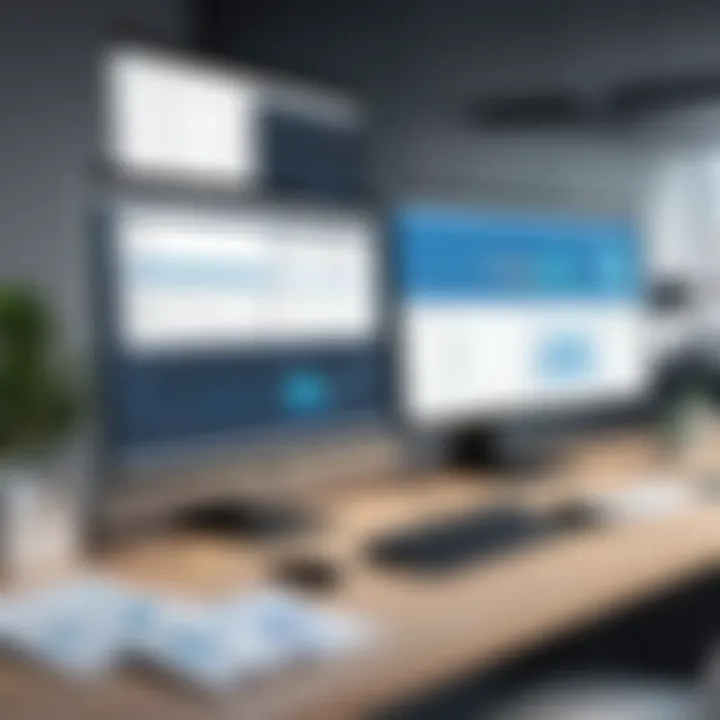
Intro
In the realm of asset management and maintenance, the importance of a well-structured system cannot be overstated. Computerized Maintenance Management Systems (CMMS) have emerged as pivotal tools for organizations striving to enhance operational efficiency. Work orders serve as the backbone of CMMS, facilitating effective maintenance practices and optimizing the overall workflow. This section delves into the function and potential of work orders within a CMMS framework, providing critical insights that can lead to improved productivity.
Functionality
Overview of key features
CMMS work orders offer a suite of features designed to streamline maintenance processes. Central to their functionality are the following attributes:
- Automated task assignment: Tasks can be dispatched automatically to relevant personnel based on predefined criteria, ensuring accountability and reducing delays.
- Real-time tracking: Users can monitor the status of work orders instantly. This enables quick adjustments and enhances communication between stakeholders.
- Detailed reporting: Comprehensive reports can be generated to track maintenance history, costs, and time taken. This data serves as a foundation for informed decision-making.
- Integration capabilities: Many CMMS products can integrate with existing software, allowing for a seamless flow of information across departments.
How well the software meets user needs
The needs of users vary significantly across different sectors. Effective CMMS should cater to these diverse requirements by:
- Ensuring user-friendly interfaces that allow ease of access and navigation.
- Providing customization options for work orders to accommodate specific operational needs.
- Facilitating training resources that help users understand features deeply.
Adopting a CMMS enhances the ability to track and manage maintenance activities efficiently. By complying with industry standards, it supports strategic maintenance planning and execution.
Scalability
Adaptability for growth
As organizations expand, their maintenance needs often evolve. A robust CMMS must exhibit scalability to support growing operations. This includes the agility to adjust workflows to accommodate new assets, additional staff, or even new facilities. Scalable systems prevent costly disruptions associated with rapid growth but also allow organizations to maintain control and oversight as they diversify.
Options for additional features or modules
Many CMMS solutions offer optional modules that can be integrated as needed. These might include:
- Inventory management: To oversee spare parts and reduce stock costs.
- Preventive maintenance: Designed to schedule routine checks that prevent breakdowns.
- Analytics and reporting: To provide deeper insights into maintenance trends and operational bottlenecks.
"Efficiency is doing things right; effectiveness is doing the right things."
By leveraging the power of CMMS work orders, organizations can position themselves strategically in their respective industries.
Understanding CMMS
Computerized Maintenance Management Systems (CMMS) play a crucial role in enhancing operational effectiveness within organizations. Understanding CMMS is fundamental for businesses looking to optimize maintenance processes, increase asset uptime, and minimize costs. In this article, we unpack the intricacies of CMMS, focusing on its definition, historical development, and core features. With a solid grasp of CMMS, organizations can develop more coherent strategies for their maintenance needs.
Definition and Scope
A Computerized Maintenance Management System (CMMS) refers to software that assists organizations in managing maintenance operations efficiently. The primary scope of a CMMS involves automating and streamlining maintenance management tasks, from scheduling to reporting and inventory control. By employing a CMMS, users gain access to a centralized platform for recording maintenance activities, managing work orders, and tracking asset performance. This centralization aids in reducing human error and enhances data accessibility, thereby facilitating better decision-making.
Historical Context
The genesis of CMMS can be traced back to the early days of computerized systems in the 1960s. Initially, these systems were designed for tracking and managing mechanical equipment only. Over the decades, as technology evolved, so did the capabilities of CMMS solutions. The advancement of computing technology in the 1980s led to more sophisticated CMMS applications which began incorporating functionalities for preventive maintenance and detailed reporting. In recent years, cloud-based solutions have become widely adopted. These enable greater scalability and access from anywhere, allowing teams to become more agile.
Core Features
A well-designed CMMS includes several core features that streamline maintenance management tasks:
- Work Order Management: This allows users to create, assign, and track the status of work orders, ensuring timely completion of maintenance tasks.
- Preventive Maintenance Scheduling: Organizing maintenance tasks proactively reduces the risk of asset failure by performing maintenance before issues arise.
- Asset Management: Track asset performance, history, and maintenance needs in real time.
- Inventory Management: Helps manage spare parts inventory, ensuring that the necessary parts are available when needed.
- Reporting and Analytics: Generate reports to analyze maintenance costs and performance metrics for informed decision-making.
By integrating these features, CMMS solutions become indispensable tools for organizations seeking to enhance their asset management strategies.
"Understanding CMMS is essential for businesses aiming to streamline their maintenance operations. With the right approach, it can dramatically improve efficiency."
In summary, mastering the fundamentals of CMMS lays the groundwork for effective work order management. It empowers organizations to manage their assets strategically, ensuring enhanced productivity and reduced costs.
The Role of Work Orders in CMMS
Work orders are a fundamental part of any Computerized Maintenance Management System (CMMS). They serve as the backbone for tracking and managing maintenance tasks. Understanding their role is essential for optimizing asset management and improving maintenance workflows. In this section, we will discuss the purpose of work orders, their components, and how they integrate into the overall workflow of a CMMS.
Purpose of Work Orders
The primary purpose of work orders in CMMS is to provide a structured approach for managing maintenance tasks. They facilitate the organization and execution of work by offering specific information related to repair, inspection, or routine maintenance. By creating a formal request for maintenance, work orders ensure accountability and provide insights into what needs to be done and when.
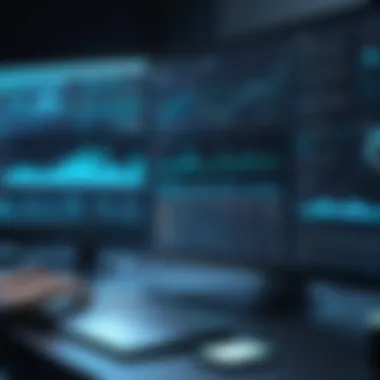

Key benefits of work orders include:
- Clarity: They define tasks clearly, minimizing misunderstandings within teams.
- Documentation: Work orders act as a record of all maintenance performed on assets, aiding in compliance and audits.
- Resource Allocation: They help in planning resource needs effectively, which enhances productivity.
- Performance Tracking: Work orders allow businesses to track the time and materials spent on each job, leading to better budget management.
Components of a Work Order
A well-structured work order consists of several vital components that collectively contribute to its effectiveness. Each part provides critical information that guides maintenance personnel in their tasks. Basic components typically include:
- Description of Work: A clear and detailed description of the task at hand.
- Priority Level: Indicates whether the task is urgent or can wait, which aids in effective resource management.
- Assigned Personnel: Names or roles of individuals responsible for completing the task.
- Materials and Parts Needed: List of any materials or parts required to complete the job, helping to streamline procurement.
- Scheduled Date: A target date for when the work should be started and finished.
- Status Updates: Sections for recording progress and any issues encountered during the maintenance task.
Each of these components plays a vital role in ensuring that maintenance activities are performed efficiently and effectively.
Workflow Integration
Integrating work orders into the existing operational workflows of an organization is critical for maximizing efficiency. This integration involves aligning work orders with other processes in the CMMS, such as inventory management and scheduling.
Key considerations for successful integration include:
- Communication: Effective communication channels must exist to ensure that all team members are aware of updates and changes to work orders.
- Software Compatibility: The chosen CMMS should integrate easily with other software tools to enable seamless data flow.
- Feedback Mechanisms: Regular reviews of completed work orders help in identifying trends and potential areas for improvement in workflows.
Successful integration will not only enhance the efficiency of operations but also significantly improve the overall maintenance strategy of an organization.
An organizationβs ability to execute maintenance tasks efficiently depends greatly on the clarity and effectiveness of its work order processes.
Creating Effective Work Orders
Creating effective work orders is essential in harnessing the full potential of a Computerized Maintenance Management System (CMMS). Well-crafted work orders facilitate seamless communication, enable prioritization, and ensure that maintenance tasks are executed efficiently. The advantages of having effective work orders are manifold. Not only do they help in managing resources better, but they also contribute significantly to minimizing downtime and enhancing overall operational efficiency. Furthermore, by establishing clear guidelines for work orders, businesses can improve accountability and traceability of maintenance tasks.
Information Requirements
To develop effective work orders, it is crucial to gather comprehensive information. This includes the specifics of the task, resources required, and any prior maintenance records. Essential details might comprise:
- Task Description: Clear and concise explanation of what needs to be done.
- Location: Precise location of the asset needing attention, which aids in planning and resource allocation.
- Priority Level: Designation of urgency to ensure critical tasks are attended to first.
- Materials Required: Listing of necessary materials so that maintenance personnel have what they need without unnecessary delays.
Additionally, including historical maintenance data can help in understanding recurring issues and developing more effective strategies. Ensuring workers have access to relevant information at their fingertips also enhances decision-making processes on the ground.
Prioritization Strategies
Establishing effective prioritization strategies is key in managing the workload associated with work orders. This involves categorizing them based on urgency and impact on operations. Strategies may include:
- Urgency Categories: Assigning levels from critical to low priority based on how promptly the task needs completion.
- Impact Assessment: Evaluating how the delay in maintenance will affect operations. Higher impact tasks should receive more immediate attention.
- Maintenance Schedules: Aligning work orders with existing maintenance schedules and cycles to optimize resource allocation.
Utilizing a structured approach to prioritization not only helps in resource allocation but also assists technicians in focusing on the right tasks at the right time. It allows organizations to minimize any adverse effects on productivity and sustainability.
Collaboration and Communication
Collaboration and communication are superior facets in the creation of effective work orders. Engaging different stakeholders provides far-reaching benefits. Key aspects include:
- Cross-Departmental Communication: Encouraging interaction between various departments is crucial. For example, the maintenance team should communicate with the operations department to understand how maintenance tasks affect production timelines.
- Feedback Loops: Creating systems for feedback from technicians on the accuracy and clarity of work orders can improve future orders. Acknowledging on-field insights helps refine the process, ensuring continuous improvement in work order quality.
- Real-time Updates: Investing in tools that track the progress of work orders in real-time enhances transparency and coordination among team members, ultimately improving responsiveness.
By promoting a collaborative culture and prioritizing open communication regarding work orders, businesses can enhance productivity and achieve their maintenance goals more effectively.
Effective work orders are not just a formality; they are pivotal to successful maintenance strategies.
Implementing a CMMS Work Order System
Implementing a Computerized Maintenance Management System (CMMS) work order system is crucial for organizations looking to enhance operational efficiency. A well-structured system facilitates consistent tracking and management of maintenance tasks. It plays a significant role in asset management, reducing downtime and streamlining workflow. By focusing on specific aspects such as business needs assessment and vendor selection, organizations can ensure they choose the right system that aligns with their objectives.
Assessment of Business Needs
Identifying business needs is the first step in successfully implementing a CMMS work order system. Organizations must analyze their existing maintenance processes and pinpoint pain points. Questions to consider include:
- What are the current challenges in maintenance management?
- Are there specific assets that require more attention?
- How do existing systems integrate with current operations?
Understanding these elements helps in determining the functionalities required in a new CMMS. This assessment not only supports the justification for investment but also aids in aligning the chosen system with overall business goals. An accurate comprehension of needs leads to enhanced decision-making and better resource allocation.
Vendor Selection Criteria
Choosing the right vendor is essential for a successful CMMS implementation. Here are some important criteria to consider:
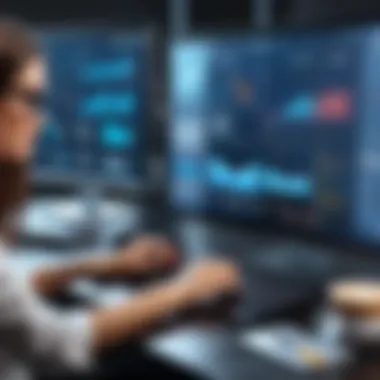
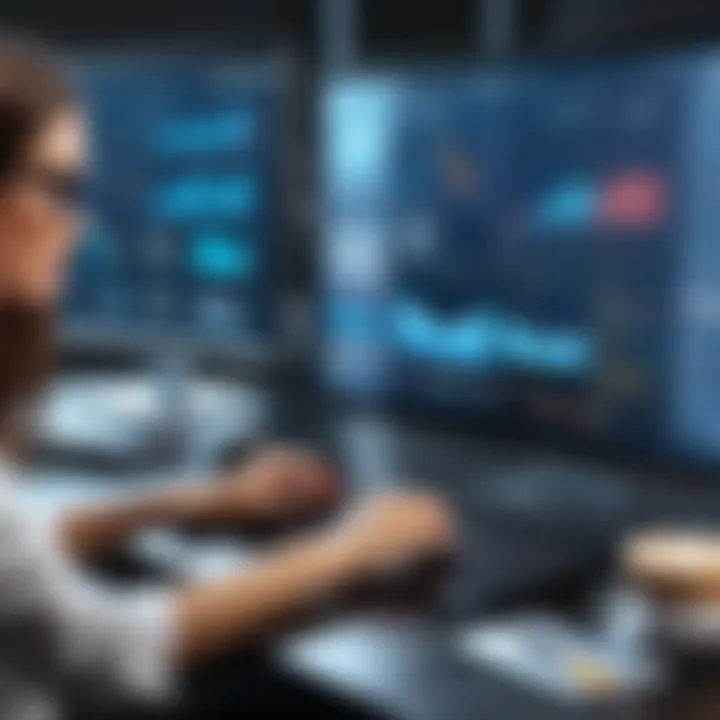
- Functionality: Evaluate if the CMMS has features specific to your industry. Look for elements like work order tracking, reporting capabilities, and maintenance scheduling.
- Integration: Ensure the vendor can provide a system that integrates with existing tools, such as ERP or inventory systems.
- Support and Training: Understand the level of vendor support available, including training options for staff. Good support can minimize disruption during the transition to a new system.
- Cost: Analyze total costs involved, including licensing, maintenance fees, and any additional implementation costs.
By focusing on these criteria, organizations can make informed choices that enhance their maintenance operations.
Training and Onboarding
Effective training and onboarding are crucial parts of implementing a CMMS work order system. Users must be comfortable and proficient with the new system to maximize its benefits. Here are key considerations:
- Comprehensive Training Program: Develop a training program that covers all functionality of the CMMS, focusing on everyday tasks. This must address different user levels from management to field technicians.
- Ongoing Support: Provide access to resources and support after the initial training. Users may encounter challenges as they adapt to new tools, and having a support system in place helps ease these transitions.
- Feedback Loop: Solicit feedback to identify any gaps in the training materials. Continuous improvement fosters a culture of learning, benefiting the organization and enhancing overall productivity.
Implementing a CMMS work order system involves careful planning, assessment, and training. By prioritizing these critical areas, businesses can set up an efficient work order system that meets their specific needs.
Best Practices for Work Order Management
In the context of Computerized Maintenance Management Systems (CMMS), the management of work orders requires a structured approach. Effective work order management can significantly enhance operational efficiency and minimize downtime. Adhering to best practices ensures that your maintenance team works more effectively, leading to savings in time and costs.
Regular Review and Updates
Regular review of work orders is essential. A systematic process helps to identify bottlenecks in the maintenance workflow. Updates should not just be reactive but also proactive. Schedule periodic reviews to evaluate the current status of open work orders. By doing so, maintenance teams can prioritize tasks effectively. It allows for allocating resources to the most urgent and impactful work.
Moreover, maintaining an up-to-date database prevents the loss of valuable information. Outdated work orders can clutter the system and lead to confusion. Ideally, regular reviews should include the assessment of closed work orders to help in learning from past experiences and improving future practices.
Utilizing Feedback
Feedback is a powerful tool in improving work order management. It should be a part of the culture within organizations. Encourage technicians and operational staff to provide insights on the work order process. They are often the first to notice inefficiencies or obstacles that may not be apparent at managerial levels.
Utilizing feedback means establishing a feedback loop. This loop should capture information from all stakeholders involved in the work order process. Key components of feedback include:
- Identifying recurring issues that affect work order completion.
- Understanding the effectiveness of communication regarding work order tasks.
- Gathering suggestions for improvement, which can lead to better management practices.
When feedback is integrated into work order management, it fosters a more responsive and effective maintenance culture. It might mean revising processes, providing additional training, or modifying priorities.
Key Performance Indicators
Key Performance Indicators (KPIs) represent quantifiable metrics that help management gauge the effectiveness of the work order system. Establishing a set of KPIs is crucial for monitoring performance and identifying areas for improvement. Some important KPIs in work order management include:
- Average time to complete work orders: Tracks the efficiency of the maintenance team.
- Work order backlog: Measures the volume of outstanding work and can indicate resource shortages.
- Compliance with scheduled maintenance: Evaluates how well the team adheres to preventive maintenance schedules.
KPI monitoring should be ongoing. Regular analysis of these indicators can help detect trends over time. This data-driven approach facilitates the identification of issues before they escalate into larger problems. Moreover, sharing these metrics with staff can enhance accountability and encourage performance improvement.
By implementing best practices in work order management, organizations can maximize uptime, reduce costs, and improve the overall effectiveness of maintenance processes.
Data Analytics in Work Order Management
Data analytics plays a vital role in work order management within Computerized Maintenance Management Systems (CMMS). By transforming raw data into actionable insights, organizations can enhance their asset management strategies, streamline their maintenance processes, and ultimately improve operational efficiency. The increasing amounts of data generated in maintenance activities necessitate effective analytical tools to navigate through this excess and glean valuable information that drives decision making.
Role of Data in Decision Making
The utilization of data in decision making cannot be overstated. When managed well, data provides a clear picture of asset performance, maintenance schedules, and resource allocation. Organizations can analyze historical work orders to identify patterns and trends. This analysis allows for more informed choices regarding equipment replacements, service timelines, and workload distribution. Additionally, real-time data facilitates immediate operational adjustments to increase productivity.
Key benefits of leveraging data include:
- Enhanced resource allocation: Ensuring the right assets are prioritized at the right times.
- Faster response times: With data at hand, teams can act quickly on urgent maintenance needs.
- Improved safety protocols: Analyzing incidents can lead to better safety measures and training processes.
Predictive Maintenance
Predictive maintenance is an advanced strategy that uses data analytics to predict equipment failures before they occur. By constantly monitoring asset conditions, organizations can forecast when maintenance should be performed. This reduces unexpected downtime and extends the life of critical assets.
Factors to consider with predictive maintenance include:
- Monitoring technologies: Utilizing sensors to gather data on asset conditions in real time.
- Data analysis tools: Employing sophisticated algorithms to analyze data trends and patterns.
- Actionable insights: Making timely decisions based on predictive outcomes rather than historical incidents.
This proactive approach leads to significant cost savings and enhances operational continuity.
Reporting and Insights
Comprehensive reporting is essential in analyzing work orders and drawing insights. Effective reporting tools aid managers in understanding the efficiency of maintenance operations and the overall health of their assets. Analytics can uncover deep insights that allow for fine-tuning processes, improving performance metrics, and increasing accountability.
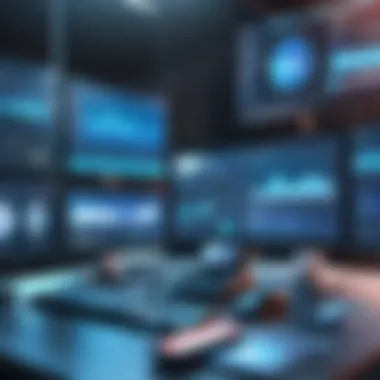
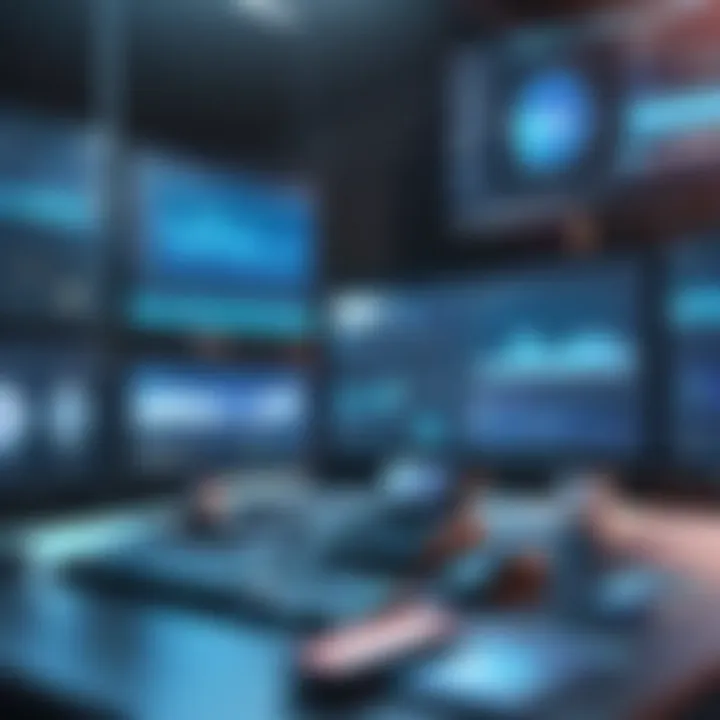
In your reporting, consider including the following:
- Work order completion rates: Understanding how efficiently work orders are being handled.
- Mean Time to Repair (MTTR): Assessing the average time taken to fix issues, which indicates process efficiency.
- Cost analysis: Evaluating the costs associated with various maintenance activities can reveal areas for improvement.
Challenges and Solutions
Understanding the challenges that arise during the implementation of a Computerized Maintenance Management System (CMMS) is essential for any business aiming to enhance its operational efficiency. Organizations often encounter various obstacles that can hinder the successful application of CMMS work orders. Addressing these challenges allows for smoother transitions, better asset management, and more effective maintenance processes. By recognizing potential issues early, companies can devise strategic solutions to the problems that may arise.
Common Obstacles in Implementation
When organizations attempt to implement CMMS work orders, they often face several common obstacles. These can include:
- Resistance to Change: Many team members may be accustomed to legacy systems or informal processes. This reluctance can slow down or derail the implementation.
- Data Quality Issues: Poor quality, incomplete, or outdated data can lead to inaccurate reporting and poor decision-making.
- Lack of Training: Users need proper training to effectively utilize the new system. Insufficient training can lead to mistakes and frustration among staff.
- Integration Challenges: Aligning the CMMS with existing software solutions, such as ERP systems, can be complicated.
- Budget Constraints: The costs associated with implementing and maintaining a CMMS can be a barrier for some organizations.
Mitigation Strategies
To overcome these challenges, businesses can employ several mitigation strategies. These strategies may include:
- Change Management Initiatives: Engaging employees early in the process can foster acceptance. Communicating the benefits of the new system helps vanquish resistance.
- Data Audits: Conducting thorough audits before implementation can ensure the accuracy and relevancy of the data being imported into the new system.
- Comprehensive Training Programs: Providing hands-on training sessions tailored to different user groups can significantly enhance the adoption process. Consider using workshops or e-learning modules.
- Phased Rollout: Implementing the CMMS in stages allows users to acclimate to the system gradually and minimizes disruption to ongoing operations.
- Budget Planning and Resource Allocation: Properly budgeting for initial costs and ongoing support will allow organizations to smooth out the financial impact over time.
Success Stories
To illustrate the potential for effective implementation of a CMMS, several success stories highlight organizations that have navigated challenges successfully:
- A Manufacturing Firm: By investing in change management, a large manufacturing firm improved equipment uptime by 25%. They effectively communicated the need for a CMMS and conducted regular feedback sessions to address concerns.
- A Healthcare Provider: This organization faced data integration challenges. By utilizing a phased approach, they were able to seamlessly integrate their CMMS with existing health records systems, resulting in improved maintenance tracking and reduced costs.
- A Municipal Agency: With thorough training and support, a city public works department transitioned to a CMMS, leading to optimized response times for maintenance work requests. Their initiative resulted in a notable increase in citizen satisfaction.
"The successful implementation of a CMMS can improve not only the maintenance workflow but also the overall efficiency of an organization."
Future Trends in CMMS Technology
The landscape of Computerized Maintenance Management Systems (CMMS) is constantly evolving to meet the demands of modern businesses. Understanding future trends in CMMS technology is vital for organizations looking to enhance asset management and maximize operational efficiency. Key elements such as emerging technologies, IoT integration, and mobile solutions play crucial roles in this evolution. These trends not only improve maintenance processes but also provide significant competitive advantages. It is essential for business professionals and IT specialists to stay informed about these developments to implement effective solutions that drive future success.
Emerging Technologies
Emerging technologies are reshaping the way businesses perceive and utilize CMMS. Innovations like artificial intelligence (AI), machine learning, and advanced analytics offer robust capabilities for maintenance management.
- Artificial Intelligence: AI helps in predicting equipment failures and optimizing maintenance schedules by analyzing historical data patterns. This capability significantly reduces downtime and improves asset lifespan.
- Machine Learning: Machine learning algorithms can continuously improve their accuracy as they process more data. This feature facilitates smarter decision-making, enhancing responsiveness to maintenance needs.
- Augmented Reality: AR can provide maintenance personnel with visual aids directly linked to work orders, reducing errors and increasing efficiency.
The adaptation to these technologies can require a shift in workforce training and infrastructure, but the benefits can outweigh the challenges.
Integration with IoT
The Internet of Things (IoT) is integral to the future of CMMS technology. The interconnection of devices and machinery enables real-time monitoring of asset conditions.
- Data Collection: IoT devices collect data from machinery which provide insights into performance and wear patterns. This data can be used to tailor maintenance schedules for each machine individually.
- Predictive Maintenance: With the integration of IoT, predictive maintenance becomes more accessible. Devices can alert teams about potential issues before they escalate into costly repairs.
- Enhanced Communication: IoT facilitates seamless communication between devices and the CMMS platform, ensuring that work orders are executed based on the most recent data. This leads to better overall management of resources and time.
The increases in efficiency that come from IoT integration create significant opportunities for companies to improve their bottom line.
Mobile Solutions and Remote Access
As the workforce becomes more mobile, the demand for mobile solutions in CMMS grows. Providing maintenance teams with remote access to the system enhances operational flexibility.
- On-the-Go Access: Technicians can receive work orders, updates, and track inventory management directly from their mobile devices, keeping them informed in real-time.
- Cloud-Based Systems: Many modern CMMS are hosted in the cloud, enabling access from anywhere. This feature improves collaboration among teams and increases productivity by allowing teams to work efficiently from various locations.
- User-Friendly Interfaces: Mobile solutions that offer intuitive designs are easier to navigate. This convenience leads to improved compliance with work order processes, as the workforce finds it simpler to engage with the system.
These mobile capabilities reflect a shift towards more agile operations, making the entire maintenance process more responsive.
"Incorporating mobile solutions in CMMS allows businesses to empower their maintenance teams, making systems more versatile and intuitive."
Culmination
In the context of this article, the conclusion serves as a critical component that brings together the various insights discussed about CMMS work orders. It emphasizes the importance of understanding how work orders fit into the larger framework of asset management and operational efficiency. A well-structured CMMS work order can significantly streamline maintenance processes, reduce downtime, and optimize resource allocation. This not only enhances productivity but also aids in extending the lifespan of assets across different industries.
Summary of Key Points
The primary elements covered throughout the article can be distilled into several key points:
- Definition and Scope: CMMS is crucial for maintaining operational readiness and asset longevity.
- Work Order Role: Work orders act as the backbone of maintenance activities, detailing tasks while ensuring effective workflow integration.
- Effective Creation: Crafting clear work orders with the necessary information facilitates prioritization and collaboration among teams.
- Implementation Strategies: Assessing business needs, selecting the right vendor, and ensuring proper training are all essential steps for successful implementation.
- Best Practices: Regular updates and feedback loops are vital for continuous improvement in work order management.
- Data Analytics: Leveraging data enables informed decision-making, predictive maintenance, and insightful reporting.
- Future Trends: Staying aware of new technologies, IoT integration, and mobile accessibility will help businesses remain competitive and agile.
Final Thoughts
Ultimately, the effective management of CMMS work orders is more than just a process; it is a strategic approach to enhancing maintenance operations. Companies that embrace these practices position themselves to not only meet current challenges but to anticipate future needs. The insights presented in this article are designed to equip business professionals with the necessary knowledge to implement CMMS successfully. By harnessing the power of technology and data analytics, organizations can achieve significant gains in productivity and efficiency, thereby paving the way for sustained growth and success in a complex operational landscape.
"Investing in a robust CMMS work order system today can lead to unprecedented operational improvements tomorrow."
The journey toward effective CMMS implementation may be complex but is rewarding. Being proactive in adopting best practices will enable organizations to thrive in a rapidly changing environment.