Comprehensive Maintenance Management Insights
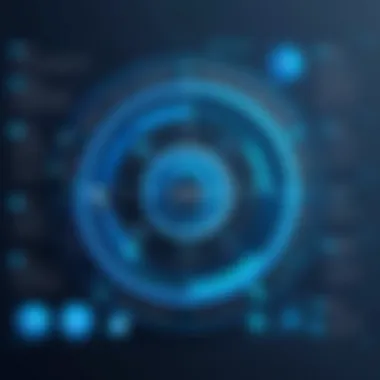
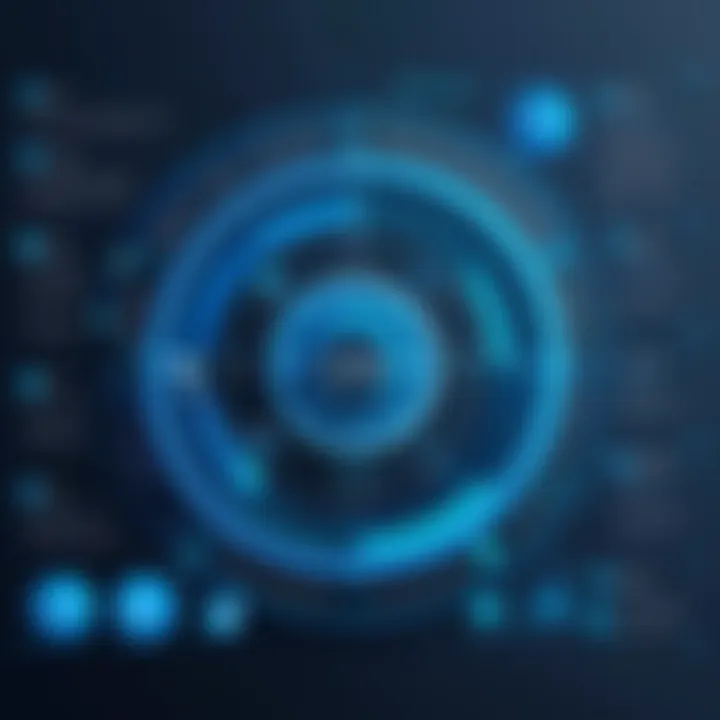
Intro
Maintenance management is a critical function in various industries, combining strategy and technology to ensure operational efficiency. Understanding its principles allows organizations to optimize resources, reduce downtime, and prolong the lifespan of equipment. This article provides a deep dive into maintenance management, examining methodologies, strategies, and the emerging role of technology.
Efficient maintenance management is no longer just about fixing what is broken. It involves a comprehensive understanding of processes that contribute to overall performance. For example, the integration of data analytics plays a significant role in predicting failures before they occur, enabling proactive management over reactive approaches. This shift from reactive to proactive maintenance is pivotal, as it minimizes disruptions and lowers costs.
The various maintenance strategies explored in this article include preventive, predictive, and corrective maintenance. Each strategy comes with unique advantages and considerations that must be understood to determine the best fit for any particular organizational context. We will examine these strategies in detail, providing insights into their applications and effectiveness.
Furthermore, the successful implementation of these strategies is heavily influenced by the use of innovative technologies. From Internet of Things (IoT) devices to advanced analytics software, these tools enhance decision-making capabilities and streamline maintenance processes.
A significant component of this discussion will focus on industry best practices and emerging trends in maintenance management. Organizations must stay informed about these developments to remain competitive and ensure that their maintenance processes are aligned with contemporary standards. This article aims to provide readers with the knowledge and insights necessary for optimizing maintenance processes within their own organizations, paving the way for improved operational performance.
"Effective maintenance management is at the core of sustaining high performance and productivity within an organization."
Throughout this detailed exploration, key terms such as operational efficiency, data analytics, and strategies will be elaborated upon. Understanding these terms will aid stakeholders in grasping the complexities of modern maintenance management and its implications on an organizationโs overall success.
By the end of this article, readers should have a clear roadmap on how to implement a comprehensive approach to maintenance management, ensuring that their organizations not only survive but thrive in today's competitive landscape.
Understanding Maintenance Management
Maintenance management is fundamental to the effective operation of any organization, particularly those relying on machinery, equipment, and technology. This section aims to elucidate the essential aspects of maintenance management, serving as a foundation for the insights to unfold in this article. Understanding this domain helps organizations implement strategies that mitigate downtime, enhance productivity, and extend the lifecycle of assets.
Definition and Scope
Maintenance management encompasses the planning, organizing, and controlling of maintenance activities. It aims to ensure that equipment and machinery operate at optimal levels, minimizing disruptions in production or service delivery.
In its broadest sense, the scope of maintenance management includes:
- Preventive Maintenance: Proactive actions designed to prevent failures before they occur.
- Corrective Maintenance: Actions taken to restore equipment after a failure has occurred.
- Predictive Maintenance: Using data analysis tools and techniques to detect anomalies in machinery and potential failures before they happen.
Clarity in the definition and scope of maintenance management allows professionals to tailor their strategies effectively. This awareness drives improvement in the reliability and availability of assets, which ultimately contributes to operational success.
Importance in Various Industries
The significance of maintenance management transcends specific sectors, impacting industries such as manufacturing, healthcare, transportation, and energy. In manufacturing, for instance, well-executed maintenance strategies can lead to higher production quality and consistency. For healthcare providers, ensuring that medical equipment functions optimally is vital for patient safety and care quality.
Other aspects of importance include:
- Cost Reduction: Effective maintenance management can lower operational costs by minimizing unexpected breakdowns and reducing the need for costly repairs.
- Regulatory Compliance: Adhering to maintenance protocols ensures that organizations meet industry regulations and standards, thus avoiding penalties.
- Asset Longevity: A systematic approach to maintenance helps prolong the lifespan of physical assets, providing better returns on investment.
"Effective maintenance management is not just about fixing things; it is about creating a culture of efficiency and reliability."
In summary, understanding maintenance management allows stakeholders to appreciate its value in promoting sustainability and profitability within various industries. Organizations that invest in comprehensive maintenance practices position themselves well for long-term success.
Types of Maintenance Strategies
Maintenance strategies are essential to enhance the reliability and efficiency of operations across various industries. Understanding the different approaches helps organizations choose a method that aligns with their operational goals. Each type possesses unique advantages and challenges, making comprehension critical for successful implementation.
Preventive Maintenance
Preventive maintenance aims to prevent equipment failure by conducting regular inspections, servicing, and replacements at scheduled intervals. Organizations using this strategy often experience lower overall maintenance costs due to reduced unplanned breakdowns.
The key features include:
- Scheduled Tasks: Frequent maintenance tasks are planned based on time or usage.
- Extended Equipment Lifespan: Regular care helps in prolonging the life of machinery.
- Increased Reliability: This method minimizes the risk of sudden failures.
However, it is essential to balance preventive schedules with the actual wear patterns of equipment. Over-maintaining may lead to unnecessary costs.
Predictive Maintenance
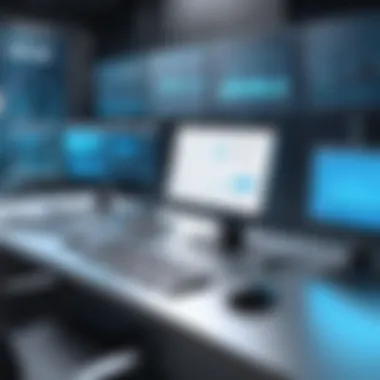
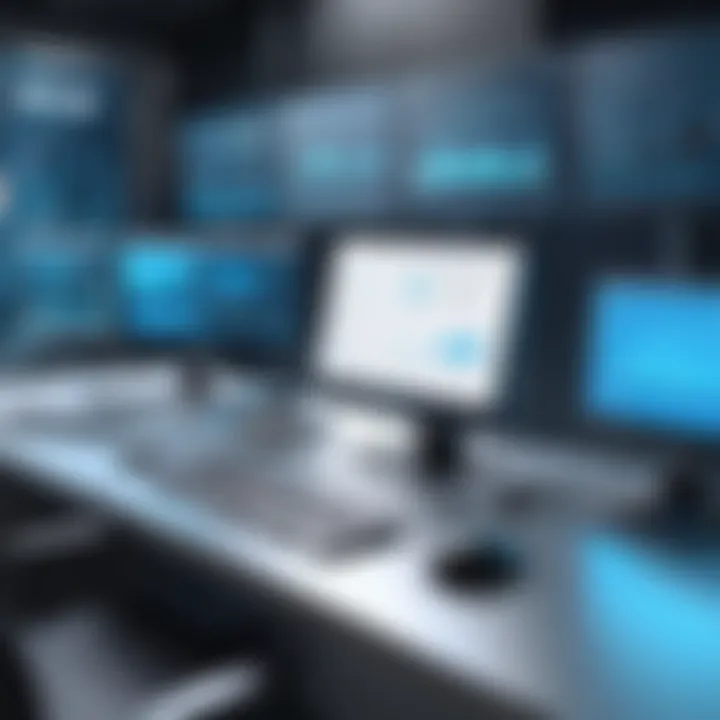
Predictive maintenance involves monitoring equipment conditions to forecast when maintenance should be carried out. Using data from sensors, real-time analytics can predict wear and tear before equipment fails.
Benefits include:
- Data-Driven Decisions: Maintenance tasks are determined based on actual data.
- Cost Efficiency: Reduces unnecessary work and optimizes resource use.
- Minimized Downtime: Repairs are conducted only when necessary, keeping equipment operational longer.
Implementing this strategy requires advanced technology like IoT sensors and data analytics tools to gather and interpret data accurately.
Corrective Maintenance
Corrective maintenance is reactive, addressing failures after they occur. While this can be seen as a less organized approach, it has its place in maintenance management.
Key characteristics are:
- Immediate Response: Fixes issues as they arise, often leading to downtime.
- Cost Implications: While it might be low-cost initially, the long-term effects of operational interruptions can be significant.
- Simplicity: No sophisticated planning required, but an ad-hoc approach can lead to inefficiencies.
This method is best suited for low-criticality equipment or when the cost of alternative strategies outweighs the benefits.
Reliability-Centered Maintenance
Reliability-centered maintenance focuses on ensuring that systems continue to do what their users require under varying conditions. It evaluates the functions of an asset and its associated failure modes to develop applicable maintenance strategies.
Consider the following aspects:
- Functional Analysis: It thoroughly investigates the desired functions versus potential failures.
- Prioritization: Resources are directed toward the most vital systems.
- Adaptability: Changes in the system or environment can adjust the maintenance plan as needed.
This approach is sophisticated but highly effective for organizations that rely on critical operations, promoting high reliability in performance.
The Role of Technology in Maintenance Management
Technology plays a crucial role in enhancing maintenance management across various industries. Its integration not only leads to improved operational efficiency but also aids in proactive decision-making. By employing advanced tools and automated systems, organizations can effectively monitor assets, predict failures, and optimize maintenance schedules. The advent of technology paves the way for a more strategic approach to maintenance management, shifting from reactive measures to preventative strategies that can greatly reduce downtime.
Software Solutions
Software solutions have transformed the landscape of maintenance management. Computerized Maintenance Management Systems (CMMS) are essential tools for tracking maintenance activities, inventory, work orders, and compliance with regulations.
Some benefits of implementing CMMS include:
- Efficiency: These systems automate routine tasks, reducing the administrative burden on staff.
- Data Centralization: All maintenance data is stored in one place, making it accessible for analysis and reporting.
- Enhanced Communication: Users can easily share information and updates, fostering collaboration among maintenance teams.
Popular software options include Infor EAM, SAP PM, and Microsoft Dynamics. Each of these platforms offers unique features that tailor to specific industry needs.
Internet of Things (IoT)
The Internet of Things (IoT) brings real-time data acquisition to maintenance management. With connected devices and sensors, organizations can gather valuable insights on equipment condition and performance.
Advantages of IoT in maintenance management include:
- Real-Time Monitoring: Continuous observation of equipment performance helps detect issues before they escalate.
- Predictive Maintenance: Data from IoT devices enables predictive analytics, allowing organizations to anticipate equipment failures based on usage trends.
- Reduced Downtime: By addressing problems proactively, companies can minimize unscheduled maintenance and associated costs.
By deploying IoT technologies, businesses can enhance reliability and performance, leading to improved overall productivity.
Data Analytics and Reporting
Data analytics and reporting are integral components of modern maintenance management. The ability to analyze maintenance data leads to informed decisions that can enhance efficiency and effectiveness.
Through analytics, organizations can:
- Identify Trends: Analyzing historical data helps recognize patterns in equipment failures and maintenance needs.
- Benchmark Performance: Organizations can assess their performance against industry standards or past performance metrics, aiding continuous improvement efforts.
- Tailor Maintenance Strategies: Insights from data can inform appropriate maintenance strategies based on specific equipment requirements.
Utilizing tools like Power BI or Tableau can provide companies with robust data visualization capabilities, translating complex data sets into actionable insights.
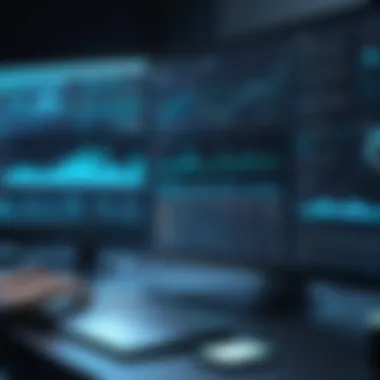

"Effective maintenance management combines the power of technology with strategic thinking to optimize operations and reduce costs."
Key Performance Indicators (KPIs) for Maintenance Management
In the realm of maintenance management, Key Performance Indicators (KPIs) serve as essential tools for measuring effectiveness and efficiency. They provide businesses with quantitative and qualitative data to assess the performance of maintenance activities. KPIs not only facilitate decision-making but also foster a culture of accountability among teams. By defining and monitoring relevant KPIs, organizations can pinpoint areas for improvement, leading to significant advancements in operational performance.
Defining Relevant KPIs
For KPIs to be effective, they must align with the organization's goals and maintenance strategies. Some relevant KPIs in maintenance management include:
- Mean Time to Repair (MTTR): This measures the average time taken to repair equipment after a failure. A lower MTTR indicates a more efficient maintenance process.
- Mean Time Between Failures (MTBF): This KPI tracks the average time elapsed between failures of a system. It reflects the reliability of equipment.
- Maintenance Cost as a Percentage of Asset Value: This metric helps assess whether maintenance expenditures are reasonable in relation to the overall value of assets.
When defining KPIs, it is critical to consider the specific context of the organization as well as industry standards. Engaging stakeholders in this process ensures that the selected KPIs reflect what is truly important for the organization's success.
Benchmarking and Comparison
Benchmarking KPIs against industry standards or best practices is a vital step for continuous improvement in maintenance management. This involves comparing an organization's performance metrics with those of peers or leaders in the field, providing insights into potential areas of enhancement.
Benefits of benchmarking include:
- Identifying Gaps: By comparing KPIs, organizations can detect performance gaps that require attention.
- Setting Targets: Establishing performance targets based on the benchmarking process allows organizations to aim for excellence.
- Stimulating Innovation: Insights gained from benchmarking can promote innovative maintenance practices as organizations strive to meet or exceed standards.
Utilizing KPIs in tandem with benchmarking creates a comprehensive framework for evaluating maintenance practices, ultimately driving informed decisions that enhance efficiency.
"The effective management of maintenance processes relies heavily on relevant KPIs and a clear understanding of performance metrics."
By continuously evaluating and refining KPIs, organizations can ensure that they remain aligned with the evolving needs of their operation.
Challenges in Maintenance Management
Effective maintenance management presents a range of challenges that can impact operational efficiency and organizational success. Recognizing these challenges allows companies to innovate and optimize their maintenance strategies. The most significant challenges include resource allocation, balancing costs and efficiency, and training staff for skill enhancement.
Resource Allocation and Management
Managing resources effectively is critical for any maintenance strategy. Organizations often face complexities in allocating manpower, tools, and materials where they are most needed. Poor resource allocation can lead to delays, bottlenecks, and increased downtime.
To navigate these issues, organizations should implement a systematic approach. This means understanding and tracking resource availability and demand using software solutions. Maintenance software like IBM Maximo or CMMS can assist in organizing these resources efficiently. Tools that enable visibility into resource usage can drive better decision-making and lead to more agile responses to maintenance needs.
Balancing Costs and Efficiency
Cost management is a constant concern in maintenance management. Organizations strive to minimize costs while maximizing efficiency. An imbalance can lead to overspending on maintenance or, conversely, adopting a superficial approach that detracts from operational performance.
A data-driven approach is essential in achieving this balance. Companies should focus on identifying key performance indicators that reflect both cost and efficiency metrics. Utilizing tools for predictive maintenance can reduce unplanned downtime and related expenses. This proactive approach can help avoid costly repairs while ensuring that equipment functions at optimal levels.
Training and Skill Development
The emphasis on continual training and development cannot be understated in maintenance management. As technologies evolve, the skill sets required from maintenance staff also shift. Ongoing training ensures that employees are equipped to handle modern equipment and methods.
Creating structured training programs can foster a culture of learning within the organization. Workshops, e-learning, and on-the-job training should be incorporated as standard practices. Organizations like the National Institute for Occupational Safety and Health (NIOSH) provide resources to assist in developing robust training frameworks. This not only enhances employee satisfaction but can also lead to improved maintenance outcomes.
By overcoming these challenges, a company can improve its maintenance strategies, leading to enhanced operational performance and competitive advantages.
Best Practices in Maintenance Management
In the dynamic field of maintenance management, implementing best practices is vital for ensuring operational efficiency and minimizing downtime. These practices not only improve the reliability of systems but also contribute to cost savings and enhanced performance. Focusing on specific elements such as Standard Operating Procedures, Continuous Improvement, and Stakeholder Engagement helps organizations develop a robust maintenance framework.
Standard Operating Procedures
Standard Operating Procedures (SOPs) are essential in maintenance management. They provide clear guidance on how to perform maintenance tasks systematically and effectively. By documenting procedures, organizations can ensure that maintenance activities are performed consistently, reducing errors and improving accountability.
Effective SOPs typically cover:
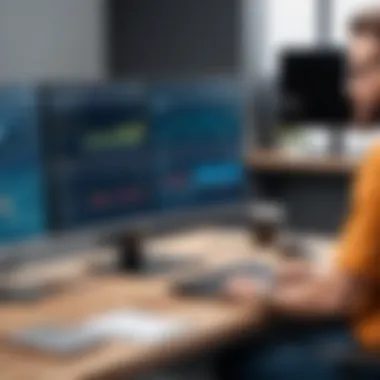
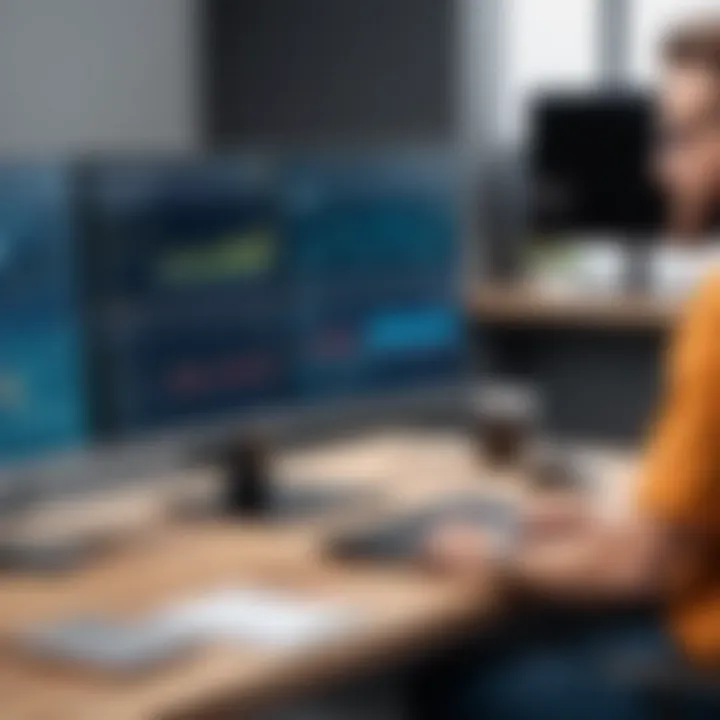
- Task Specifications: Detailed instructions on what needs to be done, when, and how.
- Safety Protocols: Guidelines for maintaining safety during maintenance tasks, critical to protecting personnel and equipment.
- Quality Control: Standards to assess the quality of maintenance work performed, ensuring that all tasks meet organizational and regulatory standards.
Additionally, SOPs facilitate training for new staff and serve as a reference for experienced personnel. Organizations that implement SOPs can enhance their ability to maintain equipment and extend its lifespan, ultimately leading to increased productivity.
Continuous Improvement
Continuous improvement is a fundamental practice in maintenance management that focuses on regularly assessing and enhancing processes. This practice aligns well with the principles of Lean Management and Six Sigma, fostering an environment where efficiency is constantly evaluated and optimized.
Key components of continuous improvement include:
- Data Analysis: Monitoring performance data to identify areas needing improvement.
- Feedback Mechanisms: Encouraging input from maintenance personnel to understand challenges and inefficiencies in processes.
- Training and Education: Regularly updating staff on the latest techniques and technologies equips them to implement efficient practices.
By adopting a continuous improvement mindset, organizations can adapt quickly to changing operational needs and technological advancements, ensuring they remain competitive in an ever-evolving landscape.
Stakeholder Engagement
Engaging stakeholders is crucial for the successful implementation of maintenance practices. Maintenance does not occur in isolation; it involves various departments and personnel. Effective communication and collaboration among different stakeholders lead to better understanding and support for maintenance initiatives.
Strategies for engaging stakeholders include:
- Regular Meetings: Schedule discussions to keep stakeholders informed about maintenance goals and challenges.
- Feedback Collection: Solicit input from different departments affected by maintenance activities to gain diverse perspectives.
- Training Workshops: Educate stakeholders about the importance of maintenance and how it contributes to overall organizational success.
When stakeholders feel involved in the maintenance process, there is a higher likelihood of support and cooperation. This engagement ultimately leads to a more effective maintenance management approach, aligning maintenance goals with broader organizational objectives.
"Effective maintenance management relies heavily on the collective effort and understanding of all stakeholders involved in the process."
The Future of Maintenance Management
The future of maintenance management is marked by rapid changes driven primarily by technological advancements and evolving business objectives. As organizations strive for higher efficiency and lower downtime, the ability to anticipate and respond to maintenance needs will become crucial. Proactive strategies that leverage real-time data will dominate, enabling more precise decision-making in maintenance operations.
Emerging Technologies
Emerging technologies play a vital role in changing the landscape of maintenance management. The adoption of artificial intelligence, machine learning, and advanced analytics is elevating the capabilities of maintenance teams. These technologies facilitate predictive maintenance, which shifts the focus from routine maintenance schedules to data-driven interventions. By analyzing trends and patterns in equipment performance, organizations can predict failures before they occur, minimizing costly downtimes.
- Artificial Intelligence: AI algorithms can process vast amounts of data quickly. This assists in identifying potential equipment failures, thereby allowing teams to schedule maintenance activities effectively.
- IoT Devices: The Internet of Things enables machines to communicate relevant performance data in real-time. This information is crucial for monitoring equipment health continuously and for instant reporting of anomalies.
- Cloud Computing: Access to cloud-based platforms ensures that maintenance data is centralized and available, facilitating collaboration among team members, regardless of their physical location.
Implementation of these technologies requires investment and training. However, the long-term benefits can significantly outweigh these costs, leading to improved operational efficiency.
"Incorporating technology is not just a trend but a strategic necessity in the realm of maintenance management."
Sustainability and Environmental Impact
As businesses become more aware of their ecological footprint, sustainability in maintenance management is gaining importance. The interplay between maintenance practices and environmental impact cannot be overlooked. A focus on sustainability is not just ethical but also can improve the bottom line.
- Energy Efficiency: By optimizing maintenance schedules and ensuring equipment operates properly, organizations can reduce energy consumption. This aligns with global goals of reducing carbon emissions.
- Material Management: Effective maintenance helps extend the life of equipment, which decreases the need for new materials. This conservation of resources is vital for sustainability initiatives.
- Regulatory Compliance: Organizations are also facing increased pressure to comply with environmental regulations. Proper maintenance practices can help achieve compliance, avoiding penalties and enhancing company reputation.
As the industry moves towards greener practices, organizations that prioritize sustainability in their maintenance strategies may gain a competitive edge. This shift not only meets regulatory demands but also responds to the broader consumer trends favoring environmentally responsible companies.
Ending
Effective maintenance management is crucial for ensuring optimal operational performance across various industries. This article has discussed several key elements that contribute to this comprehensive approach. By understanding and addressing these components, organizations can achieve significant benefits.
Recap of Key Points
- Understanding the Definition and Scope: Maintenance management encompasses various strategies and processes aimed at preserving assets and reducing downtime.
- Types of Maintenance Strategies: Organizations employ preventive, predictive, corrective, and reliability-centered maintenance to mitigate risks and enhance productivity.
- Role of Technology: Implementing advanced software solutions, leveraging IoT, and utilizing data analytics contribute to superior maintenance practices.
- Key Performance Indicators (KPIs): Defining relevant KPIs and benchmarking performance are essential in measuring success.
- Challenges: Addressing issues like resource allocation and training is necessary for effective implementation.
- Best Practices: Following standard operating procedures and engaging stakeholders promotes continuous improvement.
- Future Trends: Understanding emerging technologies and focusing on sustainability will shape the landscape of maintenance management.
"Strategic maintenance management is about foresight and preparedness rather than reactionary measures."
The Importance of Strategic Maintenance Management
Strategic maintenance management is not merely a series of tasks; it is a vital framework that drives organizational success. By aligning maintenance strategies with business objectives, organizations can create synergy between operational efficiency and financial performance.
Considerations for strategic maintenance management should include:
- Resource Optimization: Allocating resources effectively ensures that both time and finances are utilized efficiently.
- Risk Management: Identifying potential failure points allows companies to adopt proactive measures, reducing downtime and costs associated with unexpected failures.
- Data-Driven Decisions: Analytical insights facilitate informed decision-making. Trends and patterns emerging from data help to refine maintenance practices continuously.
- Sustainability Initiatives: Implementing strategies that focus on environmental impact leads to a positive corporate image and compliance with regulations.
Engaging with principles of strategic maintenance management not only prolongs asset life but also cultivates a culture of reliability and accountability. Organizations that prioritize these aspects are likely to outperform peers in both productivity and profitability.