Creating Effective Work Orders for Operational Success
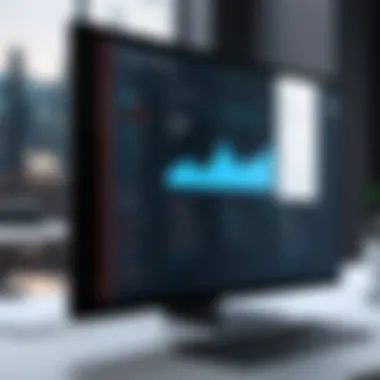

Intro
Creating work orders is a fundamental process that plays a crucial role in operational efficiency across many industries. Understanding the intricacies of crafting effective work orders can significantly enhance task management, leading to smoother operations and ultimately better outcomes for business ventures. This guide will dissect the essential components of an effective work order, elucidate best practices for implementation, and underscore the importance of communication in the ordering process. With an eye toward optimizing these practices, professionals can expect to see remarkable improvements in their workflows.
Functionality
Effective work orders should possess certain key functionalities that cater to the diverse needs of various stakeholders involved in the workflow. To achieve this, it is necessary to examine the fundamental features that contribute to a successful work order system.
Overview of Key Features
- Clear Description: A well-defined description of the task at hand is vital. It should encompass specific details that convey expectations.
- Assignee Information: Identifying the people responsible for the task can eliminate confusion. Their contact information and relevant skills should be included.
- Priority Level: Indicating the urgency of the task ensures that resources are allocated appropriately.
- Due Dates: Establishing deadlines helps to keep projects on track and facilitates better time management.
- Resource Allocation: Clearly documenting necessary materials or tools can prevent delays in task completion.
How Well the Software Meets User Needs
When implementing a work order system, evaluating how the chosen software meets user needs is essential.
- Does it allow for customization according to different workflows?
- Are the features intuitive enough that users can easily navigate through them?
- How does it integrate with existing systems in place?
The alignment between user expectations and software capabilities determines the effectiveness of work order management. If the software does not fulfill user requirements, it can lead to inconsistencies and inefficiencies, thus undermining the purpose of having a work order system in the first place.
Scalability
As businesses evolve, their operational needs can change significantly. Thus, work orders must be adaptable and scalable to ensure they remain effective in a dynamic environment.
Adaptability for Growth
A scalable work order system will seamlessly accommodate the growth of tasks and team size without necessitating a complete overhaul of processes. This adaptability can manifest in various forms, such as incorporating new task types or expanding user access.
Options for Additional Features or Modules
Moreover, a good work order system should offer options for advanced features or modules that can be added as needed. This modular approach allows organizations to remain agile, deploying new functionalities without disrupting existing workflows. Such features might include:
- Advanced reporting and analytics
- Integrated communication tools
- Automation capabilities for repetitive tasks
"In the fast-paced world of business, the ability to adapt is not just a benefit โ itโs essential for survival."
By strategically implementing and continuously refining work orders, organizations can ensure that they not only meet current requirements but are also prepared for future demands.
Preamble to Work Orders
Work orders serve as vital instruments in managing and executing tasks across various industries. In this section, we will explore the significance of work orders, defining their role in enhancing operational efficiency. Understanding work orders is essential for professionals aiming to streamline processes within their organizations.
Definition of Work Orders
A work order is a formalized document that outlines tasks required to be performed. It details what needs to be done, by whom, and within what timeframe. Work orders can pertain to maintenance, repairs, or projects. Their primary purpose is to ensure clarity and accountability in task execution. By setting clear expectations, work orders contribute to better resource allocation and time management.
Historical Context
The concept of work orders has evolved significantly over time. Initially, they were simple verbal requests or handwritten notes. As industries grew more complex, the need for structured documentation emerged. The introduction of computers and specialized software has further transformed work order management. Modern platforms allow for real-time updates, tracking, and integration with other business systems, enhancing overall operational efficiency.
Importance in Business Operations
Work orders are not merely administrative tools; they are critical for effective business operations. They facilitate communication among team members, ensuring everyone has access to the same information. Additionally, work orders help in:
- Tracking Resources: Proper documentation allows for better tracking of labor, materials, and equipment.
- Compliance: Many industries are regulated, making work orders essential for maintaining standards.
- Accountability: They define responsibilities, minimizing disputes regarding task ownership.
In summary, work orders streamline workflow, enhance communication, and drive accountability. A comprehensive understanding of work orders sets the stage for more effective task management in any organization.
Types of Work Orders
Understanding the types of work orders is crucial for efficient operational management. Each type serves a distinct purpose, enabling organizations to effectively manage tasks based on their urgency and nature. This section elucidates the three primary categories: Preventive Maintenance Work Orders, Corrective Work Orders, and Emergency Work Orders. Knowing when and how to deploy each type can enhance productivity and resource allocation.
Preventive Maintenance Work Orders
Preventive maintenance work orders are designed to prevent equipment failures before they occur. They are proactive measures that help in extending the lifespan of assets. These work orders are generated based on prescheduled maintenance intervals or equipment usage metrics.
- Benefits:
- Reduces the likelihood of unexpected breakdowns.
- Lowers overall maintenance costs over time.
- Enhances the reliability of operations.
- Improves safety standards by ensuring equipment functions correctly.
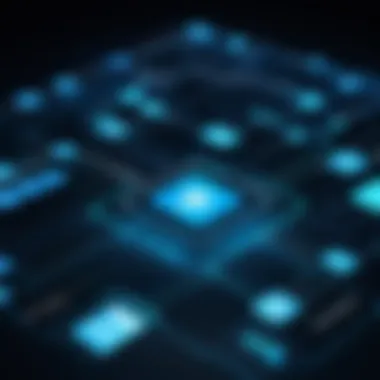
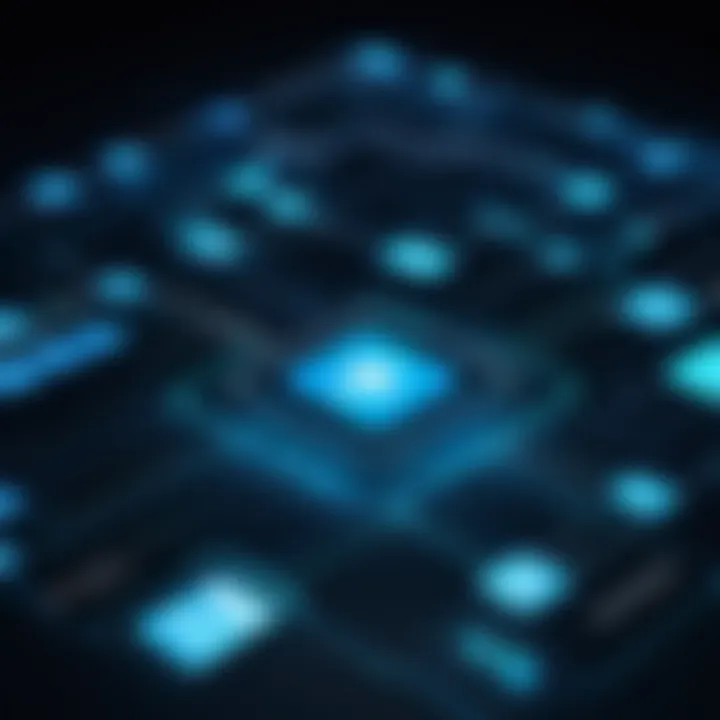
When creating these work orders, it is essential to include specific details such as the required maintenance tasks, frequency of service, and historical data on past maintenance interventions. By being systematic, companies can effectively plan their budgets and personnel deployment for maintenance operations.
Corrective Work Orders
Corrective work orders are reactive in nature. They are issued when equipment fails or when there are quality control issues that need immediate attention. This type reflects the critical need for responsive action in maintenance management.
- Key Considerations:
- They often need expedited processing to minimize downtime.
- Documentation of the fault is necessary for future analysis.
- Communication between teams is vital for effective resolution.
The content of a corrective work order should include clear descriptions of the issue, any immediate actions taken, and priority level. Accurate and prompt information processing ensures that issues are addressed before they escalate.
Emergency Work Orders
Emergency work orders are created in response to situations that demand immediate action. They may arise from unexpected equipment failures, critical safety issues, or urgent operational needs.
- Characteristics:
- Require immediate attention to mitigate risks or losses.
- Often interface with various departments for swift response.
- Can disrupt normal operations, hence proper management is vital.
These work orders must be straightforward and include critical information such as the location of the equipment, nature of the emergency, and personnel assigned to resolve the issue. The urgency associated with emergency work orders makes effective tracking crucial to ensure that all necessary measures are taken promptly.
"Understanding the types of work orders is essential for achieving operational efficiency. Knowing how to categorize them can lead to significant improvements in task management."
Key Components of a Work Order
Understanding the key components of a work order is fundamental for creating effective workflows in any organization. Each element plays a crucial role in ensuring that the work is completed effectively and efficiently. A well-organized work order helps streamline communication, minimizes errors, and improves overall operational efficiency. When creating a work order, specific components must be included to provide clarity and direction.
Identification Information
Identification information is crucial for tracking and referencing work orders. This section should include unique identifiers such as the work order number, which prevents confusion about tasks and projects. Including details such as the requesterโs name, date issued, and associated project or department ensures that all relevant parties have clear access to whom the order pertains and its context. Clear identification helps prevent duplication of work orders and supports accountability.
Task Description
The task description should precisely outline what work needs to be carried out. This component should be concise but comprehensive enough to avoid ambiguity. Rather than vague phrases, use clear language that specifies the exact tasks involved. This often includes a description of materials needed, potential challenges, and expected outcomes. A well-defined task description enables team members to understand their responsibilities and reduces the time spent discussing what needs to be done.
Location Details
Location details are significant since they identify where the work will physically take place. This section should provide precise information about the site, including GPS coordinates if necessary. Clear location details help in logistics, ensuring that resources are delivered to the appropriate site without delay. Safety can also be significantly enhanced when teams know exactly where the work is happening, particularly in large facilities or outdoor sites.
Priority Level
The priority level assigned to a work order is essential for task management. Work orders can vary in urgency; therefore, a clear indication of the priority helps the team allocate resources more effectively. By categorizing tasks as high, medium, or low priority, organizations can focus on the most critical work first, ensuring that pressing needs are met without overlooking less urgent requests. This careful prioritization is key in busy environments where multiple tasks are competing for attention.
Estimated Completion Time
Providing an estimated completion time is vital for planning and resource allocation. This component lets all stakeholders know when they can expect the work to be completed. Accurate timelines help manage workload, allowing teams to plan their schedules around expected deadlines. It's important to consider potential unforeseen circumstances when estimating completion times to avoid disappointment. Tracking actual completion against this estimate can also provide valuable data for future planning and process improvement.
Effective work orders represent not just a task assignment but a structured approach to operational efficiency.
In summary, each of these components contributes significantly to the successful management of work orders. By emphasizing clarity, accountability, and efficiency in these details, organizations can enhance their operational workflows, leading to improved productivity and satisfaction.
Steps to Create a Work Order
Creating an effective work order involves a systematic approach adapted to the needs of an organization. The process requires attention to detail and an understanding of operational requirements. It plays a crucial role in ensuring that tasks are completed timely and efficiently. Each step has strategic importance, which contributes to the overall effectiveness of work order management. By following these steps, businesses can enhance their workflows and minimize errors.
Gathering Necessary Information
Before initiating a work order, collecting all relevant information is essential. This involves understanding the specific task, the resources needed, and any constraints that might affect the execution. Gathering information can involve communication with various departments. Here are important points to consider:
- Task Specification: Clearly define what needs to be done. This may include repairs, installations, or maintenance.
- Resource Identification: Identify the tools, materials, and personnel required.
- Timeline Considerations: Recognize any deadlines that must be met.
Accurate information gathering reduces delays and miscommunications in later stages.
Choosing Appropriate Software or Tools
Selecting the right software for work order management is critical. The tool should suit the organization's specific needs, including workflow processes and team structure. Factors to consider include:
- User-Friendliness: The software should be intuitive for all users.
- Integration Capabilities: Ensure that it can integrate with existing business systems.
- Reporting Features: Look for tools that provide analytics to track performance and issues.
Popular choices include Cezar, ServiceTitan, or CMMS software tailored for maintenance operations.
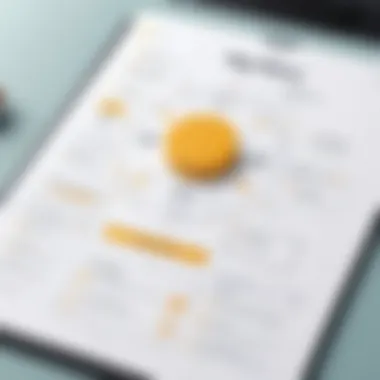
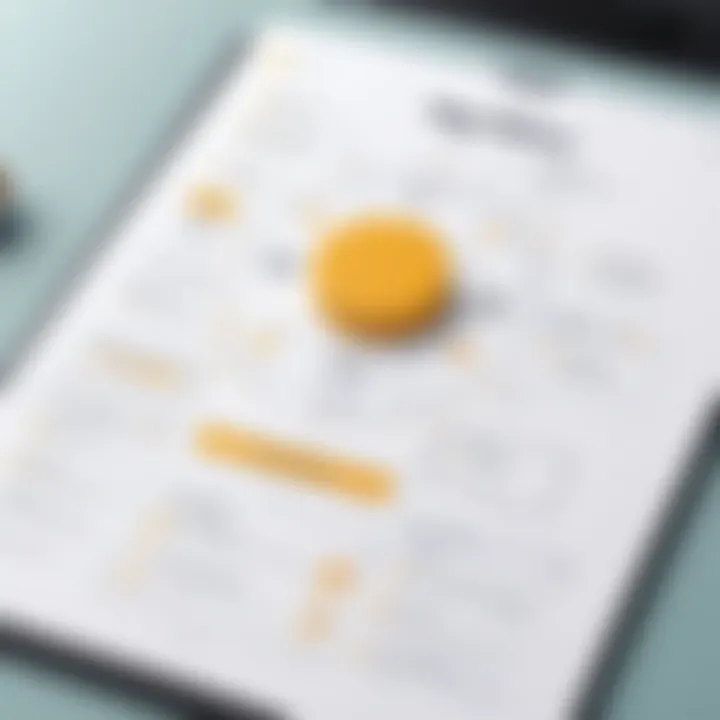
Filling Out the Work Order Template
The next step is to accurately fill out the work order template. A well-designed template captures essential information effectively. Components such as:
- Identification Information โ Include details such as work order number, requestor name, and dates.
- Task Description โ Provide a comprehensive description of the work required.
- Location Details โ Specify where the work is to be performed.
- Priority Level โ Indicate how urgently the task needs to be addressed.
- Estimated Completion Time โ State the anticipated duration for completing the task.
Employing a consistent format enhances clarity and helps in tracking.
Submitting the Work Order
After filling out the work order, the next phase is submission. This is where the request is officially recorded in the system. Ensure the submission process is straightforward. Depending on the software, it might involve:
- Digital Submission โ Entering the information into the system and saving it.
- Emailing the Request โ If not using a system, emailing the document to relevant personnel.
Timeliness is key at this stage. The sooner the order is submitted, the quicker it can be addressed.
Tracking and Follow-Up
The final step, which is often overlooked, involves tracking the status of the work order. Following up ensures accountability and fosters communication among team members. Important actions include:
- Monitoring Progress: Keep an eye on the status of tasks and ensure they stay on schedule.
- Communicating with Teams: Regularly check in with teams responsible for the work.
- Documenting Outcomes: After completion, document results and feedback to improve future processes.
Effective tracking and follow-up can significantly enhance overall operational efficiency, reinforcing the importance of a structured work order management approach.
Best Practices for Work Order Management
Effective work order management is critical for enhancing productivity and efficiency across various industries. Implementing best practices helps streamline the creation and fulfillment of work orders. Adopting structured approaches ensures that every step in the process is properly addressed, leading to better resource allocation, reduced downtime, and overall improved operational performance. Best practices help businesses identify gaps in their current systems and make necessary adjustments quickly.
Implementing Standard Operating Procedures
Standard Operating Procedures (SOPs) are essential in any work order management process. By defining clear guidelines, they aid in maintaining consistency. When everyone follows the same protocols, errors and misunderstandings are greatly reduced. SOPs create a framework for creating and processing work orders that can be adhered to by all team members.
When developing these procedures, itโs important to involve various teams in the creation process. This collaboration ensures that the SOPs are practical and cover all aspects of work order management. Regular reviews and updates of these procedures are necessary to keep them relevant and effective.
Training Staff on Work Order Processes
An often overlooked yet vital component of work order management is staff training. Employees must understand the importance of their role in the work order process. Training ensures that everyone knows how to create, submit, and manage work orders correctly. It can be beneficial to organize workshops or training sessions focused on software tools used within the organization.
Reinforcement through continuous training sessions fosters a culture of learning. By regularly revisiting training, employees can stay updated on any changes in procedures or technology. This investment in staff knowledge helps reduce errors and promotes accountability.
Utilizing Data Analytics for Performance Tracking
Data analytics plays a crucial role in optimizing work order management. By analyzing metrics such as completion time, resource allocation, and staff performance, organizations can identify trends and areas for improvement. Utilizing data insights allows businesses to make informed decisions to enhance their processes.
For example, tracking the response time for work orders can indicate whether a team needs more resources or training. Tools like Microsoft Power BI or Tableau can be used to visualize data effectively, making it easier for teams to grasp complex information.
Continuous Improvement Strategies
Continual improvement is vital in any organizational process. Regularly assessing work order management practices can uncover weaknesses and opportunities for enhancement. Use feedback from staff involved in the process to identify pain points, as they are on the frontline and best positioned to offer insights.
Implementing strategies such as the Plan-Do-Check-Act (PDCA) cycle can be very helpful. This approach encourages organizations to plan improvements, implement them, check the results, and act on what has been learned. Such a method promotes a proactive culture where the focus is on ongoing advancement rather than reactive measures.
The commitment to best practices is not just about maintaining efficiency; it is about fostering a dynamic workplace where every employee feels empowered to contribute to operational excellence.
Challenges in Work Order Creation
Creating effective work orders is crucial for maintaining operational efficiency, yet several challenges can hinder this process. Recognizing and addressing these challenges helps organizations improve their workflows and minimize disruptions. The following sections will examine common obstacles, highlighting the importance of effective work order creation.
Inadequate Information Gathering
One significant challenge faced during work order creation is inadequate information gathering. This generally occurs when the necessary details are either not collected or insufficiently documented. Without precise and thorough information, the risk of misunderstandings increases, which can lead to delays or incomplete tasks.
To effectively combat this issue, it is essential for teams to develop a clear procedure for gathering information. When generating work orders, detailed descriptions regarding the tasks and required materials should be specified. Furthermore, utilizing checklists can ensure that all pertinent information is recorded before submission. This not only minimizes confusion but also sets a standard for future work orders.
Miscommunication Between Teams
Miscommunication between teams is another prevalent issue impacting work order creation. When different departments do not effectively share information, tasks may not be prioritized correctly, or critical details may be lost following the order's creation.
Implementing regular communication meetings and utilizing platforms such as Slack or Microsoft Teams can promote better collaboration between teams. Encouraging open dialogue ensures that all departments stay informed about ongoing projects and work order statuses. In turn, clearer communication reduces operational bottlenecks and fosters a more harmonious working environment.
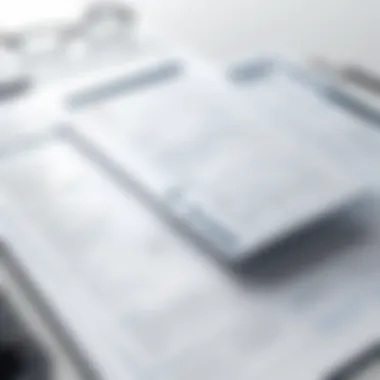
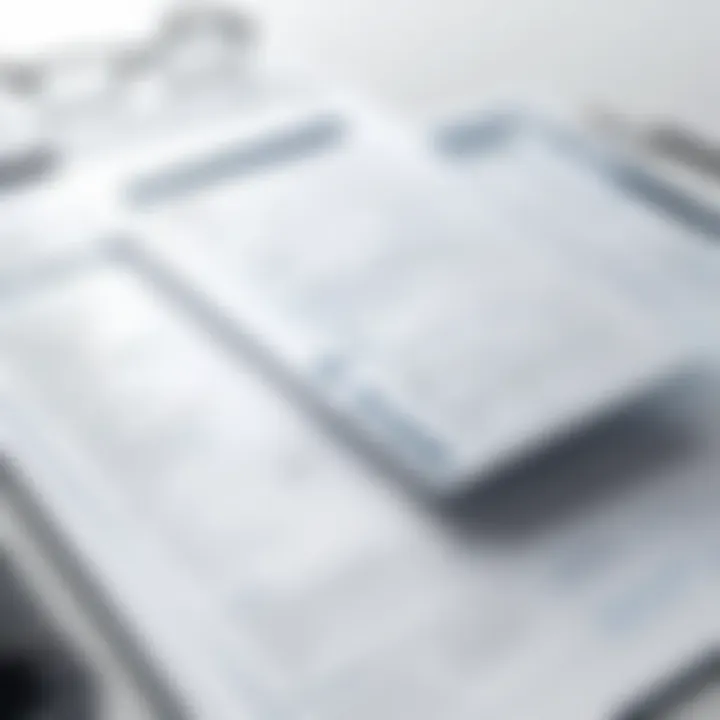
Technical Issues with Software
Technical issues associated with work order management software can also hinder effective order creation. Software glitches, system outages, or user errors can make it difficult for teams to enter or access necessary information. Ultimately, these problems can derail the entire work order process.
To mitigate such technical issues, it is important to invest in reliable software solutions with robust customer support. Regular training on how to use the software can also empower staff to navigate challenges effectively. Establishing a contingency plan for technical disruptions ensures that workflows remain unaffected even during unexpected software failures.
Leveraging Technology in Work Order Management
The role of technology in work order management cannot be overstated. In todayโs fast-paced business environment, leveraging technology streamlines processes, reduces errors, and enhances communication. The integration of modern tools helps professionals manage work orders with greater efficiency. This section delves into the specific elements that can transform how businesses handle work orders, discussing software solutions, mobile applications, and integration with existing systems.
Work Order Management Software Solutions
Work order management software forms the backbone of efficient order creation and tracking. These specialized tools are designed to automate and simplify various tasks associated with work orders. Solutions like UpKeep, ServiceTitan, and FMX are prominent in the market. They provide functionalities for managing requests, assigning tasks, and tracking progress in real-time.
Key benefits of such software include:
- Centralized Information: All data related to work orders is stored in one place, facilitating easy access and updates.
- Automated Notifications: Users receive alerts for task updates, ensuring stakeholders are informed of any changes.
- Analytics and Reporting: Many solutions offer analytical tools that help in understanding work order history and performance metrics.
Using these systems leads to more informed decision-making and improved operational workflows. Furthermore, companies can scale their operations more efficiently by adopting these digital solutions.
Mobile Applications for On-the-Go Management
The rise of mobile applications has brought a new level of convenience to work order management. Apps designed for mobile use, such as Maintenance Connection and MobiWork, allow users to access and manage work orders from anywhere, at any time.
These applications provide several advantages:
- Real-Time Updates: Field staff can receive work orders and report back on the status immediately, fostering effective communication.
- User-Friendly Interfaces: Many mobile platforms focus on ease of use, ensuring that team members can navigate the app with little training.
- Offline Functionality: Some apps allow work order updates even when there is no internet connection, syncing data once the connection is restored.
With mobile solutions, businesses can enhance productivity and ensure that work orders are handled promptly.
Integrating with Other Business Systems
Integrating work order management systems with other business software is crucial for creating a cohesive workflow. This integration can include linking with customer relationship management (CRM) systems, enterprise resource planning (ERP) systems, or inventory management software like SAP or Salesforce.
Benefits of such integration include:
- Data Consistency: Ensures that information is synchronized across various platforms, reducing the likelihood of errors or discrepancies.
- Streamlined Processes: Combining systems can automate processes, such as updating inventory levels based on completed work orders.
- Enhanced Reporting: Users gain comprehensive insights by analyzing data from multiple sources, informing better strategic decisions.
Overall, integrating work order management with other systems facilitates a smoother operation, reducing administration time and enhancing overall efficiency.
"Adopting technology in work order management not only increases efficiency but also helps in maintaining high standards of service delivery."
Future Trends in Work Order Management
Understanding the future trends within work order management is vital for organizations aiming to adapt to rapidly changing environments. Future trends will shape how companies manage work orders, streamline processes, and enhance operational efficiencies. Attention to these trends allows businesses to not only keep pace with emerging technologies but also leverage them to gain a competitive edge. This section will explore key components: the adoption of artificial intelligence, enhanced data security measures, and the emphasis on user experience.
Adoption of Artificial Intelligence
Artificial Intelligence (AI) has the potential to fundamentally transform work order management. By implementing AI technology, organizations can automate routine tasks and improve decision-making. AI can analyze vast amounts of data to predict demand, streamline workflows, and reduce human error. For instance, AI algorithms can prioritize work orders based on urgency and resource availability, enabling more efficient task prioritization.
Moreover, predictive analytics can suggest preventive maintenance schedules, thereby minimizing downtime and repair costs. While the integration of AI requires initial investment, the long-term return may significantly exceed these costs. Adopting AI solutions in work order management not only improves efficiency but also fosters an environment focused on informed decisions.
Enhanced Data Security Measures
As work order management becomes more digitized, data security emerges as a crucial component. Organizations must protect sensitive information related to work orders, including user credentials and operational data. Improved data security measures are essential to safeguard against cyber threats and breaches, which can result in financial losses and reputational damage.
Implementing advanced security protocols, such as encryption and multi-factor authentication, is becoming standard practice. Additionally, regular security audits and employee training on data protection can greatly enhance security posture. By prioritizing data security in work order management, organizations can build trust with their clients and stakeholders, ensuring operational integrity.
Emphasis on User Experience
User experience plays a central role in the effectiveness of work order management systems. A well-designed interface can significantly enhance user engagement and efficiency. When users find a system intuitive and easy to navigate, the likelihood of errors diminishes. This is especially important as teams begin to rely more heavily on mobile applications for managing work orders remotely.
Organizations must seek ongoing feedback from users to continuously improve the system. Features such as customizable dashboards, simplified forms, and mobile compatibility are essential in enhancing overall user satisfaction. Investing in user experience not only improves team morale but also leads to better adherence to processes, ultimately elevating operational efficiency.
Culmination
To encapsulate the relevance of the topic, the conclusion plays a crucial role in reaffirming the significance of effective work order practices within business operations. A well-crafted work order is not merely about capturing tasks but also about ensuring that operations run smoothly and efficiently. When properly constructed, work orders facilitate clear communication among team members, minimize delays, and enhance productivity across various sectors.
Recap of Key Points
Throughout this article, we addressed several pivotal elements related to creating work orders:
- Definition and Importance: We established what work orders are and how they function as communication tools within a business medium.
- Types of Work Orders: Preventive, corrective, and emergency work orders serve different purposes and underscore the importance of adaptability.
- Key Components: Elements such as identification information, task descriptions, and estimated completion time are fundamental.
- Steps to Create Effective Orders: Gathering necessary information and choosing the right tools are steps to ensure clarity.
- Best Practices: Training staff and implementing standard operating procedures can significantly improve work order management.
- Challenges: Recognizing and overcoming challenges is essential for seamless creation processes.
- Technological Trends: Using modern software solutions and mobil apps can enhance efficiency in the management of work orders.
- Future Developments: Trends like AI and improved data security are set to redefine how businesses handle work orders.
Final Thoughts on Effective Work Order Practices
Effective work order practices can lead to marked improvements in overall productivity. It is imperative for organizations to embrace continuous improvement strategies, not just in creating work orders but also in their wider operational frameworks. As businesses evolve, integrating technologies, enhancing user experiences, and focusing on data security will be paramount. By establishing and refining these practices, professionals can better navigate the complexities of modern operations. The journey does not end with creating a work order; it continues with evaluating its effectiveness and adjusting as needs change.