Enhancing Business Efficiency with Tool Tracking Software
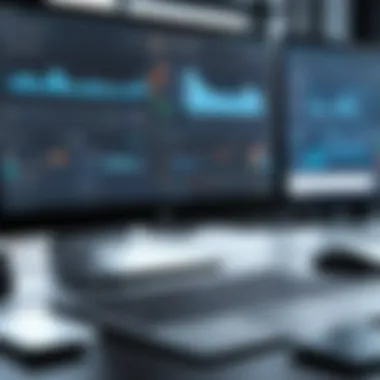
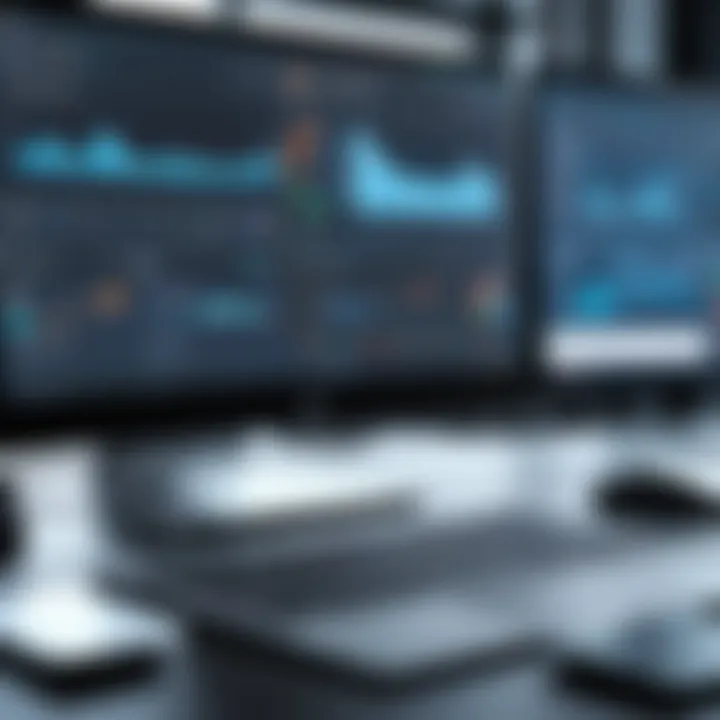
Intro
In the fast-paced world of business, the significance of every tool, screw, and piece of equipment cannot be overstated. Without efficient management of these small tools, organizations risk losing time, money, and ultimately, competitive advantage. Small tool tracking software has emerged as a vital component for companies looking to streamline their operations, offering pinpoint visibility into resources that are often overlooked.
With the use of specialized software, businesses can not only track the location and availability of tools but also gain insights into their operational performance. These systems work like a well-oiled machine, ensuring that every tool is accounted for, decreasing the likelihood of delays, and enabling proactive maintenance to extend tool longevity. As firms grapple with the challenges of economic fluctuations and ever-evolving industry standards, investing in small tool tracking software becomes not just wise but essential.
This article aims to dissect the myriad features and benefits of such tools, while addressing the critical aspects that decision-makers should consider before integration. In a landscape where efficiency reigns supreme, embracing this technology may very well turn out to be the game changer that keeps a business competitive.
Functionality
Overview of key features
When it comes to small tool tracking software, functionality is king. Here are some key features one should expect:
- Real-time tracking: This ensures that every tool is monitored and its location updated instantly. No more searching high and low for that elusive wrench.
- Inventory management: With a robust inventory system, businesses can see what tools they possess, what needs repairing, and what might be due for replacement.
- User access controls: Different team members often require varying levels of access. Having a system that allows for this granularity means sensitive information can be better protected.
- Barcoding or RFID integration: By utilizing barcoding or radio-frequency identification (RFID), tracking tools becomes even simpler and more accurate.
- Reporting and analytics: Data-driven insights into usage patterns can help identify areas for improvement, ensuring that tools are being used effectively and resources are allocated wisely.
These features, when combined effectively, not only increase accountability but also enhance overall operational efficiency.
How well the software meets user needs
The effectiveness of small tool tracking software hinges on how well it can cater to the unique needs of different organizations. Companies in construction, manufacturing, or even service industries may possess varying requirements.
It’s essential to evaluate how a software solution meets specific company needs:
- Customization options: Can the system be tailored? Generic solutions often miss the mark, while adaptable software allows businesses to select features that are relevant to their operations.
- Ease of use: The best software is intuitive. If employees struggle to navigate the platform, it could lead to resistance or errors.
- Integration capabilities: Compatibility with existing systems like ERP or project management software is crucial. Organizations shouldn't have to uproot their established practices for a new solution.
- Customer support: The need for ongoing support cannot be overlooked. Reliable customer service can assist with training, troubleshooting, and system updates.
In a nutshell, to ensure small tool tracking software works seamlessly, it should align closely with the daily operations of users, enhancing their workflow rather than complicating it.
Scalability
Adaptability for growth
Businesses aren't static; they evolve. Whether it’s expanding into new markets or increasing tool inventory, the scalability of tracking software is paramount. A robust tool should be able to adjust to the changing needs of an organization without requiring a total system overhaul.
In practical terms:
- User growth: As teams expand, the software must support additional users without performance issues. This flexibility is essential in fast-growing sectors.
- Feature add-ons: Organizations may wish to incorporate advanced features as their needs change over time. A solution that allows for easy add-on modules can be invaluable.
Options for additional features or modules
As businesses evolve, so too may their needs for additional features in their small tool tracking software. Possible modules or enhancements might include:
- Maintenance scheduling: This feature helps automate upkeep, further prolonging the lifespan of tools.
- Project management integration: Linking to project management tools can provide a holistic view of materials and tools needed for specific jobs.
- Mobile access: With a mobile-friendly interface, workers can easily access data on the go, facilitating quicker decision-making.
Investing time into selecting a tracking software that grows with the needs of the organization can save businesses from future headaches down the line.
"Choosing the right small tool tracking software isn't just a decision; it's a step towards future-proofing your business operations."
As firms navigate through an increasingly complex business landscape, the integration of small tool tracking software stands out as an essential tactic for enhancing efficiency and accountability.
The right solutions and strategies not only optimize existing workflows but also set the stage for sustainable growth. Through thoughtful consideration of functionality and scalability, decision-makers can position their organizations to be more effective in their daily operations.
Foreword to Small Tool Tracking Software
The landscape of modern businesses is shifting rapidly, driven by the need for efficiency and precise resource management. In this context, small tool tracking software has stepped into the limelight, offering solutions that streamline operations and enhance productivity. Organizations, be they construction companies, manufacturers, or service providers, are recognizing the potential of these tools to not only track assets but also optimize workflow processes.
Definition and Purpose
Small tool tracking software is a specialized solution designed to monitor and manage small tools and equipment, such as power drills, hammers, or even safety gear. This software allows businesses to keep tabs on the location, status, and usage of their tools, ensuring that items are not misplaced or left unused for long periods. The primary purpose of this software is to enhance efficiency. When tools are readily available and properly maintained, projects can be completed faster, saving both time and money.
"The real cost of tools isn’t in their purchase, but in their management and utilization."
With robust tracking, businesses can also improve accountability, making it clear who is using what tools at any given time. This can prevent theft or loss, which otherwise cuts deeply into profit margins. Understanding this definition is the first step in appreciating the broader benefits of adopting such technology.
Historical Context and Evolution
To truly grasp the significance of small tool tracking software, it's important to look back at how we arrived at this technological pivot point. Initially, companies relied on manual methods to track their tools—think paper logs and ledgers. While effective in their own right, these systems were often plagued by inaccuracies and inefficiencies.
With the introduction of digital databases in the late 20th century, businesses began to move towards electronic tracking systems. These technologies advanced, laying the groundwork for the sophisticated software solutions we see today. It's also worth noting the shift towards mobile technology, simplifying how employees access tracking data. Nowadays, many small tool tracking solutions operate via smartphone applications, creating ease of use that was previously unimaginable. The evolution from basic manual tracking to intelligent software systems reflects the broader trend of digitization in business.
By understanding the roots and rationale behind small tool tracking software, organizations can better appreciate its potential. This framework can help businesses navigate toward solutions that not only meet their immediate needs but also prepare them for future challenges.
Key Features of Small Tool Tracking Software
When it comes to small tool tracking software, understanding its key features is like finding the needle in the haystack. These features serve as the backbone for optimizing efficiency and ensuring that resources are properly managed throughout the operation. From inventory management capabilities to effective reporting, these tools present a robust suite of functionalities that can make or break the efficiency of an organization.
Inventory Management Capabilities
Inventory management is one of the most crucial aspects of any business, and small tool tracking software shines in this area. It not only allows businesses to monitor the availability of their tools but also provides alerts when items are running low. Imagine a construction site where tools are frequently mislaid or lost. With a solid inventory management system in place, such as those offered by brands like ToolWatch or GigaTrak, supervisors can access a real-time overview of what’s being used, when, and by whom. This minimizes the likelihood of overbuying or, worse, running out of critical tools during a project.
Furthermore, effective inventory management can enable better planning for future purchases. If a certain tool is used more frequently than expected, organizations can adjust their buying strategy accordingly.
Real-Time Tracking and Updates
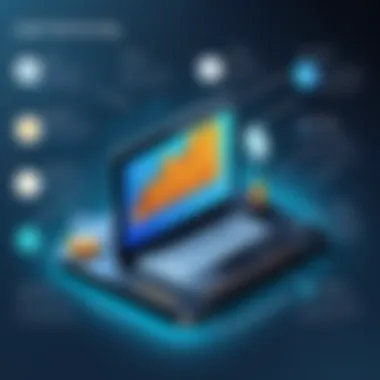
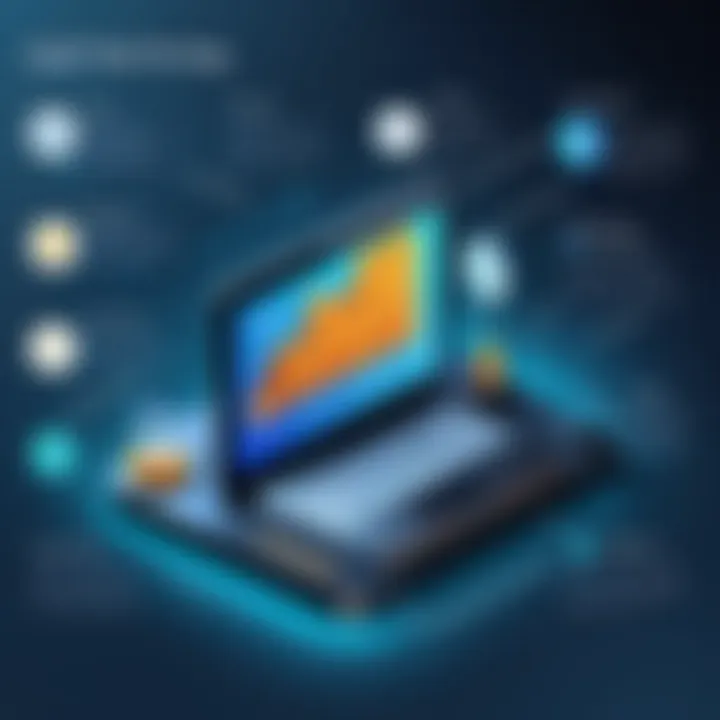
Real-time tracking represents another layer of sophistication embedded in small tool tracking software. This feature essentially enables organizations to know the precise location and status of a tool at any given moment. When tools are tagged with RFID or QR codes, they can be scanned and logged into the system as they move from one user to another.
This immediacy is vital for avoiding loss and inefficiencies. Imagine being in a fast-paced environment where every minute counts. Being able to locate a missing tool quickly without the back-and-forth search not only saves time but also enhances productivity. Assets can be tracked using mobile applications, enabling user interventions in real-time as needed. As a result, workflows are streamlined and bottlenecks are avoided, fostering a more effective work environment.
User Access and Permissions
Another significant feature of small tool tracking software is the management of user access and permissions. In any organization, understanding who has access to what tools is fundamental in maintaining both order and accountability. By implementing user permissions, organizations can ensure that only authorized personnel can check out tools, which greatly reduces the risk of loss or theft.
Moreover, this capability allows for a tiered access structure. For instance, project managers may have the authority to allocate resources, while junior staff members would only have limited access. This not only promotes a better hierarchy but also encourages responsibility among employees. In turn, the organization fosters an atmosphere where tools are treated with respect.
Reporting and Analytics Features
Lastly but importantly, reporting and analytics features provide insight into usage patterns and resource allocation within the organization. This data can be invaluable for long-term planning and optimization strategies. Small tool tracking software can generate reports detailing usage rates, downtime, and even the costs tied to broken or lost tools.
By analyzing this data, organizations can identify trends that might otherwise go unnoticed. For example, if a particular tool consistently requires repair or replacement, it might signal that it’s either being misused or isn’t the right fit for the tasks at hand. Addressing these issues before they become problematic can save companies significant costs down the line.
"The right tool in the right place at the right time is the secret sauce for optimizing efficiency in any operation."
In summary, the key features of small tool tracking software are not just conveniences—they represent essential elements for informed decision-making and operational success. By streamlining inventory management, facilitating real-time tracking, implementing effective user access management, and enabling detailed reporting, these tools empower organizations to minimize waste and improve accountability. Such features are not simply beneficial; they are fundamental for navigating the complexities of contemporary business environments.
Benefits of Using Small Tool Tracking Software
In an era where every second counts and resources are tight, the application of small tool tracking software brings a slew of advantages to organizations striving to improve their operational efficiency. The core benefits encompass much more than just enhanced visibility into inventory; they touch virtually all facets of business, from cost management to safety compliance. Organizations that embrace these solutions often find themselves ahead of the curve, ready to pivot in an increasingly complex environment. Here, we will delve into key areas where small tool tracking software can make a significant impact.
Enhancing Efficiency and Productivity
Small tool tracking software stands as a beacon for boosting overall operational efficiency. By offering real-time tracking capabilities, employees can locate tools, equipment, or supplies with minimal hassle. This means less time spent searching for a misplaced tool or waiting for a replacement, which can lead to a remarkable increase in productivity across teams.
For instance, consider a construction site where multiple teams are simultaneously working. Each hour lost searching for tools can translate into substantial wage costs. By utilizing barcode scanning or RFID technology, personnel can effortlessly identify the tool's location and availability. Consequently, this immediacy not only speeds up work processes but also fosters a seamless flow of operations, ensuring that deadlines are met without compromising quality.
Reducing Costs and Waste
Implementing small tool tracking software inherently drives down costs associated with inefficiencies. The ability to maintain an accurate inventory in real-time means that organizations can avoid over-purchasing or unnecessary rentals. Furthermore, by accurately tracking the usage of tools, firms can identify which ones are used frequently versus those that just take up space in the warehouse.
Wasted resources also decrease, as organizations can better manage their assets. If an organization can avoid replacing lost tools repeatedly, it directly saves money that can be redirected towards other critical areas. Not to mention, this also sorts out maintenance schedules and minimizes wear and tear, prolonging the lifespan of tools and equipment.
"Efficiently tracked tools are the backbone of cost reduction; less waste means more funds to invest back into the business.”
Improving Accountability and Traceability
With the rise of digital systems comes a new level of accountability. Small tool tracking software records each instance of tool usage, ensuring that businesses know who is using what and when. This traceability not only helps in locating missing equipment but also serves as a valuable tool for performance evaluation.
When tools are checked out and returned with identifiable user data, accountability is inherently bolstered. If a tool is broken or lost, organizations can efficiently trace back to the user responsible, enabling a clear pathway for responsibility and resolution. This not only promotes a culture of ownership among employees but can also lead to behaviors that minimize loss and ensure proper care for equipment.
Facilitating Compliance and Safety Standards
In today's regulatory landscape, compliance is more crucial than ever. Small tool tracking software can be integrated with safety protocols to ensure that all tools meet industry standards. This can easily flag tools that are approaching the end of their operational lifecycle or tools that require calibration before use.
Moreover, organizations can maintain a comprehensive field of safety practices through checklists incorporated within the software. Employees can receive reminders for when tools need maintenance or when safety check-ups must occur. Taking proactive steps in maintenance not only fulfills regulatory requirements but also fosters a culture of safety—ensuring that the workplace remains hazard-free and efficient.
In summary, the advantages of employing small tool tracking software are manifold, each feeding into the larger aim of enhancing business efficiency and resource management. By understanding and implementing these benefits, organizations can streamline operations, better allocate resources, and pave the way for success in an increasingly competitive landscape.
Factors to Consider When Selecting Software
When sifting through the myriad of options for small tool tracking software, it is crucial to pinpoint the factors that will maximize efficiency and bolster day-to-day operations. Organizations often face pressure to streamline processes while ensuring that each penny spent yields substantial returns. The decision-making process is rarely straightforward; hence, a thorough understanding of specific elements ensures informed choices potentially saving time and money in the long run.
Scale and Complexity of Operations
Not all businesses are cut from the same cloth, especially when it comes to operations. For example, a construction company with dozens of job sites scattered across a region requires a vastly different tool tracking solution than a boutique design studio managing a couple of projects at a time. Assessing the scale and complexity of your operations will guide you toward software that can handle your unique demands.
A few considerations here might include:
- Number of tools and assets: Larger inventories necessitate comprehensive management features, whereas smaller outfits can operate efficiently with basic functionalities.
- Multiple locations: Companies operating across various sites may need real-time updates that allow for efficient resource sharing without the hiccups of miscommunication.
Balancing these aspects can significantly influence operational efficiency.
Integration Capabilities
In the ever-evolving digital landscape, software that doesn't talk to other crucial applications can become an albatross around your neck. Take, for instance, a scenario where an organization’s HR system is disconnected from its inventory tools —data is siloed, leading to inefficiencies. A solid small tool tracking software should integrate seamlessly with existing systems, whether it’s asset management tools, financial software, or project management applications.
When evaluating integration capabilities:
- API Availability: Check if the software offers APIs that can communicate with other systems.
- Pre-built Integrations: Some software come equipped with common integrations, making the connection process smoother.
Finding a solution that fits snugly within your current ecosystem will make life easier for everyone involved.
User-Friendliness and Support
Let’s face it—if a tool is as complicated as a Rubik's Cube, it’ll likely gather dust instead of helping your staff. A user-friendly interface is non-negotiable. Employees should feel comfortable navigating the platform, as training them shouldn’t feel like wrangling cats.
Here’s what to look for:
- Intuitive Design: A clean layout reduces the learning curve, ensuring that users can take advantage of essential features without extensive training.
- Support Services: Consider the support options available. Whether it’s live chat, email, or a knowledge base, prompt assistance can be invaluable when the going gets tough.
Cost Implications and Budget Constraints
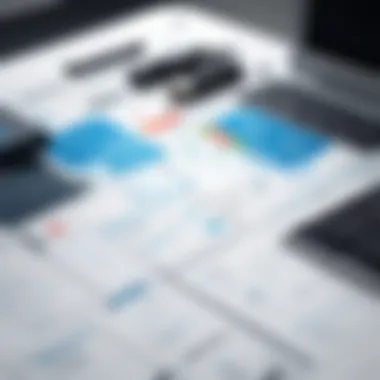
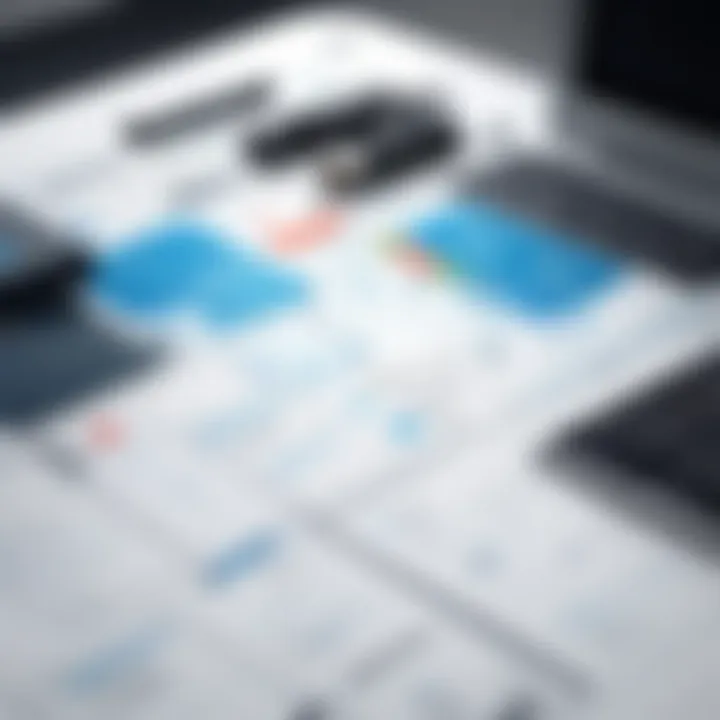
“Penny wise, pound foolish” is more than just a saying; it’s a cautionary tale. Selecting software solely based on the lowest price could lead to significant headaches and expenses down the line. It's essential to analyze the potential return on investment (ROI) and weigh features against costs.
Consider these factors:
- Tiered Pricing: Look for software that offers different pricing tiers based on features. This allows you to pick a package that aligns with your current needs while providing the ability to scale later.
- Hidden Costs: Always clarify the total cost of ownership, including setup fees, training costs, and subscription hikes, to avoid surprises.
By marrying budget constraints with necessary functionalities, companies can maximize efficiency without breaking the bank.
"Choosing the right small tool tracking software is less about finding the cheapest option and more about making an investment that pays dividends over time."
Each of these factors intertwines to form a comprehensive decision-making framework. Neglecting any aspect could lead to a disconnect that veers organizations off course, impacting overall productivity.
Deployment Models for Small Tool Tracking Software
When considering the integration of small tool tracking software, the deployment model is a crucial aspect that can greatly impact the overall effectiveness and user experience of the solution. The decision between cloud-based solutions and on-premise software involves not just technical specifications, but also considerations around cost, scalability, accessibility, and data security. Each deployment model offers its own unique benefits, which can lead to more efficient operations and ultimately enhance productivity in various environments.
Cloud-Based Solutions
Cloud-based small tool tracking software has gained traction in recent years, becoming a preferred option for many businesses. These solutions are hosted on remote servers and accessed via the internet. Here are several key reasons why organizations might lean towards cloud-based systems:
- Accessibility: One of the standout features is the ability to access data from anywhere, at any time, provided there’s internet connectivity. This is particularly beneficial for businesses with multiple locations or for teams that operate remotely.
- Scalability: As a company grows, its tool tracking needs will likely evolve. Cloud solutions can be easily scaled up or down to accommodate changes in operations without the hassle of hardware updates.
- Lower Initial Costs: Generally, cloud solutions involve less upfront cost. Instead of purchasing expensive servers and software licenses, companies can opt for a subscription model with predictable pricing.
- Automatic Updates: Maintenance and updates are managed by the software provider, saving businesses time and ensuring they are using the latest features and security protocols.
However, companies must also consider potential drawbacks such as data privacy and internet dependency. With so much sensitive information transmitted online, businesses need to vet providers carefully to ensure robust security measures are in place.
"Choosing cloud-based solutions can provide flexibility and efficiency, but organizations must weigh these benefits against their unique needs and challenges."
On-Premise Software
On-premise software installations offer a different set of advantages and may be preferable in specific contexts. This model involves installing and running the software on a company's own servers. Here are important considerations:
- Control over Data: One of the primary reasons organizations might prefer on-premise solutions is the level of control it provides. Companies can implement their own security measures, managing access to sensitive information directly.
- Customization: On-premise installations often allow for greater customization. Businesses with unique processes may find that an on-premise solution can be tailored to fit their specific workflows more accurately than a cloud-based option.
- Integration with Existing Infrastructure: Companies already invested in on-premise systems may find it easier to integrate new tracking software into their existing infrastructure, avoiding possible incompatibilities with other software used.
- Cost Considerations: While initial costs can be higher than their cloud counterparts, businesses might find long-term savings if they require extensive usage, since there are usually no recurring subscription fees.
Yet, it’s important to acknowledge that on-premise solutions require dedicated IT resources for maintenance, upgrades, and troubleshooting, which can add to operational complexity.
Integration with Existing Systems
In the modern business landscape, integrating small tool tracking software with existing systems is crucial. This undertaking often determines the success of the implementation process and ultimately affects the efficiency of overall operations. The ability to sync seamlessly with other organizational tools can be a game changer, as it allows for a holistic view of asset management and resource allocation.
Benefits of Integration
When a small tool tracking system aligns with other software solutions, such as asset management tools and financial applications, it creates a streamlined workflow that enhances productivity. Here are some major benefits:
- Centralized Data Management: A single source of truth becomes attainable. Information from various departments can be displayed in one interface, reducing the odds of duplication or errors.
- Improved Communication: When tools speak the same language, it fosters better collaboration among teams. Everyone is on the same page, which can mitigate many misunderstandings.
- Faster Decision-Making: Integrated systems provide timely insights. Management can quickly assess inventory levels, financial forecasts, and operational efficiencies without rummaging through disparate databases.
- Maximized ROI: By utilizing existing tools and adding just the necessary functionalities, businesses can maximize their return on investment. It’s not about starting from scratch but rather building on what is already in place.
However, before diving headfirst into integration, some considerations come into play.
Considerations for Successful Integration
The process is not without its challenges. Here are a few key factors to ponder:
- Technical Compatibility: Always ensure that the new software aligns with the current infrastructure. Sometimes, legacy systems hinder progress, and careful assessment is needed to address these discrepancies.
- Potential Downtime: Integration efforts might require time away from regular operations. Effective planning can mitigate these risks, but it’s a factor that warrants consideration before proceeding.
- Vendor Support: Not all software vendors are created equal. Their commitment to supporting integration efforts can vary significantly. It's wise to choose a partner whose services align with your operational needs.
- Training Needs: If new systems are introduced, sufficient training for employees will be essential. A well-informed staff will reduce resistance to change and help in smoother transitions.
In summary, integrating small tool tracking software with existing systems paves the way for improved efficiency and productivity. The journey is filled with both possibilities and pitfalls, but with careful strategizing, businesses can overcome the hurdles and create an environment conducive to success.
Compatibility with Asset Management Tools
For businesses that have already invested heavily in asset management systems, ensuring that new small tool tracking software is compatible is indispensable. When these tools work well together, it not only prevents the frustration of incompatible systems but empowers businesses with more valuable insights about their assets.
Integrating Asset Insights
- Seamless merging of data from asset management systems offers a comprehensive overview of what tools are available and where they’re located.
- Tracking how often tools are used and identifying their lifecycle can assist in making informed decisions about purchasing new assets or retiring old ones.
- Data-driven Decisions: By having all valuable data at hand, businesses can make informed decisions on asset allocation, maintenance schedules, and budgets.
Linkage to Financial Software
Coupling small tool tracking software with financial systems is another layer of optimization. The linkage to financial software brings forth essential benefits that enhance overall operational efficiency.
- Budget Tracking: By integrating tool tracking with financial software, organizations can automate the reporting of expenditures related to tool usage, fostering better budget management.
- Expense Reporting: Having real-time data enables quicker responses to any discrepancies in reported costs compared to budgeted amounts. This function can significantly streamline financial audits.
- Forecasting: Historical data on tool usage paired with financial analytics can lead to improved forecasting models that better align budgetary needs with actual spending.
Establishing these linkages not only magnifies the efficiency of resource management but ensures that every dollar spent is accounted for in the grand scheme of operations.
Challenges of Implementing Small Tool Tracking Software
When businesses consider the integration of small tool tracking software, they must navigate several obstacles that can hinder this process. Understanding these challenges is vital as it equips organizations with the knowledge needed to tackle them head-on.
Resistance to Change within Organizations
Often, the greatest barrier to adopting new software isn’t the technology itself, but rather the people involved. Resistance to change is common in many organizations. Employees might feel that introducing tool tracking software disrupts established workflows or threatens their job security. This can particularly be the case in companies with long-standing practices that have worked, albeit perhaps not as efficiently as they could.
Moreover, nurturing a culture of innovation and adaptability can be a hurdle. For example, when a construction company sought to implement tool tracking software, staff initially resisted the change as they felt overwhelmed by learning a new system. They were used to physical logs and word-of-mouth communication, and shifting to digital can feel like learning to walk again. To overcome this, organizations need to focus on comprehensive training programs and emphasize the long-term benefits of the software, such as increased efficiency, lower costs, and improved accountability. Encouraging open dialogue and addressing concerns can smooth the transition.
Cost of Implementation and Training
Cha-ching! The cost that comes with implementing small tool tracking software often gives businesses quite a scare. It's not just the sticker price of the software itself, but also the hidden expenses like training sessions, potential system upgrades, and the time spent during the transition phase. When a company like XYZ Corp looked into software solutions, they had to navigate various financial aspects that seemed daunting at first.
Training, in particular, adds another layer of complexity. It's essential to ensure that employees are comfortable and proficient with the new tools. If the training is insufficient, it can lead to misuse or ineffective practices, ultimately negating any gains from implementing the software in the first place.
To minimize costs and disruptions, businesses can consider a phased approach to implementation. Start with a small pilot project rather than a full-scale rollout. This strategy not only helps in identifying potential issues but also allows for spreading the training costs. With hands-on experience, staff may become advocates of the software, transforming skepticism into approval.
"The only thing constant in life is change; however, managing that change is where true competence lies."
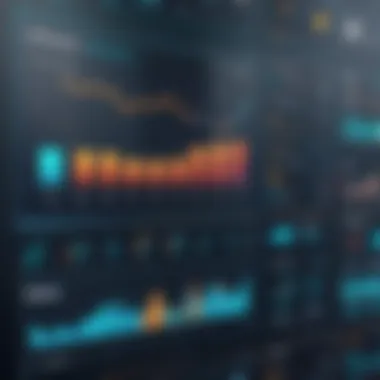
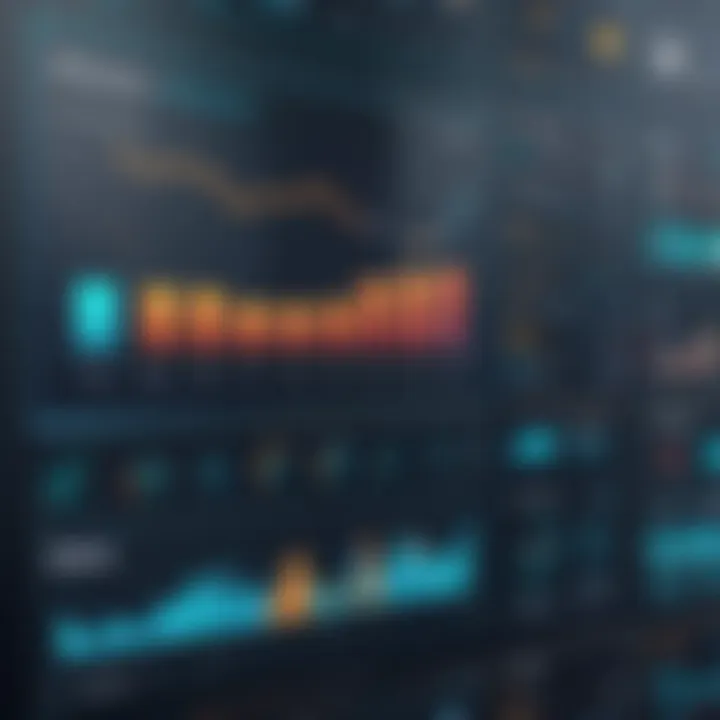
Regulatory and Compliance Considerations
When it comes to small tool tracking software, regulatory and compliance considerations are crucial for organizations to take into account. Compliance isn’t just about following the rules; it's tied intricately to operational integrity and efficiency. Having appropriate tracking software helps ensure that tools are not only accounted for but also used safely and legally. In fast-paced industries, where stakes are high, neglecting compliance can lead to severe repercussions, including fines, operational hiccups, or worse, reputational damage.
Relevance of Industry Standards
Industry standards act as the backbone of regulatory compliance. They provide frameworks that businesses can use to benchmark their practices against recognized norms and ensure accountability. For instance, standards set by organizations such as ISO (International Organization for Standardization) guide companies in maintaining quality, safety, and efficiency in their operations.
Understanding and integrating these standards into tool tracking practices can have numerous benefits:
- Enhanced Credibility: Being compliant boosts your company’s credibility with clients and stakeholders, showing that you take regulations seriously.
- Risk Mitigation: Aligning with industry standards lowers the chances of penalties and legal issues. You essentially have a roadmap to navigate through compliance complexities.
- Streamlined Processes: Many standards encourage best practices that lead to operational efficiencies. Incorporating these can drive internal processes, making them smoother.
In fields like construction, healthcare, or manufacturing, where tools play a pivotal role, failure to adhere to these standards could result in accidents or violations with steep consequences.
Data Privacy and Security Issues
Data privacy and security have become critical touchpoints for businesses, especially with the rise of technology solutions. Small tool tracking software often collects vast amounts of data, from user interactions to inventory statistics. Managing this data responsibly isn’t merely good practice; it’s a legal obligation under regulations like GDPR (General Data Protection Regulation) in Europe and various others worldwide.
Taking these considerations into account can protect organizations from both financial losses and reputational damage. Here’s what businesses should aim for regarding data privacy and security:
- User Consent: Always ensure that users provide consent for their data collection and clarify how their information will be used.
- Data Encryption: Use encryption standards to safeguard data during transmission and at rest. This adds a layer of protection against unauthorized access.
- Regular Audits: Implement regular audits of both data security measures and the software itself; this helps in identifying vulnerabilities that could be exploited.
- Compliance Training: Conduct training sessions for employees to familiarize them with data privacy policies and responsibilities.
"By ensuring data compliance and securing private information, organizations can build trust and loyalty among their customers, which is invaluable in today’s market."
In summary, regulatory and compliance considerations around small tool tracking software are not just about avoiding pitfalls; they’re opportunities for businesses to elevate their operational standards, safeguard their data, and reinforce their market stance. Ignoring them may not only stall efficiency; it can significantly hinder growth.
Future Trends in Tool Tracking Technology
As small tool tracking software continues to evolve, it's critical to understand the future trends shaping its development and application. Businesses that keep an eye on these trends can stay ahead of the curve, ensuring their tools and resources are managed with maximum efficiency. In this section, we will discuss how AI, automation, and the Internet of Things (IoT) play pivotal roles in the transformation of tool tracking technology.
Emergence of AI and Automation in Tracking
The integration of artificial intelligence in tool tracking software is not just a passing trend; it’s becoming a cornerstone of smarter operations. AI can sift through massive amounts of data quickly and accurately, allowing businesses to spot inefficiencies they might have previously overlooked. For instance, imagine a bakery using tracking software that leverages AI. This system can analyze tool usage patterns, predict peak times, and suggest optimal scheduling for equipment maintenance. The result? Fewer breakdowns and a smoother operation.
Moreover, automation streamlines routine tasks that often bog down productivity. By automating inventory updates, businesses can ensure that their records reflect real-time tool availability without manual input. For example, if a power drill is removed from the storage, the system can instantly adjust stock levels, facilitating better decision-making on re-orders.
"Efficiency isn't just about cutting costs; it's about intelligently allocating resources for the best outcome."
But implementing AI and automation requires careful planning. Businesses should consider their specific needs and the software's capabilities. Not every small tool tracking software will offer the same level of AI integration, and not all companies may need advanced features. A construction firm, for example, might find value in predictive analytics that suggests when tools are likely to need repairs based on usage history.
IoT Integration for Enhanced Monitoring
The IoT is another powerful ally in the quest for optimizing tool tracking. When tools are equipped with smart sensors, they can communicate their status in real-time. This connectivity allows businesses to monitor tool location, condition, and usage patterns from anywhere, at any time. For example, a landscaping company can keep track of all their mowers across multiple job sites, ensuring they know exactly where each unit is located.
These smart tools not only report their whereabouts, but they also inform users about maintenance needs. If a saw starts to overheat due to excess use, it can send an alert. This feature not only prevents equipment failure but also ensures that projects stay on schedule.
The combination of IoT and tool tracking leads to improved asset management. When tools can be tracked and managed more efficiently, organizations can limit their purchases to the tools they genuinely need — no more duplicating what’s already in the shed.
In summary, understanding and leveraging future trends like AI and IoT can significantly enhance the capabilities of small tool tracking software. Keeping pace with these advancements enables businesses to not only increase accountability and efficiency but also foster a more proactive approach to resource management.
Success Stories and Case Studies
Success stories and case studies play a pivotal role in understanding the real-world impact of small tool tracking software. They provide concrete examples of how various companies have implemented these systems and the ensuing benefits. Through these narratives, organizations can glean valuable insights and practical lessons, which serve as a guide for their own implementations of tool tracking solutions. In a world where efficiency and accountability are paramount, these stories illuminate the path to optimizing operations with small tool tracking methods.
Examples from Various Industries
When exploring successful implementations across different sectors, one can observe a range of innovative strategies and outcomes. For instance:
- Construction Industry: A notable construction firm faced challenges with misplaced smaller tools, resulting in costly delays. They adopted a comprehensive tracking system utilizing RFID technology. As a result, they reported a 30% reduction in lost equipment and an improvement in project timelines. The software facilitated not just tracking but also facilitated usability analysis of tools, further enhancing operational workflow.
- Healthcare: A hospital integrated small tool tracking software to manage surgical instruments. Through the introduction of barcode scanning linked to a central inventory database, they saw a 25% reduction in time spent locating instruments during surgery. This efficiency contributed to better patient outcomes and minimized operating room delays.
- Manufacturing: An automotive manufacturer faced inefficiencies due to untracked hand tools in a highly competitive market. They implemented a cloud-based tool tracking system that provided real-time visibility of tool usage. This led to a 15% increase in production efficiency, demonstrating how vital it is to monitor tool allocation effectively.
These different scenarios underscore how small tool tracking software transcends industry boundaries, delivering tailored solutions that drive success.
Lessons Learned from Implementations
From various case studies, several key lessons emerge that can guide organizations considering tool tracking software implementation:
- Need for Customization: Companies should carefully consider the unique dynamics of their operations. For example, a one-size-fits-all solution may not yield optimal results. Customizing features to match specific requirements leads to better adoption and utilization.
- Training and Onboarding: Successful case studies underscore the necessity of comprehensive training for staff. Only when team members are adequately familiar with the software can they utilize it to its full potential. Poor onboarding leads to underutilization and frustration, which can offset the benefits of the software.
- Integration with Existing Systems: Many organizations found that seamless integration with current systems augmented efficiency. Those that did not account for compatibility faced hurdles that compromised the tracking process. An integrated approach ensures data consistency and enables better decision-making.
- Continuous Feedback Loop: Businesses that adopted a culture of continuous improvement saw the best outcomes. Actively seeking feedback from users throughout the implementation process allowed for adjustments and enhancements, driving ongoing optimization in tool management practices.
"What works for one may not work for another, but learning from others' journeys can illuminate your path to success."
End
In the fast-paced world of modern business, small tool tracking software emerges as a cornerstone for optimizing operational efficiency. The significance of such software extends beyond mere inventory management; it encapsulates the essence of accountability, resource allocation, and overall productivity. Several key elements underscore the importance of this topic in the context of the article.
Summary of Key Points
First, it's vital to acknowledge the core functionalities that small tool tracking software brings to the table. From robust inventory management capabilities to real-time tracking, these features ensure that organizations maintain a clear vision of their resources. This visibility is not just beneficial; it’s essential for enhancing workflow and adapting to dynamic market demands.
Additionally, the benefits of implementing such software cannot be overstated. Companies experience reduced operational costs by minimizing waste and enhancing task efficiency. Moreover, accountability becomes a built-in aspect of daily operations, fostering a culture of responsibility among employees.
On a practical note, organizations must weigh various considerations before making the leap into software selection and deployment. Understanding the scale of operations, integration capabilities, and user-friendliness can significantly influence the successful adoption of tracking solutions.
Lastly, it's worth noting that this software's impact also resonates in future endeavors, with trends toward AI integration and IoT monitoring set to redefine efficiency standards further. Therefore, the importance of integrating small tool tracking software cannot be underscored enough, as it holds the potential to revolutionize how businesses manage their tools and resources.
Future Outlook and Recommendations
Looking ahead, organizations should remain vigilant about the evolving landscape of tool tracking technologies. The future holds exciting possibilities, such as enhanced functionalities powered by AI capabilities, which could automate routine tasks and optimize the decision-making processes.
To gear up for these changes, companies need to prioritize
- Continuous training and upskilling of employees on new systems
- Analyzing data insights for smarter resource allocation
- Staying updated with industry standards and best practices