Free Manufacturing Simulation Software: Ultimate Guide
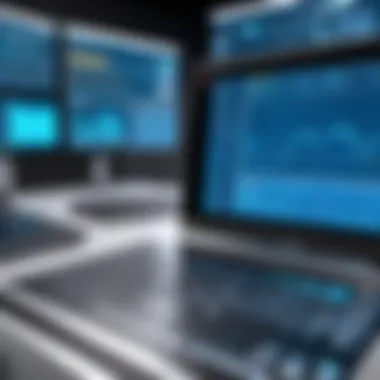

Intro
In the manufacturing industry, efficiency and precision are paramount. The roles of proper planning and execution cannot be understated. Simulation software emerges as a vital tool within this context. This guide focuses on free simulation software available to manufacturing professionals, illustrating its significance in supporting decision-making and optimizing processes. Understanding the available tools is critical. Therefore, this article offers valuable insights into various software solutions, selection criteria, industry applications, and future trends.
Simulation software helps visualize complex processes, allowing manufacturers to test different scenarios without real-world implications. Each tool varies in functionality, addressing specific challenges faced by the industry. This exploration aims to equip users with the knowledge needed to navigate the software landscape effectively. As more companies integrate technology into their operations, recognizing the capabilities of simulation tools can yield significant advantages in productivity and cost management.
Functionality
Overview of Key Features
Free simulation software comes with an array of functionalities that cater to a wide range of manufacturing needs. Common features include:
- Visual modeling: Users can create graphical representations of manufacturing processes.
- Data analysis: These tools often support advanced data analytics to interpret simulations effectively.
- Scenario testing: Manufacturers can create various scenarios to find the most efficient solutions.
- Collaboration tools: Features that allow teams to work together seamlessly increase overall productivity.
How Well the Software Meets User Needs
The efficacy of simulation software largely depends on how well it addresses specific user needs. For many manufacturers, ease of use is a high priority. Thus, software with intuitive interfaces garners more interest. Additionally, customization options can significantly affect the usability of each tool.
Moreover, integrating existing software with simulation tools should be straightforward. This capability allows for smoother workflow transitions. The ability to customize outputs and reports can also enhance the relevance of generated data to specific industries.
Scalability
Adaptability for Growth
Manufacturing is an ever-evolving field. Hence, selecting software that adapts with the business is crucial. Free simulation software often varies in scalability, but the best tools are designed to grow with the company.
Implementing features that cater to both immediate needs and future expansions is key. This adaptability enables manufacturers to incorporate new processes, technologies, and methodologies without overhauling their systems.
Options for Additional Features or Modules
Many simulation tools offer optional features or modules that can be added as businesses grow. For instance, tools like Simul8 and FreeCAD enable additional functionalities through plugins or supported integrations. Users should analyze potential costs and benefits when choosing additional modules. This flexibility ensures that companies can remain competitive by continuously upgrading their simulation capabilities.
"Choosing the right simulation software is not just about immediate functionality but also about future-proofing your manufacturing processes."
In summary, a thoughtful selection of simulation software can foster continuous improvement and operational excellence in manufacturing. Understanding these tools' functionalities and adaptability will lay a solid foundation for informed decision-making.
Understanding Simulation in Manufacturing
The concept of simulation in manufacturing serves as a critical instrument for optimizing processes and enhancing productivity. It allows manufacturers to create accurate models of real-world operations. By doing so, they can predict outcomes, identify bottlenecks, and generate solutions even before physical implementation. Understanding how simulation fits into the manufacturing landscape is vital for people in the industry. With industries increasingly relying on technology, the significance of simulation cannot be overstated. It paves the way for effective decision-making and process transparency.
Definition and Importance
Automation and digitization reshape the manufacturing process. Simulation refers to the process of creating a digital representation of a system, enabling simulations of its behavior under different conditions. Simulation provides a platform for testing various scenarios without the risks associated with physical trials. This ability is especially important in high-stakes environments where the cost of failures can be substantial. In summary, simulation is crucial because it:
- Reduces risks: It allows for testing ideas without real-world consequences, minimizing costly mistakes.
- Increases efficiency: By examining multiple scenarios, manufacturers can fine-tune their processes for optimal performance.
- Facilitates insight: It transforms complex data into understandable outcomes, aiding in better decision-making.
In essence, the role of simulation in manufacturing is to foresee challenges before they emerge and adjust strategies proactively, leading to greater operational efficiency.
Historical Context
The evolution of simulation in manufacturing can be traced back several decades. Early simulation models were primarily mathematical and often involved immense effort from engineers and mathematicians. The 1960s and 1970s marked significant progress, with the advent of computers. Simulation software began to emerge, making it more accessible to many organizations.
As manufacturing processes have become more complex, the tools for simulation have also evolved. The introduction of more sophisticated algorithms and user-friendly interfaces has made simulation software a staple in modern manufacturing. Many companies now view simulation not merely as an auxiliary tool, but as a core component in their strategic arsenal.
Recent years have seen the integration of advanced technologies such as Artificial Intelligence and IoT into simulation tools. The potential for innovation continues to grow. Understanding this historical context is essential. It provides a framework for appreciating how modern simulation software functions and what benefits it can bring to various manufacturing processes.
The Role of Software in Manufacturing Simulation
Manufacturing has evolved significantly with the introduction of advanced technologies. Simulation software plays a pivotal role in this transformation. It allows manufacturers to model, analyze, and optimize processes before actual implementation. This contributes to reduced costs, increased efficiency, and improved product quality. The strategic use of software enables a comprehensive understanding of complex manufacturing systems and helps in making data-driven decisions.
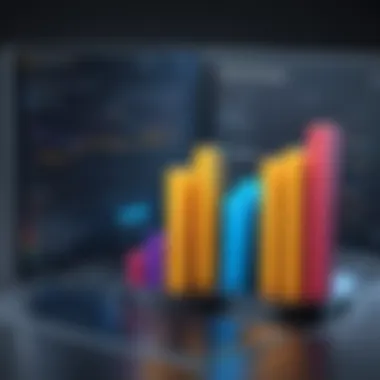

Key Features of Simulation Software
Simulation software generally comes packed with key features designed to streamline operations. Here are some notable elements:
- Visualization: Most software offers strong visualization tools to create realistic representations of manufacturing systems. This helps users better grasp the entire process.
- Scenario Analysis: Users can test different scenarios and conditions without any risk. This allows for extensive evaluation of variables and their impacts on production.
- Data Integration: Good simulation software integrates seamlessly with other systems in the manufacturing environment. This allows for efficient data flow and real-time analysis.
- User-friendly Interfaces: A well-designed interface enhances usability. Even users who may not be tech-savvy can navigate the software comfortably.
- Reporting Tools: The ability to generate detailed reports helps in tracking performance metrics and identifying areas of improvement.
These features enable manufacturers to better predict outcomes and thus optimize their operations effectively.
Types of Manufacturing Simulation Software
Different simulation software exists to meet unique needs within the manufacturing industry. Understanding these types is crucial for selecting the right tool. Here are various kinds:
- Discrete Event Simulation (DES): This type of software models systems as a sequence of events. It's particularly useful in environments where changes occur at distinct intervals, like assembly lines.
- Agent-based Simulation (ABS): In ABS, individual agents represent components in the manufacturing process. Each agent acts according to predefined rules, allowing for a complex simulation of interactions.
- Continuous Simulation: Unlike DES, this approach models systems continuously, making it appropriate for processes like chemical manufacturing where variables change fluidly over time.
- Hybrid Simulation: Combining aspects of different simulation types, hybrid software provides flexibility. It can effectively model complex environments where multiple behaviors coexist.
Understanding the variety of software available helps manufacturers make informed decisions based on their specific operational needs.
Benefits of Using Free Simulation Software
Free simulation software offers significant advantages for manufacturers looking to enhance their productivity and operations. The relevance of this section is especially crucial as we shine a light on two primary benefits: cost efficiency and accessibility for small businesses. Recognizing these elements can help organizations make informed choices that align with their operational objectives.
Cost Efficiency
The foremost benefit of using free simulation software lies in its cost efficiency. Manufacturing operations can be expensive, and reducing overhead is often a priority for many companies. By opting for free software, businesses can minimize software expenditures while still gaining access to valuable simulation tools.
Here are some key points regarding cost efficiency:
- No Licensing Fees: Free software eliminates the need for licensing fees, allowing firms to allocate funds elsewhere.
- Lower Initial Investment: Small and mid-sized enterprises can avoid large upfront costs associated with proprietary software.
- Trial and Error: Users can experiment with various simulations without commitment, enhancing the development process without financial pressure.
Using free simulation software enables manufacturers to test new ideas, assess production lines, and analyze potential outcomes without fiscal anxiety. This flexibility can lead to better strategic decision-making.
Accessibility for Small Businesses
Free simulation software levels the playing fields. Many smaller businesses may not have the capital to invest in expensive software solutions. With free options available, these organizations can access essential tools that were once the privilege of larger manufacturers.
Consider the following aspects of accessibility:
- Resource Availability: Small businesses can utilize quality simulation tools without incurring a substantial economic burden, which promotes innovation.
- User-friendly Options: Many free simulation software solutions often focus on creating an intuitive interface, making them easier for users with limited technical expertise to navigate and employ.
- Community Support: Open-source platforms usually cultivate vibrant communities. Users can seek help, share knowledge, and access tutorials, lowering the barrier for entry even further.
In this way, free simulation software not only provides access to critical tools but also fosters a culture of use and collaborative learning among small manufacturers.
Popular Free Simulation Software for Manufacturing
In the landscape of modern manufacturing, the choice of simulation software can greatly influence operational success. Free simulation software offers enterprises an accessible entry point into advanced modeling and analysis capabilities. This section explores the significance of renowned tools available at no cost, which can transform how businesses approach production challenges. These tools not only enhance modeling precision but also foster innovation without the immediate pressure of hefty financial investments. By incorporating free simulation software, manufacturers can experiment, optimize processes, and ultimately drive efficiency in their operations.
Open-source Software Options
Open-source simulation software is a valuable resource for manufacturers looking to leverage advanced capabilities without incurring costs. These tools typically allow users to freely download, modify, and distribute the software. A few notable examples in this category include:
- FreeCAD: This is a parametric 3D CAD modeler which is often used for product design. With modules for analysis and simulation, it is adaptable to a variety of manufacturing needs.
- Simul8: This platform is tailored for simulating processes in manufacturing, logistics, and service operations. Its user-friendly interface makes it accessible to those who may not have advanced technical skills.
- Open Modelica: Primarily used for modeling complex systems, Open Modelica allows manufacturers to simulate energy management and processes across different domains.
Utilizing these open-source tools not only reduces financial barriers but also enables customization. Users can modify the source code to better fit their own manufacturing realities, which is crucial for addressing unique operational needs and challenges.
Proprietary Free Versions
While many simulation programs come with price tags, several companies offer free versions of their software with limited features. These proprietary versions can serve as a valuable starting point for manufacturers wishing to explore simulation capabilities without full investment.
- Fusion 360 by Autodesk: Although it is premium software, Autodesk offers a free version for students and startups. It integrates CAD and simulation technology that aids in product design and testing.
- SolidWorks: SolidWorks provides a free student edition under certain conditions, allowing learners and small companies to engage in CAD applications alongside simulation options.
- BIM 360: While primarily focused on building information modeling, this software can help manufacturers simulate construction processes and workflows, offering a free trial period.
These proprietary free versions are generally equipped with robust features to enable efficient product development. As manufacturers become proficient with basic functionality, they can consider upgrading for more extensive capabilities as their requirements evolve.
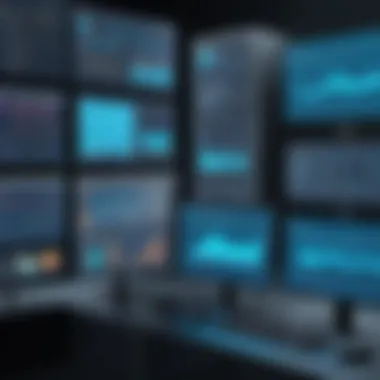

Important Note: It is crucial to understand the limitations of free versions. Often, the most advanced features are reserved for paid plans, which can influence decision-making in upgrading or transitioning to paid software.
Key Considerations When Choosing Software
When selecting simulation software for manufacturing, several key aspects need to be evaluated. These considerations can significantly impact how effectively the software integrates into existing workflows and contributes to overall operational efficiency. It is crucial to go beyond mere functionality to ensure that the software aligns well with business needs and objectives. Here, the three primary considerations include compatibility with existing systems, user experience and interface, and customer support and community.
Compatibility with Existing Systems
Compatibility is vital when assessing software choices. It ensures that the new simulation software can effectively work with any current systems in place. For instance, if a company uses particular manufacturing execution systems (MES) or enterprise resource planning (ERP) software, the new simulation tool must integrate smoothly to avoid data silos or operational bottlenecks.
Incompatibility can lead to unnecessary complexity and increased costs as businesses may need to redo processes to accommodate the new software. Therefore, it is beneficial to review technical specifications and seek solutions that offer APIs or flexible integration options. Testing compatibility in a controlled environment can often reveal more about how well the software will function alongside existing tools.
"Software is most effective when it seamlessly integrates into the broader technological ecosystem."
User Experience and Interface
User experience (UX) plays a significant role in the successful adoption of any software. A software product with a complex user interface can lead to steep learning curves, slowing down the implementation process and disappointing users. A clear, logical interface that encourages ease of use enhances productivity.
When assessing user experience, consider factors such as navigation, customization options, and the overall design aesthetic. Good UX can enable users to focus on simulations without being distracted by cumbersome design elements. Itβs advisable to explore demo versions of the software when possible, assessing not only how intuitive the interface is but also how long it takes for users to become proficient.
Customer Support and Community
Customer support can often distinguish between a frustrating and a productive software experience. Reliable technical support ensures that if issues arise during usage, help is readily available. This can range from email support to live chat or phone assistance.
Community engagement is another aspect worth exploring; active online forums or user groups can provide shared experiences, tips, and troubleshooting advice. Companies that foster a robust user community might offer resources beyond what formal documentation can provide. Searching for user reviews and feedback on platforms like Reddit can yield valuable insights into the support culture surrounding specific software tools, influencing the decision-making process.
In summary, when choosing simulation software for manufacturing, evaluating compatibility, user experience, and customer support is essential. Investing time to analyze these factors can lead to significant long-term benefits, optimizing both the software's functionality and the overall manufacturing process.
Integration of Simulation Software in Manufacturing Processes
In the ever-evolving landscape of manufacturing, the integration of simulation software becomes an essential practice. This integration is not merely about adopting a new tool; it encompasses a holistic approach to enhancing productivity and operational efficiency. Simulation software allows manufacturers to visualize processes, predict outcomes, and assess various scenarios without the need for costly physical prototypes. This section explores how integrating simulation software can lead to streamlined operations and enhanced decision-making within the manufacturing sector.
Streamlining Operations
Simulation software streamlines operations by providing a digital twin of manufacturing processes. A digital twin is a virtual representation that mirrors real-world systems in real-time. With this, manufacturers can identify bottlenecks, inefficiencies, and redundancies early in the production cycle. This visualization allows teams to modify operations before physical implementation.
- Reduced Lead Times: By using simulation models, manufacturers can optimize workflow and decrease lead times drastically. When teams can simulate the layout of a factory floor, for example, they can find the most efficient flow of materials, reducing the time products spend in manufacturing.
- Resource Optimization: Simulation tools help determine the optimal allocation of resources including labor, machinery, and material. This leads to enhanced productivity and less waste. When resources are utilized effectively, costs are managed better, resulting in improved profitability.
- Continuous Improvement: With the ability to experiment virtually, manufacturers can continuously improve processes. They can test various approaches to understand their impact on production metrics, facilitating a culture of innovation that is data-driven.
"Simulation software is not just a tool; it's a catalyst for change in production processes."
Enhancing Decision-making
Enhanced decision-making is a crucial benefit that comes from integrating simulation software into manufacturing. Data-driven decisions are more effective, and simulation provides the critical insights necessary for those choices.
- Scenario Analysis: Simulation allows manufacturers to analyze various scenarios and predict outcomes based on different inputs. This is especially valuable in a market that may be subjected to unpredictable demand shifts. By evaluating potential scenarios, decision-makers can prepare more robust strategies.
- Risk Management: Every manufacturing process carries risk. Simulation helps in risk assessment by predicting potential points of failure or inefficiencies. By understanding these risks in advance, manufacturers can implement measures to mitigate them, thereby safeguarding their operations.
- Informed Strategic Planning: With insights gained from simulation tools, leaders can make informed decisions regarding investments, resource allocation, and process re-engineering. This strategic foresight can provide a competitive advantage in the fast-paced manufacturing landscape.
Challenges Associated with Free Simulation Software
Navigating the realm of free simulation software comes with its own set of challenges. While the idea of accessing sophisticated tools without financial commitment is appealing, a critical evaluation of their limitations is essential. Understanding these challenges not only prepares users for potential obstacles but also helps them make informed decisions in their software selection process. This section focuses on two significant challenges: limited features compared to paid options and security concerns affecting data privacy.
Limited Features Compared to Paid Options
Free simulation software often lacks critical features found in their paid counterparts. These limitations can include advanced modeling capabilities, customization options, and integration with other enterprise tools. For example, powerful features like real-time data analytics, support for complex algorithms, or extensive API access are usually absent in free solutions.
In many cases, manufacturers implementing simulation software for the first time may find themselves hindered by these constraints. The inability to utilize a softwareβs full potential can lead to suboptimal performance and inaccurate simulations. Users may experience frustration as they attempt to complete tasks that would be straightforward on more robust software.
Additionally, the user interface of free software might not be as intuitive as that of paid options. This can slow down the learning curve, requiring more time for teams to adapt and get the most out of the available tools. A lack of training resources or community support can further complicate usage, leaving users feeling isolated in their challenges.
"The gap between what users expect and what free software provides can be significant, often leading to dissatisfaction and inefficiency."
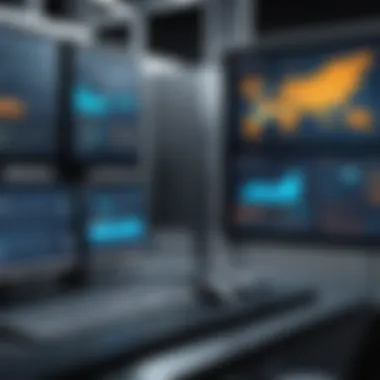

Security and Data Privacy Concerns
Security is another paramount challenge associated with free simulation software. When free tools are used, questions frequently arise regarding data privacy. Users must consider whether the software provider has clear policies in place to protect sensitive manufacturing data.
Many free tools may not implement rigorous security measures such as data encryption or multi-factor authentication, which can expose businesses to cyber threats. Data breaches can lead to significant losses, both financially and reputationally, which outweigh any savings made by choosing a free option.
Moreover, the nature of open-source software often leaves users unsure about the security track record of the software. While many open-source solutions allow for transparency and peer review, the lack of dedicated support can result in vulnerabilities that may not be promptly addressed. Users also need to be cautious of where their data is stored and how it is shared with third parties.
Case Studies: Success Stories in Manufacturing
Case studies serve as vital evidence of how free simulation software can improve manufacturing processes. They are not only illustrative but also informative. By examining real-world applications, businesses can gauge the effectiveness and practical use of different software.
Each case sheds light on unique challenges faced by manufacturers and the innovative ways they overcame these hurdles through free simulation tools. Companies, regardless of their size, can draw parallels with their situations and adapt successful strategies to their own needs.
Small Business Implementations
Small businesses often operate under tight budgets, making the cost-effectiveness of free simulation software particularly appealing. A noteworthy example is a local furniture manufacturer that adopted OpenSim. The firm faced challenges in optimizing their production line. By using the software, they were able to simulate different layouts and processes without incurring substantial costs.
The benefits were evident. The manufacturer discovered a more efficient workflow that reduced material waste and improved labor productivity. Additionally, they could conduct what-if analyses, allowing them to test changes in real-time and assess potential outcomes before implementation. Such strategic tools provided the small business with significant insights that would have otherwise been inaccessible.
Larger Enterprises Utilizing Free Software
Larger enterprises, while often equipped with considerable resources, can still benefit from free simulation software. Consider a global automotive manufacturer that explored AnyLogic for supply chain simulations. The objective was to improve the alignment of suppliers and reduce lead times.
Using AnyLogic's capabilities, the enterprise was able to visualize complex logistics scenarios. They analyzed real-time data to refine their predictive models. The result was a marked improvement in their operational efficiency and cost savings which could be redirected to innovation and product development.
These examples underscore how both small and large organizations can leverage free simulation software, achieving impressive results. Such case studies are crucial as they provide empirical evidence that can guide others in similar industries.
Future Trends in Simulation Software
In the rapidly evolving field of manufacturing, simulation software plays a vital role in optimizing processes and enhancing production capabilities. Understanding the future trends in simulation software is crucial for businesses aiming to stay competitive. Advancements in technology, particularly in areas like artificial intelligence and Internet of Things, are reshaping how simulation software is developed and used. These changes present numerous benefits, such as improved efficiency, better decision-making, and enhanced interoperability between machines and systems.
Advancements in Artificial Intelligence
Artificial intelligence (AI) is influencing many sectors, and manufacturing is no exception. Simulation software is beginning to incorporate AI algorithms that allow for smarter predictions and analysis. These capabilities can help in minimizing downtime, reducing waste, and improving overall production quality. For instance, AI-driven tools can analyze vast amounts of data generated during manufacturing processes, identifying patterns that human operators might overlook.
- Predictive Maintenance: AI can forecast equipment failures before they happen, allowing for timely maintenance that minimizes costly downtime.
- Optimization Algorithms: Advanced algorithms can suggest optimal production schedules and resource allocations based on real-time data.
- Enhanced Design Capabilities: AI can assist in creating more efficient product designs by analyzing previous models and suggesting improvements.
These advancements not only streamline operations but also lead to more sustainable manufacturing practices, ensuring companies can adapt to market changes effectively and efficiently.
Integration with Internet of Things
The Internet of Things (IoT) is another key factor influencing simulation software in manufacturing. As more devices become interconnected, real-time data exchange between machines and software platforms becomes feasible. This connectivity allows for dynamic simulation models that can adapt to real-time conditions. The benefits of integrating IoT with simulation software are numerous.
- Improved Data Accuracy: With IoT sensors collecting real-time data, simulation models can reflect the current state of the manufacturing environment more accurately.
- Faster Decision-making: Instant access to live data allows for quicker evaluations and adjustments within the manufacturing process.
- Holistic Operational Views: Integration offers a comprehensive view of operations, making it easier to identify inefficiencies and opportunities for optimization.
Finale and Final Thoughts
In this guide, we have examined the essential landscape of free simulation software in the manufacturing sector. Understanding the available tools can significantly enhance the operational efficiency and decision-making processes within manufacturing environments. As highlighted, simulation software serves not only as a tool for analysis but also as a strategic asset that enables businesses to visualize processes, forecast outcomes, and identify potential improvements.
The benefits of employing free simulation software are numerous. Organizations can reduce costs while gaining access to powerful analytical tools. Furthermore, this accessibility encourages small businesses to integrate sophisticated technologies that were once only feasible for larger corporations. Such democratization of technology ensures that innovation and efficiencies are not limited by size or budget.
However, potential users must consider several factors when opting for free software. The trade-offs often include limited features compared to paid alternatives, which might impact advanced users. Security and data privacy are other critical considerations, as many free software options may not provide the robust protections offered by commercial products. It is vital for organizations to weigh these factors against their unique needs and aspirations.
Ultimately, the exploration of free simulation software is more than just a cost-saving measure; it is an investment in future capabilities and efficiencies for manufacturing. As businesses adapt to a rapidly changing technological landscape, embracing these tools will be crucial to maintaining competitiveness and fostering continuous improvement.
Recap of Key Points
To summarize the critical takeaways from this article, consider the following:
- Simulation software enhances operational efficiency by enabling better planning and resource allocation.
- Free software democratizes access to advanced tools, especially benefitting small to medium-sized enterprises.
- Feature limitations may exist, requiring firms to assess their actual needs carefully.
- Security remains a pivotal issue with free software, necessitating due diligence in selection.
Encouragement for Exploration
As the manufacturing landscape continues to evolve, so too does the role of simulation software. Professionals in the field should take the initiative to explore the many free options available today.
Investigating variety in tools not only provides insights into specific capabilities but also offers experiences that enrich understanding of processes and workflows. Consider engaging with online communities, such as those found on Reddit or Facebook, to share experiences and gain feedback about different software solutions. Participating in this dialogue promotes collaborative learning, fostering a more profound grasp of how these tools can be effectively utilized in real-world applications.