Exploring Maintenance Work Order Apps: A Comprehensive Guide
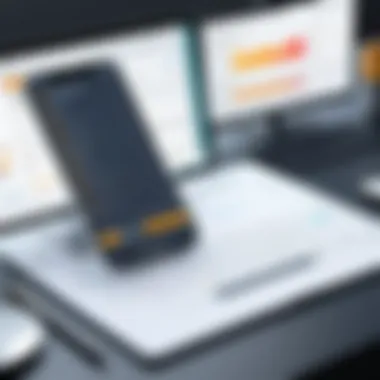
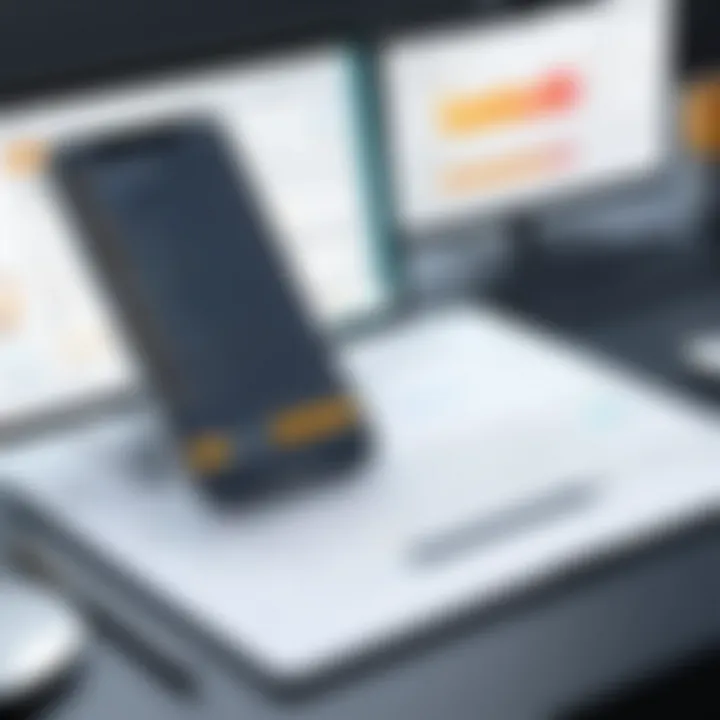
Intro
In today's fast-paced business environment, managing maintenance tasks efficiently is crucial. Maintenance work order apps play a significant role in this context, by automating processes and enhancing productivity. This guide will navigate through the essential aspects of maintenance work order applications, including their functionality, scalability, and more. We aim to provide valuable insights that help businesses select the most suitable solutions for their operational needs.
Functionality
The functionality of maintenance work order apps is a cornerstone of their effectiveness. These applications generally offer a suite of features that help businesses streamline their maintenance operations. Understanding these functions can help in evaluating different options in the market.
Overview of key features
Most maintenance work order apps include a variety of features:
- Task management: Users can assign and track tasks efficiently.
- Scheduling: Automated reminders and calendars help prevent missed deadlines.
- Asset tracking: Monitor the condition and location of equipment.
- Reporting: Generate detailed reports on maintenance activities for analysis.
- User access control: Manage who can view and edit information within the app.
These features contribute to better organization and time management across teams.
How well the software meets user needs
The effectiveness of maintenance work order apps largely depends on how well they cater to the user's requirements. A good app is user-friendly and integrates seamlessly with existing workflows. Businesses must consider the specific needs of their operations. Observing user feedback and reviews provides insights into real-world applications, which can influence decision-making.
Scalability
Scalability is a crucial aspect of any software solution. A maintenance work order app must not only meet current demands, but also adapt as the organization grows.
Adaptability for growth
Apps that allow for easy adaptation are essential for sustainability. A scalable app can accommodate an increasing number of users and additional maintenance processes. Companies should assess how easily an app can be expanded. This could involve adding new sites, teams, or functionalities.
Options for additional features or modules
To ensure long-term viability, businesses must also evaluate the potential for incorporating new features. Many programs offer modular systems that allow for the integration of extra functionalities as business needs evolve. Certain applications may feature:
- Integration with IoT devices
- Advanced analytics tools
- Mobile access for field technicians
This flexibility ensures that a maintenance work order app can grow in tandem with the business it serves.
"Choosing the right maintenance work order app not only improves efficiency but also prepares the business for future challenges."
Prelims to Maintenance Work Order Apps
Maintenance work order apps are crucial tools in modern business settings. They enable organizations to systematically manage maintenance tasks, enhance efficiency, and reduce costs associated with maintenance operations. In today’s fast-paced environment, the importance of these apps cannot be overstated. Companies of various sizes and industriesare increasingly relying on technology to streamline their maintenance processes.
Definition and Purpose
Maintenance work order apps are software solutions that help manage maintenance tasks by organizing, tracking, and reporting on work orders. The primary purpose of these applications is to improve the management of maintenance requests and ensure that tasks are completed in a timely manner. These apps allow businesses to create and assign work orders, schedule maintenance activities, and monitor progress.
One of the key elements of these apps is their ability to provide clarity in communication among maintenance teams and other stakeholders. They serve as a centralized platform where all relevant information about maintenance tasks can be accessed easily. Additionally, maintenance work order apps can lead to improved asset management, ensuring that machinery and equipment are maintained properly to avoid downtime.
Evolution of Maintenance Management Software
The evolution of maintenance management software is closely linked to advancements in technology. Traditionally, maintenance management relied on paper-based systems or fragmented digital tools that often hindered efficiency. Companies faced challenges in tracking work orders, managing resources, and communicating effectively between teams.
With the emergence of cloud computing and mobile technologies, maintenance management software has transformed considerably. The shift towards integrated solutions has made it easier for organizations to deploy maintenance work order apps. These modern systems often incorporate features such as real-time tracking, automated notifications, and analytics capabilities that support decision-making.
Today's maintenance work order applications have repurposed the old paradigms of managing maintenance work. They provide businesses with the tools required to optimize their operations, reduce unplanned downtime, and maintain regulatory compliance. As maintenance management continues to evolve, these apps are becoming increasingly sophisticated, incorporating cutting-edge technologies such as the Internet of Things (IoT) and artificial intelligence.
Key Features of Maintenance Work Order Apps
Maintenance work order apps are designed to optimize the process of managing maintenance tasks. The importance of understanding their key features lies not only in enhancing operational efficiency but also in facilitating better communication among team members. These apps provide specific functionalities that stand out and are crucial for businesses seeking effective maintenance solutions. In this section, we will explore four essential features that define the effectiveness of maintenance work order apps.
User-Friendly Interface
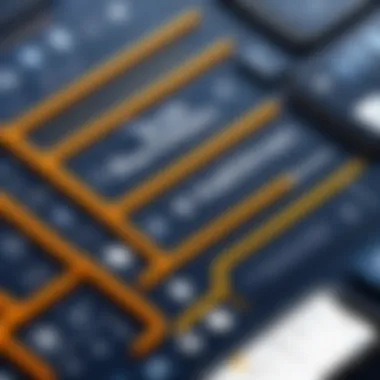
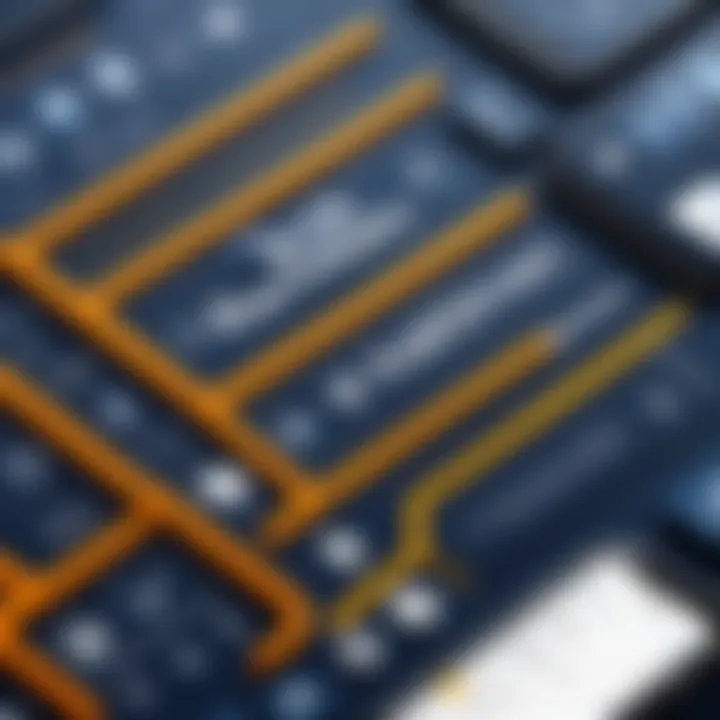
A user-friendly interface is essential for any software, but it holds particular significance for maintenance work order apps. These applications are often used by staff who may not be tech-savvy. Therefore, the design should be intuitive, allowing users to navigate seamlessly through different functions without extensive training. A good interface minimizes clicks needed to complete tasks. For example, if a technician can quickly log a work order, it increases the likelihood that they will accurately document all relevant details.
In addition, mobile accessibility allows users to interact with the app on-the-go, crucial for field workers who may not always be at their desks. By streamlining the interface, companies can improve adoption rates among employees, leading to more efficient workflow and reduced errors.
Real-Time Tracking
Real-time tracking is a pivotal feature that enables businesses to monitor work orders’ statuses instantly. This feature allows for more precise planning and resource allocation. When managers can see live updates on ongoing tasks, they can make informed decisions quickly. For instance, if a repair starts to take longer than anticipated, managers can reallocate resources to ensure that other tasks are not delayed.
Moreover, real-time tracking enhances accountability. Technicians and workers must update their progress, thus reducing the lag time in workflow visibility. This aspect also contributes to better customer service, as stakeholders can receive timely updates on work order statuses. Being aware of where issues stand can significantly improve response times.
Automated Notifications and Reminders
Automated notifications and reminders play a critical role in effective maintenance management. These alerts can inform team members about upcoming tasks or changes to active work orders. For example, if a routine maintenance task is approaching due date, the assigned technician will receive a notification. This feature helps to ensure that no task is overlooked, reducing the chances of neglecting critical maintenance activities.
Additionally, reminders can be customized based on urgency. For instance, tasks labeled as high priority can trigger immediate alerts compared to less urgent items. This customization enhances operational efficiency and ensures better compliance with maintenance schedules. Moreover, looking forward, customers can also receive alerts regarding service appointments or updates, augmenting overall customer satisfaction.
Historical Data Analysis
Historical data analysis offers valuable insights that can inform future maintenance practices. By analyzing past maintenance work orders, organizations can identify patterns in equipment failure, service deficiencies, and overall resource usage. This intelligence plays an essential role in budgeting and forecasting.
For example, understanding how often a particular machine requires maintenance can lead to more accurate inventory and staffing needs. Furthermore, leveraging this data for predictive maintenance allows companies to perform maintenance tasks just before issues arise, thus avoiding costly downtime.
Through systematic historical data analysis, maintenance teams can engage in informed decision-making that shapes their operational strategies. This not only enhances efficiency but also contributes to long-term cost savings.
Investing in maintaining a well-designed maintenance work order app with these key features will undoubtedly lead to improved productivity, reduced operational costs, and better customer satisfaction.
Benefits of Implementing Work Order Apps
Implementing a work order app can profoundly impact a business's maintenance processes. The advancement from traditional methods to digital solutions transforms not only the way tasks are managed but also enhances overall productivity. This section will explore key benefits of work order apps, which can help organizations streamline their operations and achieve their long-term objectives.
Increased Operational Efficiency
Operational efficiency is a primary driver for adopting work order apps. These applications automate and standardize routine tasks, significantly reducing the time spent on administrative duties. For instance, scheduling maintenance activities becomes a streamlined process. Instead of manually assigning tasks, the app can allocate resources based on availability automatically. This ensures that work orders are handled promptly and efficiently.
Moreover, work order apps offer real-time updates about ongoing tasks. This immediate access to information allows managers to make informed decisions quickly. As a result, the organization can respond more effectively to issues as they arise, minimizing downtime and maximizing productivity. The implementation of work order apps ultimately enables businesses to focus on core activities instead of being bogged down by administrative burdens.
Enhanced Communication
Communication is crucial in any organization, particularly in maintenance operations. Work order apps facilitate enhanced communication among team members. Stakeholders can share updates, feedback, and critical information instantly, whether in the field or at the office. This collaborative platform ensures that everyone involved is on the same page.
Furthermore, the apps often include features for reporting problems, requesting services, and updating work statuses. This eliminates the reliance on emails or informal messaging, reducing misunderstandings and improving accountability. Well-informed teams contribute to smoother operations. Thus, enhanced communication leads to a more cohesive working environment that fosters better results for the organization.
Cost Management and Savings
Cost management is a challenge for many organizations, but work order apps provide a solution. These applications help identify and track expenses associated with maintenance tasks. By analyzing this data, companies can find areas to cut costs and enhance spending efficiency. The detailed reports generated by these apps can show spending trends and high-cost areas needing attention.
Additionally, work order apps minimize waste through better resource management. For example, employees can preemptively identify and address equipment issues, reducing costly emergency repairs and downtime. The cumulative effect of these savings translates into a healthier bottom line or even allows for reinvestment in other areas of the business.
Compliance and Safety Management
Compliance and safety are critical in maintenance management. Regulations concerning safety standards vary by industry, and keeping track of them is essential for avoiding fines or legal issues. Work order apps can automate the documentation process, storing essential compliance information readily accessible.
By utilizing these apps, companies can set reminders for routine inspections and safety checks. This proactive approach ensures that safety protocols are always met, leading to a safer working environment for employees. Furthermore, a documented history of compliance efforts can be invaluable in showcasing the company's commitment to safety during audits or inspections.
Implementing a work order app not only streamlines the operational aspects of maintenance but also contributes significantly to enhancing communication, managing costs, and ensuring compliance. As these features become increasingly important in today's fast-paced business environment, embracing this technology is now a necessity rather than a luxury for forward-thinking organizations.
Popular Maintenance Work Order Apps in the Market
The market for maintenance work order apps has grown significantly in recent years. These applications are essential tools that streamline maintenance processes across various sectors, such as manufacturing, facility management, and property management. They provide users with improved organization, better communication, and increased productivity. Understanding the available options can significantly impact how effectively a business manages its maintenance tasks.
Overview of Key Players
Some of the notable maintenance work order apps that have established a strong presence in the market include:
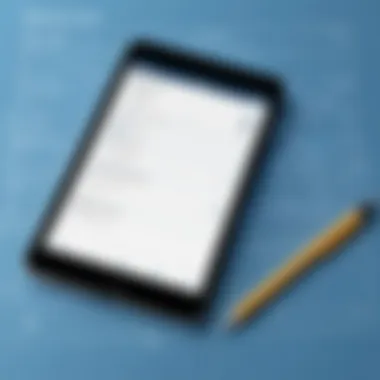
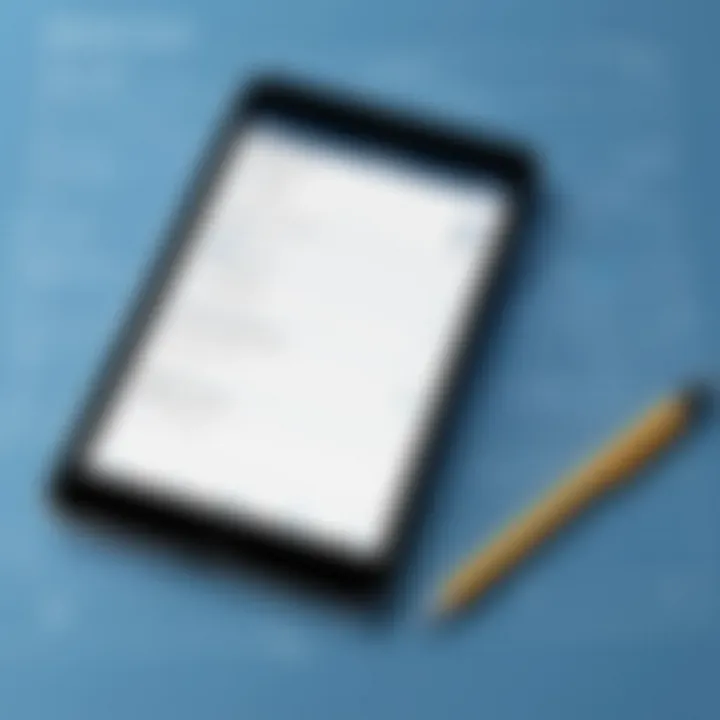
- FMX: This cloud-based software is user-friendly and integrates work order management with scheduling and asset management features. It is particularly favored by facilities and property managers.
- Maintenance Care: This app is designed for both small and large organizations. It offers customizable features, making it adaptable to various industry needs.
- Hippo: Known for its simplicity, Hippo provides essential work order management tools and focuses on reducing maintenance costs through better tracking of resources.
- UpKeep: This mobile-first maintenance app focuses on real-time communication and reporting, which is critical for businesses looking to improve their response times and overall efficiency.
By examining these and other key players, businesses can determine which app aligns best with their operational requirements.
Comparative Analysis of Features
When choosing a maintenance work order app, it is vital to assess the features that stand out among different solutions. Here are some comparisons to consider:
- Usability: The interface of FMX is praised for its intuitive design, making it an excellent choice for non-technical users. In contrast, Maintenance Care offers extensive customization that may require a steep learning curve.
- Integration Capabilities: UpKeep excels at integrating with other tools, such as accounting software. This feature can streamline workflows and enhance efficiency across departments.
- Mobile Access: Hippo and UpKeep have robust mobile applications that give field staff the ability to create, manage, and track work orders on the go, promoting flexibility and real-time updates.
- Reporting and Analytics: Maintenance Care provides in-depth reporting options that help managers analyze performance metrics over time. This feature can assist in strategic planning.
Evaluating these attributes helps organizations make informed decisions when selecting a work order app to fit their specific settings and expectations.
"The right maintenance work order app can significantly improve not just how maintenance tasks are handled, but also the overall operational efficiency of a business."
Choosing the correct solution from the popular options available will lead to smoother maintenance operations and help organizations meet their goals effectively.
Choosing the Right Work Order App
Selecting an appropriate work order app is pivotal in optimizing maintenance operations. Businesses must align the software features with their operational needs and future objectives. The right application can rectify inefficiencies, streamline workflows, and promote better communication among teams. When assessing potential applications, several critical factors must be taken into account.
Assessing Your Business Needs
Understanding your business requirements is the first step in choosing a work order app. Each organization has unique operations, which dictate specific needs. For instance, a manufacturing facility may require detailed machinery tracking, while a service provider might prioritize customer service integration.
- Identify Core Features: List the necessary features based on your operations. Consider functionalities like job scheduling, asset management, and reporting capabilities.
- Evaluate Current Processes: Reassess existing processes to pinpoint pain points that need addressing. Interview stakeholders to gather insights into their needs.
- Anticipate Future Growth: Consider your business goals and how the app can scale with them. Flexibility and scalability in a software solution can save resources in the long run.
Customization Options
Customization is another essential aspect of selecting a maintenance work order app. Low adaptability can lead to user frustration and hinder the application's effectiveness.
- Tailored Interfaces: Look for applications that allow customization of user interfaces. This lets users access the most relevant information quickly.
- Adjustable Workflows: Ensure that the app can adapt types of workflows to match your business processes. A rigid system will result in inefficiency.
- Integration Capabilities: Check if the app integrates with existing software like ERP systems or inventory management tools. Seamless integration can enhance operational flow.
Budget Considerations
Finally, budget plays a crucial role in choosing a work order app. It's important to balance the cost with the application’s value.
- Initial Costs vs. Long-Term Savings: Consider not just the upfront costs, but also the value generated over time. A slightly higher investment could yield faster ROI through increased efficiency.
- Evaluate Pricing Models: Review different pricing structures. Some apps may offer monthly subscriptions, while others may utilize a one-time fee. Choose one that aligns with your financial strategy.
- Hidden Costs: Be aware of potential hidden costs, such as those for training, customer support, and system updates. These can add up and affect the total budget.
Choosing the right work order app is about more than just picking an option. It involves understanding your needs, customization capabilities, and financial implications in relation to your operational goals.
By taking these factors into account, businesses can make an informed choice that supports their maintenance objectives effectively.
Implementation Strategies for Work Order Apps
Implementing a maintenance work order app requires a strategic approach. Organizations must ensure alignment between their operational goals and the capabilities of the software. Proper implementation shapes the user experience and determines the app's overall effectiveness. For businesses aiming to optimize their maintenance operations, an effective rollout is essential. The following sections will discuss key strategies to facilitate this implementation.
Planning the Rollout
A well-thought-out rollout plan serves as the foundation for successful adoption. First, it is important to define the objectives of the work order app. This includes identifying specific problems the app intends to address, such as reducing response time to maintenance requests or improving resource allocation. Engaging with stakeholders during this phase is beneficial. Their input can guide necessity and expectations, ultimately influencing the software selection decision.
Additionally, choosing a phase-based rollout versus a full deployment should be considered. A phased approach allows for gradual adaptation and testing, minimizing disruption in existing workflows.
- Assess infrastructure readiness: Before rollout, examine the current IT environment. Ensure compatibility with existing systems and platforms.
- System integration: Plan how the app integrates with other tools. Effective integration can enhance data flow and improve analysis capabilities.
User Training and Adaptation
Training users is integral to ensuring that the maintenance work order app is utilized effectively. An unclear gap in knowledge can lead to resistance, making it crucial to implement a comprehensive training program. The training approach can vary based on the user group’s familiarity with technology. For instance, the training for a field technician may focus more on practical application, while managerial staff might benefit from a more analytical perspective.
Training strategies might include:
- Hands-on workshops: Interactive sessions where users can practice in a controlled environment.
- Online tutorials: Asynchronous learning option to allow users to familiarize themselves at their own pace.
- Continual support: Establish a support structure post-training that assists users with questions or problems. This can help to improve confidence and increase acceptance of the new system.
"The key to successful adoption is ensuring users feel competent and supported in using the new app. It’s not just about providing the software; it is about enabling users to leverage it effectively."
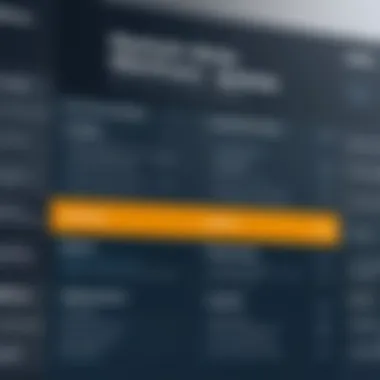
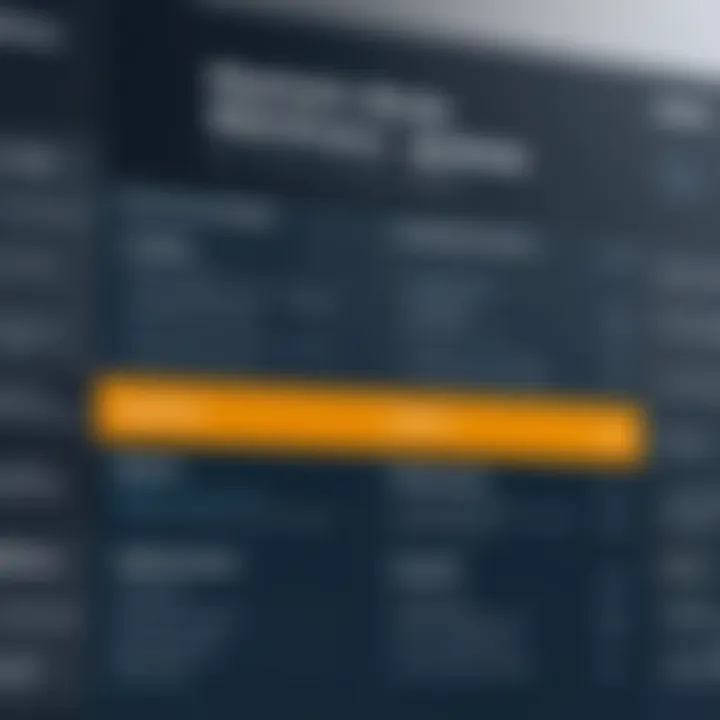
In summary, strategic implementation efforts directly affect how well a maintenance work order app performs in meeting its intended objectives. Careful planning and thorough training can drive smoother transitions and enhance operational efficiency.
Challenges in Adopting Maintenance Work Order Apps
Adopting maintenance work order applications is not without its hurdles. While the benefits are substantial, understanding the challenges is crucial for businesses. These challenges can significantly determine the success of the implementation process. Identifying specific barriers can help organizations devise strategies to overcome them. By addressing these obstacles early, companies can smoothen the transition to using these technologies.
Resistance to Change
One of the most significant barriers to the adoption of maintenance work order apps is resistance to change. Employees and management alike may feel uncomfortable with new systems or processes. This resistance can stem from several factors. Most notably, employees may fear the unknown; they might be used to traditional methods, such as pen-and-paper or basic spreadsheets.
Moreover, there might be concerns about how changes will affect job roles and responsibilities. Certain staff may worry that automation will lead to job losses or a reduction in their importance. To overcome this, clear communication is essential. It is important to convey the benefits of the new system not just for the organization but also for the employees involved. Here are some points to consider:
- Involve Employees in the Decision-Making: Gathering feedback from users ensures they feel included and valued. This participation can help mitigate fears.
- Highlight the Advantages: Emphasizing how the app can reduce workloads and improve efficiency can foster acceptance. This might include improved tracking of work and easier access to critical information.
- Provide Training: Comprehensive training sessions can ease fears about using the new technology. Familiarizing staff with the app may lessen resistance and enhance productivity.
"The key to adoption is not just the technology itself but also how well employees embrace it."
Data Migration Issues
Another challenge in adopting maintenance work order apps is data migration. Transitioning existing data into a new system can be tedious and fraught with complications. If current records are stored in various formats or systems, consolidating this information becomes complex. Data accuracy is crucial to ensure that the app functions as intended. Poor migration practices can lead to missing, corrupt, or inaccurate data.
To mitigate these issues, several steps should be taken:
- Conduct a Data Audit: Businesses should assess their current data before migration. Understanding what data is relevant and necessary helps in deciding what to transfer.
- Plan for Data Cleaning: Cleaning up old records and correcting inaccuracies can simplify the migration process. This step ensures that only high-quality data is transferred.
- Test the Migration: A trial run of the migration process allows for identifying potential issues before the full transfer. Adjustments can be made based on the findings from the test.
The successful adoption of maintenance work order applications hinges on addressing these challenges. By recognizing resistance to change and data migration issues, organizations can better prepare for a smooth transition to improved processes.
Future Trends in Maintenance Work Order Applications
The landscape of maintenance work order applications is evolving. Understanding future trends is crucial, as they impact how businesses manage their maintenance operations. As technology advances, the integration of new features becomes essential for competitiveness and operational efficiency. Businesses must adapt to these changes to optimize their resources and improve their service delivery.
Integration with IoT Devices
The integration of Internet of Things (IoT) devices stands at the forefront of future trends in maintenance work order applications. IoT devices offer real-time data collection capabilities. Sensors can monitor equipment health, track usage, and report anomalies before they escalate into major issues. This proactive approach reduces downtime and maintenance costs.
For example, imagine a facility using IoT devices on HVAC systems. If the temperature exceeds a certain threshold, an automatic work order is generated. Technicians receive notifications to address the issue immediately, which minimizes comfort disruption.
Benefits include:
- Enhanced Data Collection: Improved insights lead to data-driven decisions.
- Predictive Maintenance: Anticipating issues prevents extensive damage.
- Efficiency Boost: Automation streamlines workflow operations.
Artificial Intelligence and Predictive Maintenance
Artificial Intelligence (AI) plays a pivotal role in predictive maintenance within work order applications. By analyzing historical data, AI algorithms can predict potential failures. This allows businesses to schedule maintenance at optimal times, avoiding unexpected breakdowns.
Predictive maintenance improves operational resilience. It reduces costs associated with emergency repairs and prolongs equipment lifespan. AI's ability to process large data sets enables more accurate forecasting. This way, companies can allocate resources effectively.
Key advantages are:
- Reduced Downtime: Predictive analytics helps avoid unexpected machine failures.
- Cost Efficiency: Planned maintenance is often less expensive than reactive measures.
- Resource Optimization: Better insights lead to improved labor and material use.
Investing in technologies like AI and IoT positions businesses for the future of maintenance management.
The End
In this comprehensive guide, the importance of embracing maintenance work order apps has been illustrated extensively. These applications play a pivotal role in modern maintenance management, facilitating smoother operations and fostering productivity. The topic of this conclusion serves to reiterate significant insights outlined throughout the article, underscoring how these tools can transform operational workflows.
Recap of Key Points
- Definition and Purpose: Maintenance work order apps are essential for streamlining maintenance tasks, ensuring that operations run efficiently and effectively.
- Key Features: User-friendly interfaces, real-time tracking, automated notifications, and historical data analysis are some features that enhance functionality.
- Benefits: Implementing these apps leads to higher operational efficiency, improved communication, better cost management, and enhanced compliance.
- Popular Applications: Various notable apps have been reviewed, each offering unique features tailored to diverse business needs.
- Implementation Strategies: Careful planning and user training are critical for seamless integration into existing workflows.
- Challenges: Organizations face challenges such as resistance to change and data migration issues that can affect the adoption of these tools.
- Future Trends: The integration of IoT devices and the application of artificial intelligence are setting the stage for innovative maintenance practices.
Final Considerations for Implementation
When considering the implementation of maintenance work order apps, businesses must focus on several key aspects:
- Assessment of Needs: Clearly define the specific needs of your organization. What tasks require streamlining?
- Customization: Opt for solutions that offer customization to align with your company’s objectives.
- Training and Adaptation: Ensure that employees receive adequate training to maximize the use of the app. Foster a culture of adaptability to embrace the technological shift.
- Budget Management: Evaluate the costs versus the benefits these applications will bring. Choosing the right tool should align with the overall budgetary constraints of the business.
Adopting a maintenance work order app can lead to remarkable changes in your operational workflow, so approaching implementation thoughtfully is essential.
In summary, as businesses evolve, so must their operational toolset. Harnessing the potential of maintenance work order apps is not just an option; it is becoming a necessity in a technology-driven environment.