Mastering ANSYS 3D Modeling for Industry Applications
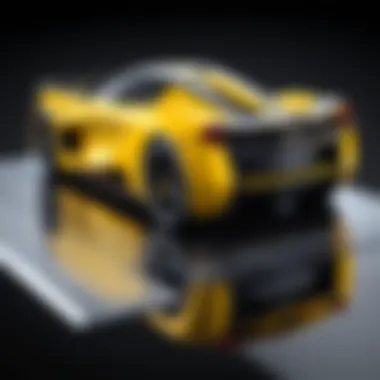

Intro
ANSYS 3D modeling is a pivotal tool in the field of engineering and design. It serves as a foundation for simulating complex physical phenomena across multiple industries. From aerospace to automotive, the ability to predict how materials and structures will behave under various conditions is critical. Professionals often turn to ANSYS to create effective models that can lead to innovations and improved product designs.
This software enables its users to perform in-depth analyses that can reveal insights not easily observable in physical tests. With the help of this sophisticated modeling platform, engineers can reduce development time and enhance performance by validating their designs before making substantial investments in prototyping or manufacturing.
In this exploration of ANSYS 3D modeling, we will delve into its functional capabilities, the advantages it presents, and its adaptability to suit a wide range of requirements. Key features will be highlighted to show how well they align with user needs, and we will assess the scalability of its solutions for growing projects and businesses.
Functionality
Overview of key features
ANSYS boasts numerous features that make it an industry leader in simulation and modeling. Some of the standout functionalities include:
- Finite Element Analysis (FEA): ANSYS supports stress, thermal, and dynamic analyses, allowing users to evaluate the integrity and performance of their designs efficiently.
- Computational Fluid Dynamics (CFD): With its robust capability for fluid flow simulation, ANSYS caters to various applications, including aerodynamics and heat transfer.
- Electromagnetics Analysis: This feature helps engineers understand the electromagnetic field behavior, which is especially important in electrical and electronic components.
- User Interface: ANSYS provides an intuitive user interface, allowing even those who are not experts in modeling to navigate the software easily and efficiently.
How well the software meets user needs
The software’s functionality aligns closely with user needs in various ways. Engineers and designers often experience challenges related to simulation accuracy, speed, and integration with other software. ANSYS addresses these challenges through:
- High Precision: The algorithms used in ANSYS ensure accurate results that can be trusted for critical decision-making processes.
- Time Efficiency: The software is designed to run complex simulations faster than many alternatives, minimizing downtime and allowing for quicker iterations.
- Interoperability: ANSYS integrates easily with other software tools, enhancing the user experience and streamlining workflow.
"Effective modeling with ANSYS is a game changer that helps organizations stay ahead in competitive markets."
Scalability
Adaptability for growth
In today's fast-paced tech world, scalability is not a luxury but a necessity. ANSYS provides the flexibility needed to accommodate varying project sizes and complexities. The platform can cater to both small-scale projects as well as extensive industrial applications. Users can easily adjust their modeling workflows based on project requirements, making ANSYS a versatile choice for many organizations.
Options for additional features or modules
Furthermore, ANSYS offers a suite of additional features or modules that users can incorporate as needed. This modularity allows users to tailor their software experience to their specific demands. The available modules include:
- ANSYS Mechanical for structural analysis
- ANSYS Fluent for advanced fluid dynamics simulations
- ANSYS Maxwell focusing on electromagnetic field solutions
As projects grow, users can upgrade or add modules without needing to switch platforms, thereby supporting long-term growth strategies.
Foreword to ANSYS 3D Modeling
Overview of ANSYS Software
ANSYS is a widely respected simulation software suite that allows users to perform a variety of engineering simulations. The software includes tools for finite element analysis (FEA), computational fluid dynamics (CFD), and more. One of its strong points is the comprehensive environment it provides for 3D modeling. This capability is essential in simplifying complex problems into manageable simulations.
With ANSYS, engineers can visualize changes in performance based on physical phenomena, thus supporting more informed design choices. The integrated environment allows seamless collaboration among various engineering disciplines, enhancing overall efficiency. In particular, the 3D Modeling tools within ANSYS enable detailed depictions of geometries needed for precise analysis.
Importance of 3D Modeling in Engineering
3D modeling plays a vital role in modern engineering practices. This representation allows for the exploration of designs in a virtual space, significantly cutting down the time and costs associated with traditional prototyping. By utilizing 3D models, engineers can simulate real-world behaviors, examine stress distributions, and identify potential failure points before manufacturing.
Moreover, it supports quicker decision-making processes. By visualizing elements in three dimensions, stakeholders receive clear insights into design feasibility and performance. This aspect is critical in industries such as aerospace and automotive, where safety and performance are paramount.
"3D modeling does not merely represent a design; it enhances the understanding of how that design interacts with various physical forces."
In addition, as computational resources continue to advance, the accuracy and reliability of simulations improve, leading to more innovative engineering solutions. This progression makes it evident that ANSYS 3D Modeling is not just a tool, but a crucial element in driving engineering excellence.
Core Features of ANSYS 3D Modeling
The core features of ANSYS 3D modeling are fundamental to understanding how the software operates and how it can be effectively utilized in engineering applications. These features define the capabilities of ANSYS and showcase its strength in simulating and analyzing complex physical systems. Knowing the intricacies of these core features can significantly impact the efficiency and precision of engineering projects.
Geometric Modeling
Geometric modeling is one of the essential aspects of ANSYS 3D modeling. It allows users to create and manipulate various geometrical shapes and designs in a three-dimensional space. The accuracy of geometric models directly influences the quality of simulation results. ANSYS provides a range of tools for creating complex geometries, whether the shape is simple or intricate.
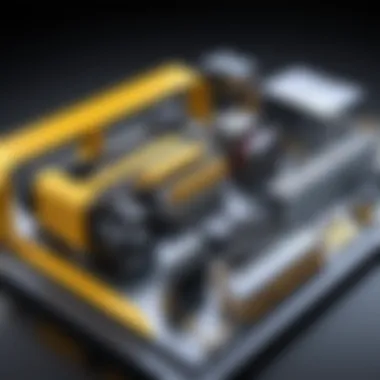

Users can utilize predefined shapes or construct custom designs from scratch. The software supports various file formats, making it easier to import geometries from other CAD tools. This flexibility is vital for engineers who prefer working with specific design software. By integrating these geometrical designs into simulations, engineers can run detailed analyses to understand how materials will perform under various conditions.
Mesh Generation
Mesh generation is another critical feature within ANSYS. Once the geometry is defined, the algorithm divides it into smaller elements to create a mesh. This process is crucial for finite element analysis (FEA) or computational fluid dynamics (CFD). A well-defined mesh results in more accurate simulation results.
ANSYS offers various meshing techniques, allowing users to select the most suitable one based on the complexity of the model. The software can automatically generate meshes, or users can define their custom meshing strategies. The ability to refine the mesh in specific areas enhances precision, especially in regions where stress or fluid flow is likely to be highest.
Boundary Conditions and Constraints
Boundary conditions and constraints fundamentally shape the outcomes of any simulation. ANSYS provides powerful tools to apply these conditions to the mesh. Engineers can define how the model interacts with its environment, including fixed supports, loads, or natural constraints.
A clear understanding of boundary conditions is essential for accurate predictions. Incorrectly assigned conditions can lead to misleading results. ANSYS simplifies this by offering intuitive ways to apply and visualize these conditions, ensuring that users can easily understand how each affects the overall simulation. Properly setting these conditions is vital for achieving reliable results in any analysis process.
"Inadequate definition of boundary conditions can significantly distort simulation outcomes, leading to erroneous conclusions about a design's viability."
In summary, the core features of ANSYS 3D modeling revolve around geometric modeling, mesh generation, and boundary conditions. Each of these elements plays a critical role in the overall functionality and effectiveness of the software. Mastery of these functions can empower engineers to create enhanced models, run accurate simulations, and ultimately drive innovation in their respective fields.
Applications of ANSYS 3D Modeling
The applications of ANSYS 3D modeling span various industries, demonstrating its versatility and efficiency in solving complex engineering problems. This section examines five key sectors where ANSYS plays a crucial role, highlighting how the software’s advanced capabilities directly contribute to innovation and effective design. By understanding these applications, professionals can better leverage ANSYS tools to meet specific challenges in their fields.
Aerospace Engineering
In aerospace engineering, ANSYS 3D modeling allows for simulation of aerodynamic properties crucial for aircraft design. Engineers can predict how a design will respond to wind and other environmental factors. With tools like Fluent, users can model airflow around wings and fuselages, optimizing designs for performance and safety. The ability to simulate stress on components during dynamic flight conditions helps reduce the risks of failure and ensures compliance with regulatory standards.
Automotive Design
The automotive industry benefits significantly from ANSYS modeling in several ways. Engineers can test various components, such as engines and chassis, under virtual operating conditions. ANSYS gives feedback on thermal management, fatigue analysis, and crashworthiness. For instance, using ANSYS Workbench, designers can quickly iterate changes, leading to a more streamlined design process. This agility can substantially reduce development time and result in higher-performing vehicles.
Civil and Structural Engineering
In civil and structural engineering, ANSYS enables the assessment of buildings, bridges, and other infrastructures. Its tools effectively evaluate structural integrity under various load conditions, including seismic and wind forces. Engineers can visualize stress points and utilize finite element analysis to simulate the behavior of materials. By predicting possible failures, they can enhance safety measures in public structures, ensuring they meet necessary codes and regulations.
Electronics and Electromagnetics
The applications of ANSYS in electronics and electromagnetics are essential in designing and optimizing components like antennas, circuit boards, and sensors. ANSYS HFSS provides tools for analyzing electromagnetic fields and optimizing the performance of high-frequency devices. This can enhance signal integrity and minimize interference, which is critical in today’s complex electronic systems. With accurate simulations, designers can achieve better reliability and performance in their electrical components.
Bioengineering Applications
Bioengineering is another area where ANSYS 3D modeling demonstrates exceptional utility. In the development of medical devices, simulations of fluid dynamics involving blood flow can aid in designing stents and implants. ANSYS can also model biocompatibility and mechanical responses of materials used in implants. By conducting virtual tests, researchers can ensure devices are safe and effective before physical prototypes are produced. This capability not only saves time and costs but also enhances patient safety.
"The versatility of ANSYS in various industries allows engineers to validate designs and make informed decisions before any physical implementation."
Benefits of Using ANSYS for 3D Modeling
Using ANSYS for 3D modeling presents a range of benefits that significantly enhance the design and analysis processes in engineering. The precision and reliability of simulations offered by ANSYS contribute to the development of superior products. This section elaborates on specific advantages such as accuracy, efficiency, and cost savings that ANSYS provides. Understanding these benefits can help professionals and businesses make informed decisions while utilizing this powerful software.
Increased Accuracy and Precision
ANSYS is renowned for its high levels of accuracy and precision in simulations. These characteristics are critical in engineering applications where small deviations can lead to substantial differences in performance. With built-in capabilities to model complex geometries and simulate real-world conditions, ANSYS allows users to conduct highly detailed analyses.
Some of the aspects that contribute to this accuracy include:
- Robust Algorithms: ANSYS integrates sophisticated algorithms that enhance computational accuracy, ensuring reliable outputs.
- Advanced Meshing Techniques: The software provides refined meshing options that capture intricate features of models without compromising speed.
- Validation Tools: ANSYS comes with tools that allow for validation of simulation results against experimental data, bridging the gap between theory and practice.
Thus, employing ANSYS for 3D modeling helps engineers avoid costly errors and improves the overall quality of designs.
Streamlined Design Process
Another significant advantage of using ANSYS is the streamlining of the design process. ANSYS software rationalizes the workflow, enabling professionals to focus on innovation rather than time-consuming repetitive tasks. The following points illustrate how ANSYS contributes to a more efficient design process:
- Integration of Tools: ANSYS allows seamless integration with other design software, facilitating collaboration and data sharing across different platforms.
- Automated Analysis: Automation features in ANSYS enable users to run multiple simulations quickly without extensive manual input, saving time and resources.
- User-Friendly Interface: The intuitive user interface simplifies complex tasks, allowing designers to work more effectively, even if they are new to the software.
As a result, teams can enhance productivity and expedite product development cycles, meeting market demands in a timely manner.
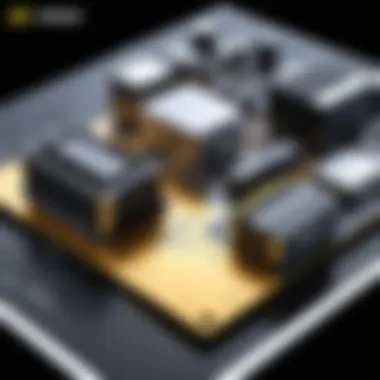

Cost Efficiency in Prototyping
Cost efficiency is a crucial benefit when using ANSYS for 3D modeling. By leveraging its simulation capabilities, companies can reduce the need for physical prototypes.
The financial advantages include:
- Reduction in Material Costs: Virtual testing minimizes waste associated with traditional prototyping, allowing for significant savings in materials.
- Lower Labor Costs: Automation and an efficient workflow lead to reduced man-hours needed for testing and design iterations.
- Faster Time-to-Market: By identifying potential issues early through simulations, businesses can avoid the costs associated with late-stage design changes.
"Using ANSYS can lead to profound cost reductions by minimizing physical prototype requirements while ensuring design integrity."
Challenges and Limitations of ANSYS 3D Modeling
While ANSYS is renowned for its robust features and capabilities, it is essential to recognize the challenges and limitations associated with its use. Understanding these aspects is crucial for professionals who wish to leverage the software effectively in their projects. The challenges do require thoughtful consideration, particularly for businesses looking to adopt or upgrade their existing modeling tools. Addressing these limitations directly can make a significant difference in how effectively engineers can utilize ANSYS for their purposes.
Steep Learning Curve
ANSYS's extensive functionalities come with a steep learning curve that many new users encounter. While the software is powerful, it may feel overwhelming to those who are not familiar with the environment. Engineers transitioning from simpler modeling software might find the variety of choices and tools disorienting.
This learning curve can impact productivity in the early stages of adoption. Users need time to familiarize themselves with the interface, commands, and capabilities.
- Training is crucial: Organizations often invest in training programs to help employees get up to speed. Courses and tutorials can mitigate the learning challenges, but they do require additional resources.
- Documentation is vital: ANSYS offers comprehensive documentation. However, the technical language may not always be accessible for beginners, contributing to longer onboarding periods.
In summary, the initial time and effort required to learn ANSYS can be a barrier for some users. Nevertheless, once mastered, the software opens doors to advanced simulation possibilities.
High Hardware Requirements
Another notable limitation of ANSYS 3D modeling is the high hardware requirements needed to run the software efficiently. Complex simulations demand significant computational power. Businesses need to ensure their systems meet or exceed the recommended specifications.
- Performance and cost: Investing in high-performance hardware can be costly. This investment may not be feasible for smaller firms or startups.
- Optimizing resources: Users often face challenges in optimizing their hardware resources. Without proper configuration, hardware capabilities can be underutilized, leading to inefficient simulations.
Moreover, as simulations become more intricate and detailed, the demand for better technology will only increase. Therefore, planning for compatible hardware becomes necessary from the outset.
Efficient use of ANSYS necessitates both software proficiency and adequate hardware capabilities. Teams must ensure their technological foundation matches the demands of ANSYS for optimal results.
Workflow in ANSYS 3D Modeling
The workflow in ANSYS 3D modeling is essential for achieving effective results in engineering simulations. It encompasses the entire process from the initial planning stages to the presentation of results. A well-structured workflow permits the user to navigate through complex modeling tasks efficiently, ensuring clarity and coherence in the outcomes.
Project Setup and Planning
Setting up a project involves critical decision-making and preparation. Users must define objectives clearly before starting. This includes selecting the type of analysis, understanding material properties, and identifying constraints. The planning stage lays the groundwork for a successful simulation.
- Defining Objectives: Clearly specifying what the project aims to achieve helps in focusing efforts.
- Selecting Appropriate Materials: Inputting accurate properties allows for more realistic simulations.
- Establishing Geometry: The shape and structure must be accurately defined as they impact performance.
In this stage, utilizing ANSYS tools to draft a preliminary geometric model can provide substantial benefits. This helps in visualizing how different components will interact and perform under various conditions.
Executing Simulations
With the groundwork laid, executing simulations becomes the next critical step. In ANSYS, simulations can vary from static analyses to dynamic behaviors. Each type requires specific parameters and settings.
- Choosing the Right Solver: Different solvers may yield varied insights. Selecting the appropriate one ensures reliability.
- Defining Boundary Conditions: These are crucial for realistic results. Specifying how the object interacts with external forces is key.
- Running the Simulation: After settings are confirmed, users can execute the simulation. It is important to monitor for any errors during the process.
Regularly saving progress through this stage is advisable to avoid losing any work. A well-executed simulation can bring significant insights for further analysis.
Interpreting Results
The final segment of the workflow involves interpreting results accurately. This is where the data gathered from simulations gets analyzed for practical applications. Understanding results may require critical thinking because the outputs can be complex.
- Visualizing Data: Using ANSYS tools to create graphs and charts helps in making sense of numerical data.
- Comparative Analysis: Evaluating results against theoretical expectations or past results can uncover discrepancies.
- Reporting Findings: Documenting the insights from the simulation is important for further development or presentation to stakeholders.
A thorough interpretation transforms simulation data into actionable insights, facilitating informed decisions in engineering practices.
In summary, a structured workflow in ANSYS 3D modeling is vital for effective project execution. Each stage—setup and planning, executing simulations, and interpreting results—plays a significant role in the overall success of the modeling process. As engineers become proficient in these workflows, they unlock the software’s full potential, enhancing both productivity and innovation.
Integration with Other Tools
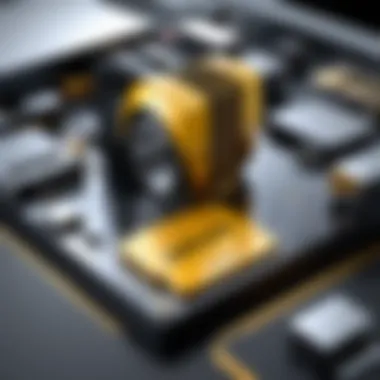

Integration with various tools is significant in enhancing the capabilities of ANSYS 3D Modeling. As industries embrace complex solutions, the ability to seamlessly connect different software applications becomes essential for achieving efficiency, accuracy, and innovation. In this section, we will delve into two critical aspects of integration: CAD Integration and Collaboration with Other Software.
CAD Integration
CAD integration stands as a cornerstone of ANSYS 3D Modeling. The ability to import geometric data from Computer-Aided Design systems like SolidWorks, CATIA, or Autodesk Inventor significantly streamlines the modeling process. This direct transfer of information ensures that the geometry created in CAD remains intact and ready for simulation tasks.
Benefits of CAD integration include:
- Time savings: Automated import mechanisms reduce manual entry errors and speed up workflow.
- Accuracy: Maintaining dimensional integrity is crucial, and CAD integrations preserve this fact.
- Flexibility: Users can make design iterations in the CAD software and directly refresh their ANSYS models without starting over.
Considerations for effective CAD integration involve ensuring compatibility between software versions and checking for geometric errors post-import. Correcting errors found during this process is crucial to avoid issues in later simulation stages.
Collaboration with Other Software
Collaborating with other software enhances the capabilities of ANSYS 3D Modeling. This collaboration is critical for multidisciplinary projects. Users can integrate simulation tools that specialize in areas like fluid dynamics or thermal analysis, allowing for a comprehensive approach to engineering problems.
The key advantages include:
- Enhanced Functionality: By using specialized software alongside ANSYS, you can tackle niche problems more effectively.
- Improved Data Sharing: Compatibility with platforms like MATLAB or Python for advanced scripting and data analytics is essential.
- Cross-Disciplinary Insights: Collaboration fosters the exchange of ideas and solutions, making it possible to innovate beyond the traditional boundaries of engineering.
When engaging in collaboration, it is essential to establish clear data formats and communication protocols to prevent data loss or corruption.
Successful integration and collaboration thus maximize the potential of ANSYS 3D Modeling, leading to superior product design and performance.
In summary, the importance of integration with other tools in ANSYS 3D Modeling cannot be understated. This aspect not only enhances efficiency but also allows professionals to leverage the strengths of different software applications. As technology continues to evolve, the need for harmonized workflows will only increase, making these integrations vital for future advancements.
Future Trends in 3D Modeling with ANSYS
The future of 3D modeling with ANSYS encompasses rapid advancements in technology that drive efficiency and accuracy. Understanding these trends is crucial for professionals who aim to stay ahead in their respective fields. Increased integration of AI and machine learning, alongside enhanced simulation capabilities, is reshaping the landscape of engineering simulation.
Advancements in AI and Machine Learning
AI and machine learning are transforming how ANSYS operates. These technologies allow for smarter data analysis and faster decision-making in 3D modeling processes. By utilizing AI algorithms, engineers can automate complex tasks, saving time and reducing the potential for human errors. For instance, optimization processes that previously required extensive trial and error can now be streamlined.
Moreover, machine learning can enhance predictive analytics. This means that engineers can predict outcomes based on historical data, leading to more informed design choices. With ANSYS leveraging AI, engineers can simulate countless scenarios, gaining insights that would otherwise be impossible. This shift not only boosts innovation but also creates competitive advantages in industries relying on precision and effectiveness.
Enhanced Simulation Capabilities
Enhanced simulation capabilities within ANSYS are pivotal for addressing increasingly sophisticated engineering challenges. Modern engineering projects call for simulations that can accurately represent dynamic and complex behavior under varying conditions. ANSYS is evolving to meet these needs by providing more robust tools that simulate real-world phenomena with higher fidelity.
The software is incorporating multi-physics capabilities allowing it to model interactions between different physical phenomena. This integration enables a more comprehensive view of how a system performs under various conditions. For example, in aerospace applications, engineers can analyze the structural integrity while simultaneously considering aerodynamic effects. This leads to more reliable designs and reduces the risk of failures in real-world applications.
In summary, the coupling of AI with enhanced simulation tools signifies a major leap forward in the capability of ANSYS. By embracing these trends, businesses can improve product quality, optimize design processes, and ultimately secure a greater market share.
"The integration of AI in simulation software marks a pivotal moment in engineering, with potential benefits that extend beyond traditional boundaries."
By staying updated on these future trends, professionals can effectively navigate the evolving landscape of 3D modeling and utilize ANSYS to its fullest potential.
Closure
In concluding this article, it’s essential to recognize the critical role that ANSYS 3D modeling plays in modern engineering practices. The capacity of ANSYS to simulate complex physical phenomena is a significant asset for professionals across various industries. This software not only enhances accuracy but also optimizes the efficiency of the design process.
Specific Elements:
Throughout the discussions, several core elements of ANSYS have emerged. These include geometric modeling, mesh generation, and the imposition of boundary conditions, all of which are foundational for reliable simulation outcomes. Each of these features works in harmony to ensure that engineers can trust the results produced by the software.
Benefits:
The benefits of utilizing ANSYS for 3D modeling extend beyond technical accuracy. The ability to streamline processes translates into considerable time savings and cost reductions throughout the project lifecycle. When teams can accurately predict behaviors and outcomes, it minimizes the need for expensive prototype iterations, ultimately improving overall project delivery timelines.
Considerations about Conclusion:
As professionals engage with ANSYS 3D modeling, it is important to remain cognizant of the challenges that accompany its use. A steep learning curve, for example, can deter some newcomers. However, the long-term advantages, such as enhanced simulation capabilities and integration with other tools, outweigh these initial obstacles. Understanding these nuances cultivates a more strategic approach in utilizing ANSYS effectively.
In summary, ANSYS 3D modeling stands out as a crucial tool for engineers aiming to push boundaries in design and analysis. Its comprehensive features and capabilities, when properly leveraged, have the potential to lead to significant innovations in the engineering field.
Summary of Insights
In reviewing the insights gained from this exploration of ANSYS 3D modeling, it becomes clearer how integral this software is within various engineering sectors. The structured workflows showcase the methodical approach necessary to fully engage with the different functionalities available. Features such as advanced mesh generation and geometry manipulation allow users to accurately represent physical scenarios. This methodical approach helps in bridging the gap between theoretical models and practical applications.
In essence, ANSYS delivers a robust platform that not only meets but also anticipates the evolving needs of engineers.
Final Thoughts on ANSYS 3D Modeling
The future of ANSYS 3D modeling is promising, particularly as advancements in artificial intelligence and machine learning take hold. These innovations will likely elevate simulation accuracy and efficiency even further. Moreover, as industries adapt to increasingly complex challenges, the integration capabilities of ANSYS with other software solutions will become increasingly vital.
ANSYS provides the foundation for engineers not just to visualize designs but to predict and alter outcomes based on real-world variables. As technology continues to advance, engaging with ANSYS will remain a strategic choice for professionals keen on achieving deep insights into their projects.