Procore Equipment Tracking: An In-Depth Analysis
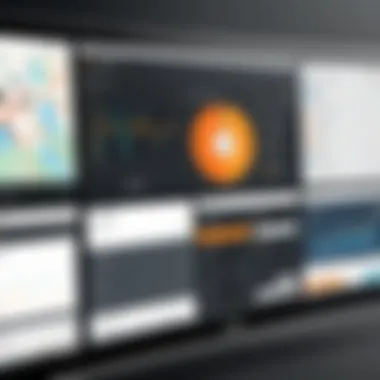
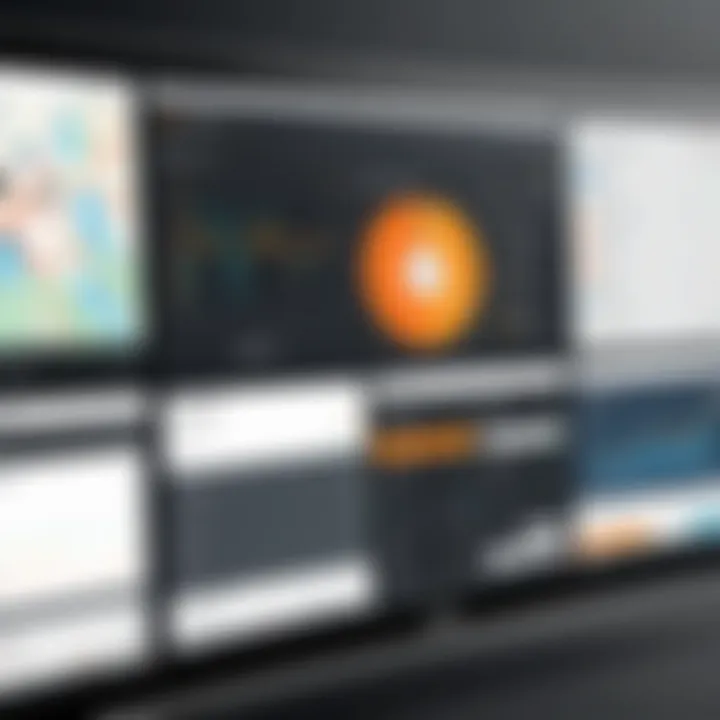
Intro
Procore Equipment Tracking offers a valuable solution for managing construction machinery and tools. It aims to solve several challenges inherent in construction management. Efficient tracking of equipment is crucial for minimizing downtime and ensuring projects are completed on schedule. This analysis focuses on the features and benefits of this software, as well as its implications for construction efficiency and accuracy.
In a construction environment, proper equipment management is not just about knowing what tools are available. It encompasses understanding their location, usage, maintenance needs, and scheduling. The functionality of Procore Equipment Tracking allows managers to keep close tabs on these factors. It enhances day-to-day operations through effective integration with existing workflows.
Functionality
Overview of key features
Procore Equipment Tracking is designed to meet the unique demands of construction projects. Some key features include:
- Real-time tracking: Users can precisely see where their equipment is located at any time.
- Usage reporting: The software generates detailed reports on tool usage, helping managers understand which equipment is most effective.
- Maintenance alerts: Notifications ensure that equipment is maintained on schedule, preventing breakdowns and ensuring safety.
- Integration capabilities: Procore can connect with other tools and systems used in construction management, which maximizes its utility.
These features aim to streamline operations, reduce redundancy, and enhance overall project visibility.
How well the software meets user needs
Feedback suggests that many users find Procore Equipment Tracking intuitive and straightforward. Its dashboard presents data in a user-friendly manner, making it easier for both seasoned managers and newcomers to navigate its functionality. The real-time updates contribute significantly to the operational efficiency of construction firms.
However, some users point out that there may be a learning curve during the initial setup. Despite this, once established, the system shows notable effectiveness in managing equipment lifecycles.
Scalability
Adaptability for growth
As construction projects vary greatly in size and scope, scalability is an important aspect of Procore Equipment Tracking. The platform is designed to grow with organizations. As a company expands, it can incorporate additional users or features based on evolving needs.
Options for additional features or modules
Procore provides the option to add modules tailored to specific requirements, such as enhanced reporting tools or advanced analytics features. This adaptability allows firms to customize their experience and maximize their investment in the system.
Understanding Procore Equipment Tracking
Understanding Procore Equipment Tracking is critical in the realm of construction management. This tool provides a framework for organizing and managing equipment, ultimately enhancing project efficiency and accuracy. Equipment tracking addresses a common issue in the construction industry: the loss or mismanagement of costly machinery and tools. Streamlining equipment logistics can lead to significant cost savings and improved project timelines.
For construction managers and supervisors, effective equipment tracking integrates seamlessly into their workflow. It enables them to keep tabs on resources in real time. As a result, it reduces downtime caused by misplaced tools and machinery. Furthermore, the insights gained from using Procore equipment tracking can aid in making informed decisions about purchasing, renting, and maintaining equipment.
Definition and Overview
Procore Equipment Tracking is a cloud-based solution designed to help users monitor and manage equipment used in construction projects. This platform allows users to log every piece of equipment, track its status, and determine its location at any given time. With the help of mobile devices, field personnel can update the status of equipment, thus providing real-time data back to the project managers.
A key aspect of this system is its ability to consolidate information in one central location, allowing for enhanced visibility into equipment usage across all projects. This not only aids management but also provides valuable data analytics for future planning.
Key Features of Procore Equipment Tracking
Procore Equipment Tracking encompasses various features tailored to enhance user experience and efficiency. Some of the notable features include:
- Real-Time Updates: Users can receive immediate notifications about equipment status changes, which assist in decision-making.
- Location Tracking: GPS integration allows managers to see where equipment is located and its usage history.
- Usage Reporting: Users can generate reports that detail how often equipment has been used, which informs maintenance schedules and purchasing decisions.
- Maintenance Scheduling: Built-in tools help track when equipment needs servicing, reducing the chances of equipment failure on-site.
- User-Friendly Interface: The design simplifies navigation for users, making it easier to adopt the platform without extensive training.
Industry Applications
Procore Equipment Tracking has applications in various sectors within the construction industry. It is beneficial for:
- General Contractors: They use the tool for managing multiple projects and resources simultaneously.
- Specialty Contractors: These users track specific equipment types necessary for specialized tasks.
- Rental Companies: They can monitor the usage and location of rented equipment, optimizing their fleet management.
- Project Managers: Gaining insights from data helps with planning and resource allocation for current and future projects.
Procore's features are designed to cater to the diverse needs of these industries, ensuring that they can maximize their resource utilization effectively.
Advantages of Procore Equipment Tracking
Procore Equipment Tracking offers several advantages that contribute significantly to the construction management landscape. Understanding these benefits is essential for companies looking to optimize resources and improve operational control. By utilizing Procore’s platform, organizations can enhance their productivity while managing equipment effectively. This section will explore three main advantages: increased operational efficiency, enhanced data accuracy, and real-time monitoring capabilities.
Increased Operational Efficiency
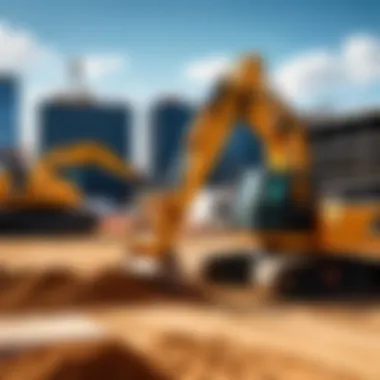
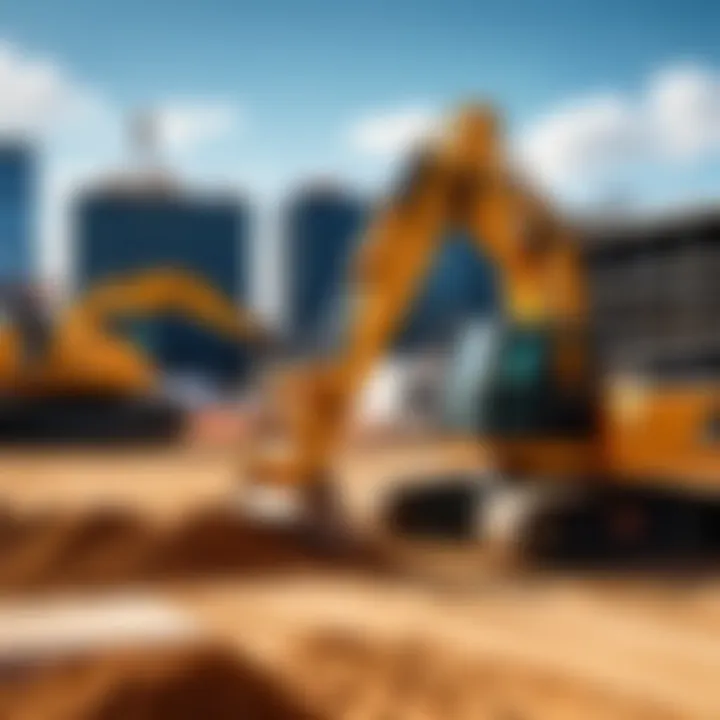
The application of Procore Equipment Tracking brings forth remarkable operational efficiency. Construction teams can streamline equipment management processes, reducing downtime and optimizing resource allocation. When equipment tracking is synchronized with project schedules, it ensures that the right tools and machines are available at the right time and place. This alignment helps avoid delays caused by unavailable equipment, which can be costly.
Moreover, Procore allows for easy check-in and check-out of equipment, which simplifies tracking ownership and usage. This feature reduces the time spent managing inventory manually. Maintenance schedules can be integrated into the system, allowing companies to forecast when equipment needs servicing. The proactive approach to maintenance reduces unexpected breakdowns, further enhancing overall efficiency in project execution. Companies looking to maximize their operational capabilities should seriously consider adopting these tracking systems.
Enhanced Data Accuracy
Data accuracy plays a crucial role in informed decision-making within construction projects. Procore Equipment Tracking offers built-in capabilities that ensure precise tracking of all equipment. By minimizing human error, the platform provides reliable data that organizations can trust. Accurate data contributes to effective project planning, resource allocation, and budgeting.
For instance, with accurate tracking of equipment usage, project managers can analyze which tools are being utilized most efficiently and which are underused. This analysis leads to better purchasing decisions and can even influence rental choices. Companies can also benefit by having a clearer picture of equipment depreciation, helping them manage financial implications wisely.
Real-Time Monitoring Capabilities
One of the standout features of Procore Equipment Tracking is the real-time monitoring it provides. This capability allows teams to see the location and status of their equipment at any given moment. Knowing where equipment is located helps in planning operations and can reduce the chances of theft or loss. For example, the system can alert project managers if equipment is moved outside a designated area, allowing for swift action.
Additionally, real-time data updates keep everyone informed, which is vital in a fast-paced construction environment. This feature facilitates better communication among team members, as they have access to the same up-to-date information without delays. Thus, immediate updates would enhance responsiveness to issues that arise, whether they are equipment-related or project-specific. As a result, project timelines can be adhered to more strictly, boosting overall project success.
"Effective equipment management leads to smoother project execution, ultimately yielding business growth."
Implementation Strategies for Procore Equipment Tracking
Implementing Procore Equipment Tracking effectively is crucial for maximizing its potential in construction management. The right implementation strategy leads to improved tracking, better project management, and increased equipment utilization. It requires careful planning and a thorough understanding of both organizational needs and Procore’s capabilities. Each phase of implementation must consider not just the technical aspects, but also the human elements involved in the transition.
Pre-Implementation Considerations
Before diving into the implementation of Procore Equipment Tracking, it is essential to conduct a comprehensive assessment of the organization’s needs. This includes:
- Identifying Key Objectives: Define what the organization aims to achieve with Procore Equipment Tracking. Whether it's improving efficiency, reducing costs, or enhancing accuracy, these goals should guide the entire process.
- Infrastructure Assessment: Evaluate existing systems and infrastructure to ascertain their compatibility with Procore. Identifying gaps will aid in smoother transitions.
- Stakeholder Engagement: Engaging key stakeholders early is vital. Their insights can inform choices and build buy-in, which is crucial for successful adoption.
- Budget Constraints: Determine the financial resources available for the implementation. Allocating the right budget ensures that all aspects of the transition are covered without unnecessary overspending.
Such careful preparation lays the groundwork for a successful implementation.
Step-by-Step Guide to Implementation
Implementing Procore Equipment Tracking can be approached through a systematic process:
- Planning Phase: Develop a detailed implementation plan with timelines and milestones. Clearly outline roles and responsibilities among team members.
- Setup and Configuration: Begin by setting up the Procore system according to the organization's specifications. Configure settings to match the unique needs of the projects and teams involved.
- Data Migration: Transfer existing equipment data into Procore. This may include importing data from spreadsheets or existing systems. Verifying data accuracy is crucial at this stage.
- Integration with Other Systems: If necessary, integrate Procore with other project management tools or software that the organization currently uses. This enhances workflow and avoids data silos.
- Pilot Testing: Before full deployment, conduct a pilot test with a small project. This helps identify any potential issues and allows for adjustments based on real-world feedback.
- Full Deployment: Roll out the system across all projects following a successful pilot. Ensure that all personnel are aware and ready to utilize the new system.
- Monitor and Adjust: After full deployment, continuously monitor the system’s performance. Be ready to make adjustments based on user feedback and changing project requirements.
Following this structured approach minimizes disruptions and optimizes efficiency.
Training Needs and Resources
Training is a vital component of implementing Procore Equipment Tracking. Comprehensive training ensures that users can effectively navigate and utilize the system:
- Training Programs: Develop structured training programs tailored for different user groups, such as project managers and field personnel. Offer both in-person and online courses to accommodate various learning styles.
- Resource Availability: Provide accessible resources, such as manuals, tutorials, and FAQs. This ensures users can find information quickly when needed, reducing reliance on immediate support.
- User Support Channels: Establish clear channels for user support. Having accessible resources for troubleshooting enhances confidence in using the system.
- Feedback Gathering: Continually gather feedback regarding the training effectiveness and the system's usability. Use this information to refine training programs regularly.
Integration and Compatibility
Integration and compatibility are crucial to maximizing the effectiveness of Procore Equipment Tracking. As construction management becomes more reliant on various software solutions, finding a cohesive operation among these technologies is key. Seamless integration allows for data consistency and operational efficiency. It reduces the chances of manual entry errors and miscommunication across different platforms, which often lead to wasted time and resources.
When companies implement Procore Equipment Tracking, they must consider how it will work alongside existing systems. Proper integration means not only connecting with direct competitors but also ensuring compatibility with tools used for project management, inventory control, and even financial software. A well-designed integration can enhance project workflows and reporting accuracy.
Third-Party Software Integration
One of the significant advantages of Procore Equipment Tracking is its ability to integrate with third-party software. This includes tools like Autodesk, Microsoft Project, and accounting platforms such as QuickBooks. The integration enables users to centralize their data, which helps make analysis more straightforward.
"Integration capabilities can mean the difference between functional isolation and central data visibility across projects."
This functionality improves communication between distinct departments, which is vital for timely decision-making. Moreover, the ability to pull data from systems users already utilize reduces the friction of adoption, making the transition to Procore much smoother. However, careful planning is required during the integration stages to ensure that the systems communicate effectively without data loss.
Data Migration Challenges
A significant hurdle in adopting Procore Equipment Tracking is often the data migration process. Companies typically have extensive historical records stored across multiple platforms. The challenge lies in transferring this data into Procore while maintaining accuracy and integrity.
It's essential to assess the existing data’s quality before migration. This involves cleaning up records, removing duplicates, or addressing inconsistencies. A flawed migration can lead to incorrect information being used in project management, which can severely impact operational efficiency.
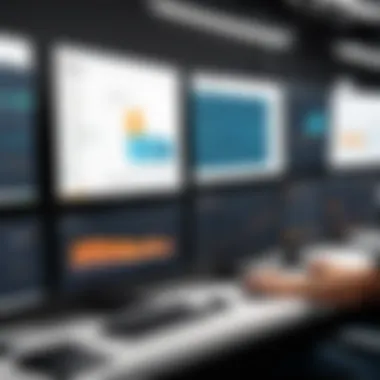
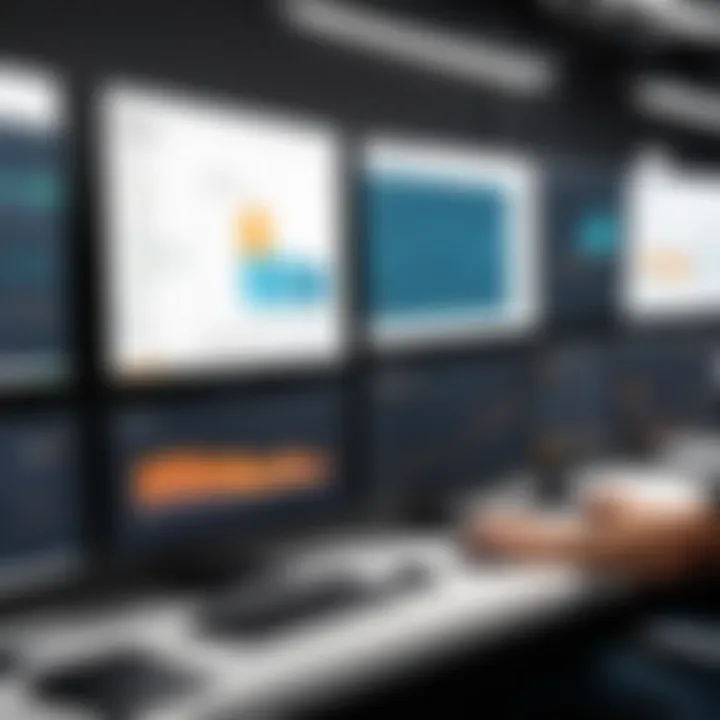
Companies should establish a clear strategy for data migration. This includes creating deadlines, determining who will oversee the process, and deciding how historical data will be used once integrated into the new system. Furthermore, ongoing monitoring post-migration can highlight unexpected issues early on, allowing teams to respond promptly.
APIs and Customization Options
APIs, or Application Programming Interfaces, play a vital role in the integration of Procore Equipment Tracking with other software systems. Procore provides robust API options, allowing for customized integrations tailored to specific business needs. This flexibility enables organizations to create solutions that fit their unique workflows and requirements.
Organizations should assess their integration needs before implementing Procore to identify which APIs will be crucial. As technology evolves, the ability to customize these interfaces will become increasingly important. This adaptability can result in significant time and cost savings, making API utilization a key aspect of an efficient equipment tracking framework.
In summary, addressing integration and compatibility comprehensively is essential when considering Procore Equipment Tracking. Successful integration with third-party software can lead to improved workflow efficiency, while careful management of data migration challenges can ensure accurate, reliable information is at the team’s disposal. Finally, leveraging APIs and customization options empowers organizations to refine their use of Procore for optimal results.
Challenges in Equipment Tracking
Effective equipment tracking is critical for managing construction projects. However, organizations often face several challenges when integrating tracking solutions like Procore. Recognizing and addressing these challenges can significantly enhance the utility and effectiveness of equipment tracking systems. Understanding these hurdles aids in mitigating risks while optimizing equipment performance. In this section, we will delve into some common implementation hurdles, user resistance, and ongoing support and maintenance issues associated with Procore Equipment Tracking.
Common Implementation Hurdles
Implementing Procore Equipment Tracking is not without its challenges. Many organizations encounter obstacles such as:
- Inadequate Training: One common hurdle is the lack of thorough training for personnel. Without proper guidance, users may struggle to utilize the system's features effectively.
- Data Entry Errors: Accurate equipment tracking necessitates precise data recording. Mistakes in data entry can lead to cascading issues, uninformed decisions, and inflated costs.
- Integration Issues: Procore may need to interface with other software or systems. This integration can create compatibility issues that delay full implementation.
- Cost Concerns: Some businesses worry about the initial investment and ongoing costs associated with equipment tracking technologies. This can lead to reluctance in adopting new systems.
Addressing these implementation issues early on paves the way for smoother adoption and can result in immediate benefits of efficiency and accuracy.
Addressing User Resistance
User resistance presents a significant barrier in the adoption of Procore Equipment Tracking. Employees may resist change for various reasons:
- Familiarity with Previous Systems: Users often find comfort in existing methods, making them hesitant to adopt new technologies.
- Fear of Job Security: There can be concerns about job displacement resulting from automated tracking.
- Perceived Complexity: If users perceive the new system as complicated, they may refuse to engage fully.
To combat resistance, communication is key.
- Involve Users Early: Engaging users in the decision-making process can create a sense of ownership.
- Provide Comprehensive Training: Tailored training sessions that highlight the system's benefits can help alleviate fears and build confidence.
By proactively addressing user resistance, organizations can promote acceptance and ease the transition to new equipment tracking systems.
Ongoing Support and Maintenance
Once Procore Equipment Tracking is implemented, maintaining functionality and user satisfaction becomes critical. Ongoing support and maintenance ensure that organizations maximize their investment:
- Regular System Updates: Keeping the software up-to-date minimizes security risks and introduces new features that enhance performance.
- User Feedback Mechanisms: Establishing channels for user feedback can help identify areas needing improvement, fostering a culture of continuous enhancement.
- Dedicated Support Teams: Having access to reliable technical support can resolve issues quickly, ensuring minimal disruption to operations.
Creating an environment where users feel supported contributes to long-term success in equipment tracking.
Investing in both the implementation phase and ongoing support is crucial for reaping the full benefits of Procore Equipment Tracking. Without these elements, organizations risk encountering persistent challenges that could hamper their goals.
Best Practices for Effective Use
Utilizing Procore Equipment Tracking effectively hinges on certain best practices. Such guidelines ensure that the investment in this tracking system provides its full range of benefits. To maximize operational efficiency and enhance accuracy in equipment tracking, it is crucial to adopt specific strategies. This section delves into practical approaches that can foster the most effective use of Procore's platform.
Regular Updates and Reporting
Regular updates are vital in maintaining the accuracy of equipment data. Users should make it a routine to update equipment status and location promptly. This practice helps in ensuring that all team members are aware of the current state of the equipment, reducing miscommunication. To facilitate this, organizations can set automatic reminders within Procore. These reminders can help streamline the process of reporting and updating data, ensuring that it remains current.
Furthermore, generating regular reports allows stakeholders to analyze equipment usage patterns. These insights are critical for identifying equipment that may be underutilized or over-utilized. Reports can also inform budgetary decisions and equipment procurement processes, ensuring resource allocations align with actual needs.
Data Analysis for Decision Making
Data analysis plays an important role in refining operational decisions. Procore provides various tools for analyzing equipment utilization and performance metrics. By leveraging this data, decision-makers can assess which pieces of equipment are most efficient or which are incurring excessive costs.
Organizations can implement analytical dashboards that visualize key performance indicators. For example, equipment downtime can be tracked over time, enabling teams to understand trends and devise strategies for improvement. Additionally, analyzing historical data can support predictive modeling, allowing for proactive maintenance and reduced equipment failure rates. This approach not only enhances overall efficiency but also contributes to longer equipment lifespans.
User Engagement and Feedback Mechanisms
Engaging users is crucial to the success of any tracking system. Regular feedback from team members who use Procore Equipment Tracking can provide invaluable insight into its functionality and effectiveness. Organizations should create mechanisms for collecting user feedback, such as surveys or regular discussion forums. This can help identify pain points and areas for improvement.
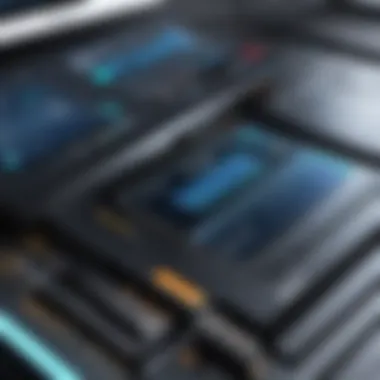
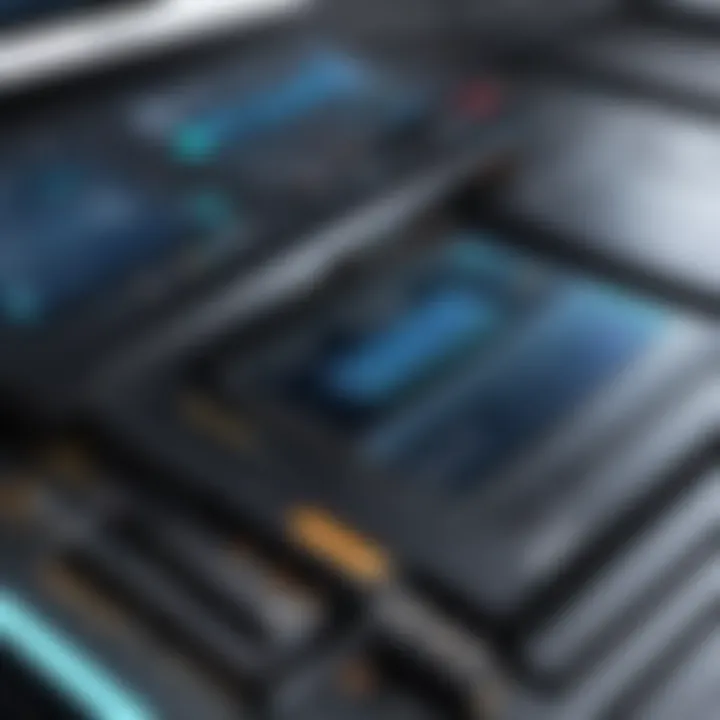
Encouraging users to share their experiences also fosters a culture of ownership and accountability. When users feel their input is valued, they are more likely to embrace the system fully. Furthermore, acting on user feedback helps optimize the tracking system continually, making it more adaptable to the evolving needs of the organization.
"User engagement and feedback are key to unlocking the full potential of any software system."
Case Studies and Success Stories
Case studies serve as practical examples that illustrate how Procore Equipment Tracking can be applied in real-world scenarios. Through these stories, potential users and stakeholders gain insight into the measurable benefits of the platform. They provide a clearer view of its functionality and potential impact on both small and large-scale projects. By examining these cases, businesses can identify strategies that align with their objectives and avoid common pitfalls encountered during implementation.
Small Business Implementation
For small businesses, effective equipment tracking can be transformative. One notable case is a small construction firm that adopted Procore Equipment Tracking to streamline its operations. Before using the platform, the company faced challenges in managing assets, often leading to wasted time and resources. After implementation, they reported significant improvements. With Procore, they achieved better visibility of their equipment locations and utilization rates. This led to reduced operational costs and improved project timelines, allowing the firm to take on larger projects with confidence. This example emphasizes that even small-scale operations can leverage technology to enhance efficiency and maintain competitive advantage.
Large Scale Project Management
In the realm of large-scale project management, Procore Equipment Tracking plays a crucial role in coordinating widespread activities. A leading construction company was tasked with building a massive infrastructure project. The complexities involved, including multiple sites and extensive equipment usage, necessitated sophisticated tracking methods. Implementing Procore enabled real-time data sharing among various teams. This collaboration allowed for quick adjustments in equipment allocation and minimized downtime. The company's ability to manage its resources effectively resulted in a project completed ahead of schedule and under budget. This illustrates that for larger organizations, leveraging advanced equipment tracking becomes essential for maximizing output and enhancing project management efficiency.
Comparative Analysis with Competitors
A comparative analysis of Procore Equipment Tracking against competitors reveals critical insights into its effectiveness. For instance, when evaluated alongside platforms like Autodesk and Viewpoint, Procore's user interface stands out for its intuitiveness. Additionally, its integration capabilities offer a seamless transition from other software solutions, which is a significant advantage. Through various case studies, organizations have highlighted that Procore not only offers better real-time tracking but also superior customer support. The concrete data collected from these comparisons can guide prospective users in making informed decisions about which equipment tracking solution best fits their needs.
"The choice of equipment tracking software can greatly influence project success. Careful analysis of case studies allows companies to see what works and what does not."
Ultimately, the examination of case studies and success stories enhances understanding of how Procore Equipment Tracking functions in diverse scenarios, driving home the importance of real-world experience in evaluating software efficacy.
Future Trends in Equipment Tracking
As the construction industry embraces technological advancements, the future of equipment tracking continues to evolve. Understanding these trends is crucial for any firm looking to maintain a competitive edge. Companies that adapt to changes in technology can optimize their operations, enhance project outcomes, and improve overall equipment management. This section delves deep into three significant trends seen in the realm of equipment tracking.
Integration with IoT Technologies
The Internet of Things (IoT) facilitates connectivity among devices, allowing for seamless data sharing. In the context of equipment tracking, integrating IoT technologies can provide real-time data on location, usage patterns, and condition of equipment. The primary benefits include:
- Enhanced visibility: Equipment management becomes more transparent as every asset is connected and its status is updated live.
- Improved efficiency: Companies can monitor equipment usage and optimize maintenance schedules. This proactive approach reduces downtime and maximizes usage.
- Data-driven decisions: The acquisition of data allows for intelligent decisions based on actual use rather than assumptions.
This integration is not without challenges. Security concerns regarding data breaches and the need for robust infrastructure pose significant hurdles. However, the potential benefits far outweigh the risks when implemented correctly.
Predictive Analytics in Equipment Management
Predictive analytics leverages data analysis techniques to forecast future outcomes based on historical data. For equipment management, this means predicting when maintenance is required or identifying potential failures before they occur. Key considerations include:
- Reduced downtime: By anticipating equipment failures, firms can schedule repairs during off-peak hours, avoiding disruptions.
- Cost savings: Timely interventions lead to less costly repairs and prevent the need for emergency replacements.
- Better resource allocation: Understanding usage patterns allows for smarter deployment of equipment across projects.
Effective predictive analytics depends on the quality of data collected and the algorithms used for analysis. Companies must invest in training and tools to harness this capability fully.
The Role of Artificial Intelligence
Artificial Intelligence (AI) is becoming an integral part of equipment tracking. By processing vast amounts of data, AI can enhance existing tracking systems. Its relevance in this field includes:
- Automation: AI can automate routine tasks such as inventory checks, freeing up staff for strategic activities.
- Enhanced analysis: AI algorithms can analyze usage patterns more efficiently than traditional methods, leading to timely insights.
- Risk management: AI can identify patterns in equipment failure and suggest preventive measures.
As AI technology continues to advance, its applications in equipment tracking will likely expand, creating smarter environments that adapt to operational demands.
"The integration of IoT, predictive analytics, and AI is transforming equipment tracking into a more agile and responsive process."
In summary, recognizing these trends allows construction firms to stay ahead of the curve. By focusing on integration with IoT, leveraging predictive analytics, and harnessing the power of AI, organizations can optimize equipment tracking, thereby improving overall project performance.
Epilogue and Recommendations
In summarizing the insights on Procore Equipment Tracking, it becomes evident that the system plays a crucial role in modern construction management. By effectively managing equipment, it not only streamlines operations but also enhances overall project outcomes. Organizations that integrate Procore into their workflows can expect significant benefits, including improved tracking accuracy and operational efficiency.
The key elements discussed throughout this article emphasize the importance of implementation strategies, integration with existing systems, and user engagement. Each of these aspects supports a seamless transition to using Procore. The adaptability of Procore Equipment Tracking to various industry needs further strengthens its relevance, making it a valuable tool.
Summarizing Key Takeaways
- Operational Efficiency: Procore Equipment Tracking optimizes equipment utilization, reducing downtime. This translates into cost savings and heightened productivity across construction sites.
- Data Accuracy: The platform enhances the precision of equipment data, minimizing errors and uncertainties in reporting and scheduling.
- Real-Time Monitoring: With real-time tracking, project managers gain immediate visibility into the location and status of equipment, allowing for quicker decision-making.
- User Adoption: Successful implementation hinges on thorough training and support, ensuring users are comfortable with the system.
- Integration Framework: The ability to interface with other third-party applications helps streamline operations and enhances functionalities without significant modifications.
Future Considerations for Implementation
Looking ahead, organizations considering Procore Equipment Tracking should focus on several key considerations:
- Customization: Assess the need for APIs and customization options. Tailoring the software to fit specific business processes can significantly enhance effectiveness.
- Scalability: As projects grow and evolve, it is essential to evaluate the scalability of Procore. The system should be feasible to expand without compromising functionality.
- Feedback Mechanism: Establish a robust feedback loop with users. Continuous improvements based on user experiences can refine the overall service and integration.
- Trends in Technology: Staying updated with future trends, such as advancements in AI and predictive analytics, can further optimize equipment tracking processes.