Implementing a Quality Management System for Small Businesses
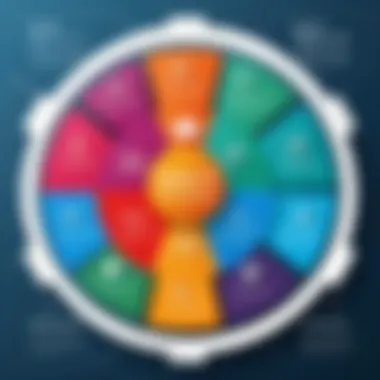
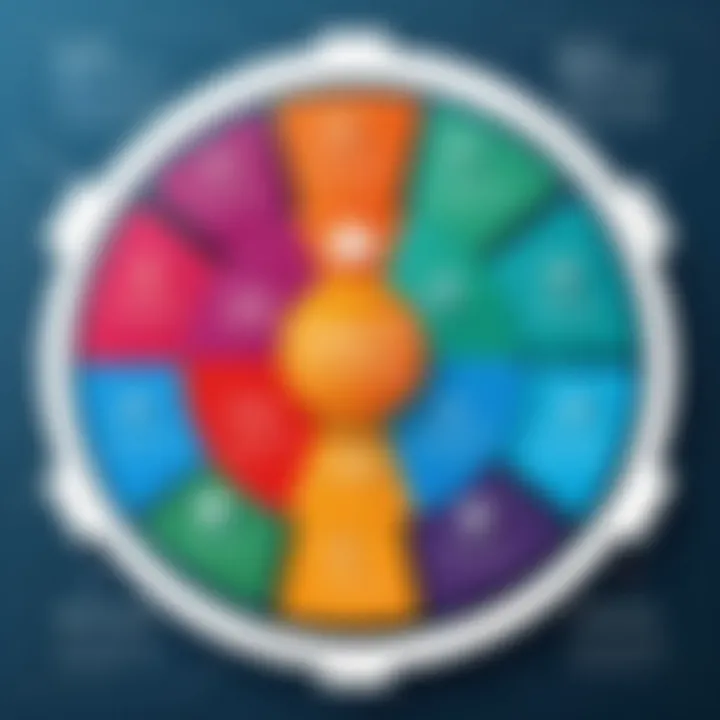
Intro
Quality Management Systems (QMS) play a crucial role in the operational framework of any business, particularly for small enterprises aiming for streamlined processes and enhanced customer satisfaction. For small businesses, the efficient implementation of a QMS can mean the difference between stagnation and growth. This article will delve into the core functionalities of QMS, especially how they can be tailored to meet the unique needs of small businesses.
In the following sections, we will explore the integral features that form the backbone of an effective QMS, the adaptability of these systems for future growth, and the specific operational benefits that come with such implementations.
A well-defined QMS not only helps in maintaining product quality but also ensures adherence to regulatory standards, facilitating a consistent level of service that customers expect. The insights shared here aim to equip small business owners with the necessary knowledge and tools to leverage QMS for enhanced operational efficiency and sustained success.
Prelude to Quality Management Systems
Quality Management Systems (QMS) play a crucial role in shaping the operational landscape of small businesses. As firms strive to maintain relevance in a competitive marketplace, a well-implemented QMS can enhance not only operational efficiency but also customer satisfaction. The essence of a QMS is to provide structured processes and metrics that ensure the consistent delivery of quality products and services.
When small businesses adopt quality management principles, they align their operations with best practices that drive improvement. This section sets the stage for understanding various aspects of QMS and lays the groundwork for exploring its components, benefits, and implementation strategies in the subsequent sections.
Definition and Purpose of QMS
A Quality Management System is an organized framework that guides an organization in enhancing its processes, products, and services. Its purpose is to ensure that a company's operations consistently meet customer and regulatory requirements. Key elements of a QMS include policies, procedures, and processes that govern quality objectives.
The primary objective of QMS is to increase customer satisfaction. It provides businesses with the tools to identify and rectify inefficiencies, thus promoting continuous improvement. By establishing clear quality policies, a business can foster a culture that prioritizes quality across all levels.
Historical Evolution of QMS
Quality Management Systems have evolved significantly since their inception. The foundations can be traced back to the early 20th century when manufacturers, such as Ford Motor Company, recognized the need for standardization in production processes. This marked the beginning of applying systematic approaches to quality.
Over the decades, prominent figures like W. Edwards Deming and Joseph Juran contributed to the development of quality management philosophies that emphasized total quality management and continuous improvement. The introduction of the ISO 9001 standard in the late 1980s was a significant milestone, offering a universal framework for organizations to benchmark their quality practices.
Today, small businesses can leverage the historical insights and established frameworks of QMS to enhance their practices and achieve sustainable growth. Understanding this historical context enriches the discussion on the effective implementation of a QMS tailored to their needs.
Importance of QMS for Small Businesses
Quality Management Systems (QMS) hold significant relevance for small businesses, as they offer a structured framework to enhance overall performance. By adopting a QMS, small companies can strengthen their operational capacity, align with industry standards, and ultimately boost their competitive edge. This section discusses the key benefits, focusing on customer satisfaction, operational efficiency, and compliance.
Enhancing Customer Satisfaction
Customer satisfaction is a crucial aspect of any business's success. Small businesses often rely on strong relationships with their customers for sustained growth. Implementing a QMS allows firms to systematically gather feedback and understand customer needs.
- Continuous Improvement: A QMS helps identify customer pain points, enabling businesses to improve products and services close to customer expectations.
- Consistency: By standardizing processes, a QMS ensures that customer experiences remain consistent. This reliability fosters trust and loyalty.
- Feedback Mechanisms: With built-in feedback loops, businesses can swiftly address concerns, demonstrating that they value their customersโ opinions.
The result of these practices often leads to improved customer retention and increased referrals, both essential for small business growth.
Improving Operational Efficiency
Operational efficiency is essential for maximizing productivity and minimizing waste. A well-implemented QMS can help streamline business processes. Various facets of operational efficiency include:
- Process Definition: Clearly defined processes become the backbone of business operations. This clarity reduces confusion, leading to quicker and more effective execution of tasks.
- Resource Optimization: A QMS allows businesses to identify inefficiencies in resource allocation. By analyzing data, small businesses can adjust strategies to utilize their resources more effectively.
- Employee Engagement: Involving employees in the QMS process often leads to increased morale and investment in their work. When employees understand the impact of quality control, they are more likely to contribute innovative ideas for improvement.
Ultimately, an efficient operational model means reduced costs and higher output, contributing directly to the bottom line.
Ensuring Compliance and Risk Management
Compliance with industry standards and regulations is crucial for avoiding potential legal issues and maintaining credibility. A QMS provides a framework for managing compliance and risk effectively:
- Risk Assessment: A proactive QMS includes regular risk assessments. Identifying potential risks early allows businesses to mitigate issues and reduces the likelihood of costly disruptions.
- Document Control: Well-defined document control procedures ensure that policies and procedures are updated, maintained, and easily accessible.
- Regular Audits: A QMS facilitates regular internal audits, ensuring the business remains compliant with laws and standards, thus enhancing its reputation and stability.
"Implementing a QMS is not merely a set of procedures; it is an investment in a small business's future success."
For small businesses, adopting a quality management system improves profitability while also paving the way for sustainable growth.
Components of an Effective QMS
An effective Quality Management System (QMS) is vital for small businesses trying to streamline operations and enhance product quality. A well-structured QMS provides the foundation for continuous improvement and has specific components crucial for success. Understanding these elements helps small business owners implement quality strategies that promote operational efficiency and customer satisfaction.
Quality Policy
A quality policy is a formal statement that outlines an organizationโs commitment to quality. It serves as a guiding principle for all employees and decisions. The policy should reflect the companyโs goals and values regarding quality. It is essential that this statement is communicated clearly throughout the organization.
A well-crafted quality policy:
- Aligns with the overall business strategy.
- Is easily understood by all staff members.
- Sets clear expectations and standards.
Having a quality policy helps ensure that all employees are taking consistent actions toward quality initiatives. Without this, there could be confusion or misalignment in efforts.
Quality Objectives
Quality objectives are specific, measurable goals related to key quality issues. Setting these objectives is vital to ensure that the businessโs quality policy is actionable. Each objective should be aligned with the overall quality policy and focus on areas that require improvement or enhancement.
When establishing quality objectives, consider the following:
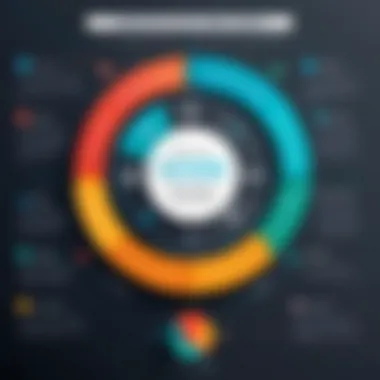
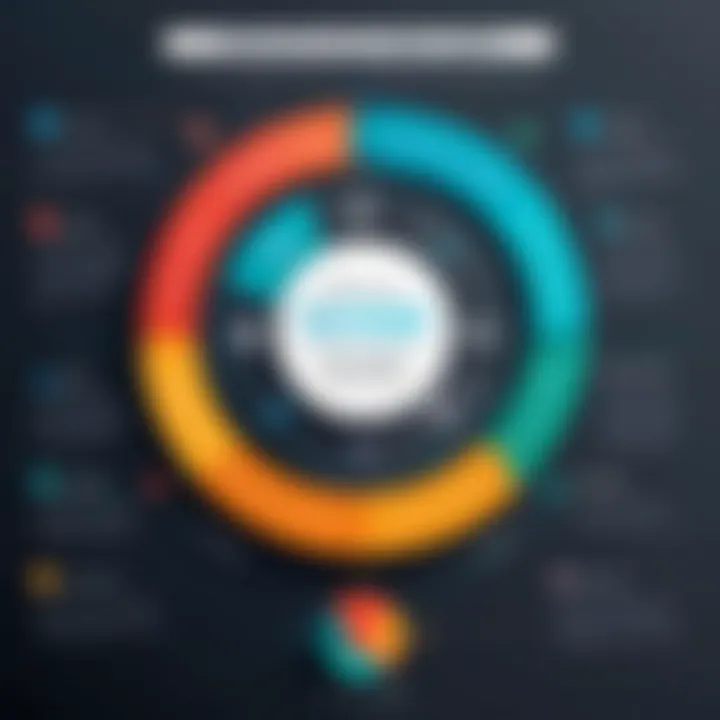
- They should be SMART: Specific, Measurable, Achievable, Relevant, and Time-bound.
- Regularly review and adjust objectives to reflect evolving business needs.
These objectives provide clear targets for employees to work towards, reinforcing the commitment to quality and allowing for performance measurement.
Document Control and Records Management
Effective document control and records management play a significant role in the success of a QMS. Properly managing documents ensures that employees have access to the most updated procedures, standards, and instructions. This is particularly important in industries where compliance is critical.
Key aspects of document control include:
- Version control: Keeping track of document revisions to avoid confusion.
- Accessibility: Ensuring all staff can easily find relevant documentation.
- Security: Protecting sensitive information from unauthorized access.
Implementing a robust document control system helps maintain organization and ensures compliance with legal and regulatory requirements.
Process Management
Process management involves the systematic identification, assessment, and improvement of business processes. It focuses on defining the processes that contribute to quality outcomes and ensures that these processes are efficient and effective.
For small businesses, process management should include:
- Documenting existing processes: Understanding how tasks are currently performed.
- Identifying areas for improvement: Using data and feedback to pinpoint inefficiencies.
- Implementing changes: Making adjustments based on insights to drive quality improvements.
Focusing on process management can significantly reduce waste, improve productivity, and enhance product quality. It allows businesses to create repeatable and standardized processes that lead to more reliable outcomes.
"Quality is not just an act; it is a habit."
Common Quality Management Standards
Quality Management Standards provide a framework for organizations to ensure that their products and services consistently meet customer requirements and quality is consistently improved. For small businesses, adhering to established standards can enhance credibility and market competitiveness. Commonly recognized standards, including ISO 9001, Six Sigma, and Total Quality Management (TQM), offer systematic approaches to quality management and operational excellence.
These standards compel small businesses to outline clear policies and objectives, fostering a culture of continual improvement. Moreover, they can help in reducing inefficiencies, lower operational costs, and increase customer satisfaction by establishing predictable processes. As small businesses grapple with resource limitations, understanding and implementing these standards is vital.
"A well-implemented Quality Management System leads to better engagement with customers and drives continuous improvement throughout the business."
ISO Overview
ISO 9001 is perhaps the most recognized quality management standard worldwide. This standard emphasizes a process-oriented approach that is beneficial for businesses of any size, but it is especially valuable for small enterprises. ISO 9001 requires businesses to demonstrate their ability to provide consistent products and services that meet customer and regulatory requirements.
One significant aspect of ISO 9001 is its focus on customer satisfaction. It encourages businesses to understand customer needs and recognize the importance of customer feedback in driving improvements. Implementing this standard may require additional documentation and process design, but the long-term benefits include increased efficiency and a stronger reputation.
Six Sigma Principles
Six Sigma is a disciplined, data-driven approach aimed at improving processes by minimizing variability and defects. For small businesses, the principles of Six Sigma can lead to significant enhancements in operational efficiency and customer satisfaction. The methodology revolves around the DMAIC framework, which includes Define, Measure, Analyze, Improve, and Control.
Small businesses adopting Six Sigma may face challenges in data collection and analysis due to limited resources. However, the benefits of implementing these principles include better decision-making based on solid data and a robust approach to quality improvement. This could lead to considerable cost savings and improved process performance over time.
Total Quality Management (TQM)
Total Quality Management (TQM) takes a holistic approach to quality management by integrating it into the organization's culture. TQM encourages a continuous improvement mindset, involved participation from all employees, and a strong focus on customer satisfaction. In small businesses, TQM can foster teamwork and build a unified focus on delivering quality.
While implementing TQM may require significant time investment and cultural shifts, the payoff can be substantial. Employees engaged in TQM practices can contribute effectively towards enhancing operational processes, often leading to innovation and improved service delivery. Small businesses using TQM may discover that their work environment becomes more collaborative, and their overall performance is elevated.
Challenges Faced by Small Businesses in QMS Implementation
Implementing a Quality Management System (QMS) is crucial yet challenging for small businesses. As these firms strive to enhance their operations, they often encounter specific hurdles that can hinder effective QMS adoption. Understanding these challenges is essential, as they not only affect the potential benefits but also shape the overall approach to quality management. Small businesses must address these challenges proactively to position themselves for successful implementation.
Resource Constraints
One prominent issue that small businesses face is resource constraints. Unlike larger organizations, they often operate with limited financial and human resources. This limitation can affect the ability to invest in QMS initiatives, including training, software, and necessary tools.
Small businesses frequently deal with tight budgets. This financial strain makes it difficult to allocate funds toward comprehensive quality management systems. In many cases, owners may prioritize immediate operational needs over long-term quality improvement. A shortage of personnel also plays a role. With fewer employees, small businesses can struggle to assign dedicated staff for QMS planning and execution. As a result, the introduction of new processes can become overwhelming and lead to delays or ineffective practices.
Despite these challenges, small businesses can explore cost-effective solutions. Utilizing cloud-based QMS software may present a viable option. Moreover, outsourcing certain functions can help manage quality more effectively without overextending internal resources.
Resistance to Change
Another significant barrier is resistance to change among employees. People tend to prefer the status quo, particularly in established work environments. When a new QMS is implemented, some employees may feel anxious about changes in their routines or doubt the effectiveness of the new processes. This hesitation can result in pushback, which complicates the adoption of the QMS and hinders the overall objective of quality improvement.
To overcome resistance, communication is vital. Engaging employees from the beginning by explaining the benefits of QMS can foster a culture of acceptance. Additionally, involving them in the QMS development process allows for ownership and a clearer understanding of the objectives.
Limited Awareness and Training
Limited awareness and knowledge about quality management practices also create hurdles. Many small business owners and employees may lack the training needed to understand QMS principles fully. This gap in knowledge can lead to errors in implementation or a lack of adherence to established processes.
Small businesses often neglect ongoing training due to budget constraints. However, they can explore various training resources. Online courses and webinars may provide affordable options for enhancing skill sets. Implementing a mentorship program can also be beneficial, allowing experienced employees to guide others in understanding QMS practices better.
Successful implementation of QMS hinges on overcoming these challenges. By recognizing resource limitations, addressing resistance to change, and enhancing training opportunities, small businesses can make meaningful progress in their quality management efforts.
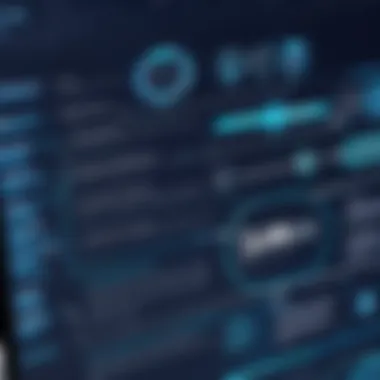
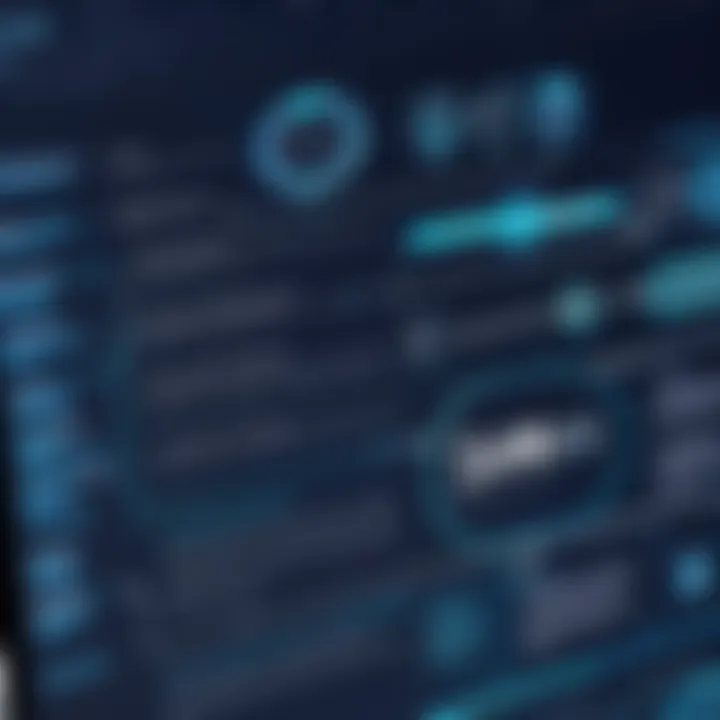
Steps to Implement a QMS in a Small Business
Implementing a Quality Management System is critical for small businesses aiming for efficiency and effectiveness. Establishing a QMS helps in maintaining high-quality standards, ensuring customer satisfaction, and improving business operations. To successfully implement a QMS, businesses should follow a series of logical steps tailored to their specific needs.
Conducting a Gap Analysis
A gap analysis serves as the foundation of an effective QMS. This process entails evaluating the current quality practices against the desired quality standards. It helps to identify what areas require improvement and what processes need to be developed or refined. By conducting a gap analysis, small businesses can pinpoint deficiencies or risks in their current system.
Key components of a gap analysis include:
- Documentation Review: Examine existing quality manuals and procedures.
- Process Mapping: Visualize current workflows to highlight inefficiencies.
- Stakeholder Engagement: Involve employees for insights on operational hurdles.
This thorough evaluation is paramount in setting a clear baseline before embarking on the QMS journey.
Defining Quality Objectives
Once the gaps are identified, the next step is defining clear quality objectives. Quality objectives provide specific, measurable goals that align with the overall business strategy. These objectives should be realistic and relevant, taking into account the needs of both customers and the organization.
Consider the following when defining quality objectives:
- SMART Criteria: Ensure objectives are Specific, Measurable, Achievable, Relevant, and Time-bound.
- Customer Focus: Tailor objectives to enhance customer satisfaction and retention.
- Alignment with Business Goals: Connect quality objectives with broader organizational goals.
Achieving these objectives fosters a culture of continuous improvement and accountability within the organization.
Developing and Documenting Procedures
Developing and documenting procedures is a vital part of establishing a QMS. Well-defined procedures serve as a blueprint for maintaining quality. They provide clarity on processes and create a standard for consistent performance. Proper documentation also facilitates training and communication among staff.
Important elements to consider include:
- Standard Operating Procedures (SOPs): Develop clear instructions for key tasks.
- Quality Manual: Compile relevant documents that outline the QMS structure and requirements.
- Change Management: Establish a process for updating documents as needed.
Effective documentation ensures consistency in operations and provides a reference point for staff performance.
Employee Training and Involvement
Employee training is crucial to effective QMS implementation. A well-informed workforce is essential for adapting to new procedures and standards. Training sessions should focus on the importance of quality, processes within the QMS, and individual roles in achieving quality objectives.
Strategies for enhancing employee training include:
- Regular Workshops: Conduct workshops to explain the QMS and its relevance.
- Continuous Learning: Encourage ongoing education and skill development related to quality management.
- Feedback Mechanism: Establish channels for employees to share observations and suggestions.
Involving employees in the QMS process not only strengthens commitment but also promotes a collective responsibility for quality assurance.
"Empowering employees through effective training creates a robust foundation for quality management."
Implementing these steps will put a small business on the path toward a successful Quality Management System that not only meets industry standards but also drives sustainable improvement.
Tools and Technologies for QMS
Tools and technologies play a crucial role in the successful implementation and maintenance of a Quality Management System (QMS) in small businesses. By leveraging the right tools, small businesses can streamline their processes, enhance communication, and ultimately achieve higher quality standards. Moreover, the adoption of advanced technologies can result in better data management and contribute to continuous improvement initiatives.
Utilizing the right tools helps businesses detect issues earlier, address customer feedback efficiently, and align their processes with industry standards. It is vital for small business owners to understand the available tools that can support their QMS efforts. Here, we discuss two key components: QMS Software Solutions and the role of Data Analytics in quality improvement.
QMS Software Solutions
Quality Management System software solutions provide an organized platform for managing various aspects of quality. These solutions often include features such as document control, audit management, corrective actions, and training management. By centralizing data and processes, companies can create a structured approach to meet quality objectives.
Benefits of QMS Software Solutions:
- Efficiency: Automating routine tasks allows teams to focus on more strategic activities.
- Transparency: Enhanced visibility into quality processes helps maintain accountability.
- Compliance Management: Simplifying adherence to standards and regulations reduces the likelihood of penalties.
When selecting QMS software, consider factors such as scalability, user-friendliness, and the ability to integrate with existing systems. It is essential to choose a solution that aligns with the unique needs of the business and its specific quality goals.
Data Analytics for Quality Improvement
Data analytics has emerged as a powerful tool for facilitating quality improvement in small businesses. By collecting and analyzing data related to processes, customer feedback, and product performance, businesses can make informed decisions to drive enhancements.
Key Advantages of Data Analytics:
- Insightful Decision-Making: Identifying trends and patterns allows managers to address quality issues proactively.
- Resource Allocation: Analyzing data helps in the strategic distribution of resources toward areas in need of improvement.
- Performance Measurement: Direct metrics enable businesses to evaluate their progress towards quality objectives clearly.
However, utilizing data analytics effectively requires some considerations. Small businesses may need training for staff on how to use analytic tools competently. Moreover, ensuring data integrity is essential, as inaccurate data can lead to misguided conclusions. Incorporating data analytics into the QMS framework remains a pivotal step in fostering a culture of quality and continuous improvement.
Measuring the Effectiveness of QMS
Measuring the effectiveness of a Quality Management System (QMS) is crucial for small businesses aiming to enhance their operational efficiency and customer satisfaction. An effective QMS not only minimizes waste and maximizes productivity, but also fosters a culture of continuous improvement. To ensure that a QMS delivers its promised benefits, regular evaluation and management of its elements are essential. This systematic approach helps organizations identify gaps, make necessary adjustments, and ultimately achieve long-term sustainability.
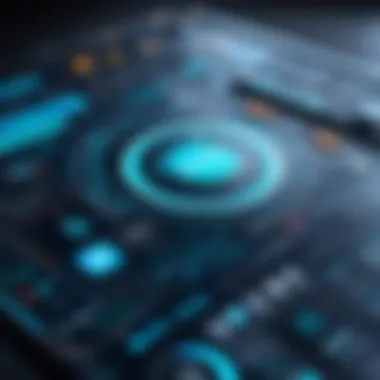
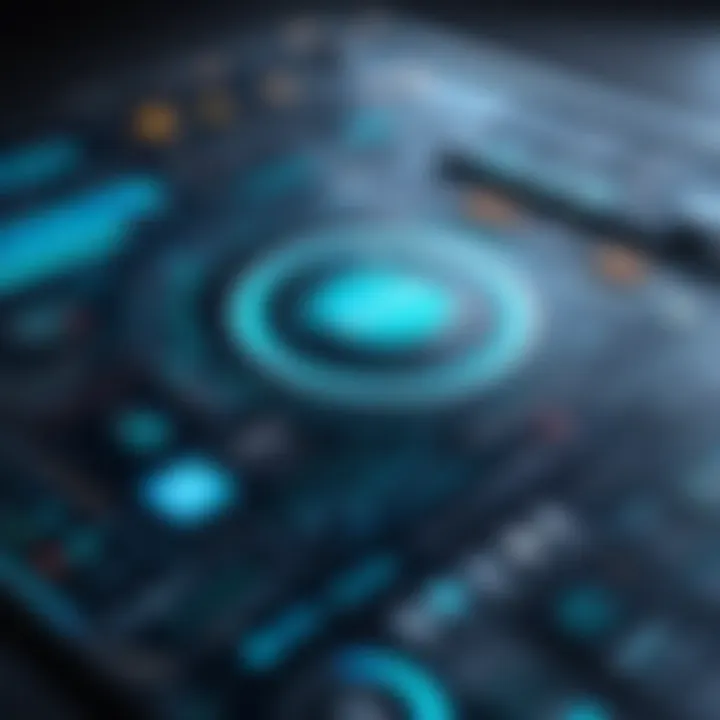
Key Performance Indicators (KPIs)
Key Performance Indicators, or KPIs, serve as quantifiable measures to evaluate the success of a QMS. These indicators should align with the set quality objectives and provide insights into various aspects of organizational performance. Some common KPIs for small businesses could include:
- Customer Satisfaction Scores: Measuring how satisfied customers are with products or services. Higher scores often correlate with effective quality management.
- First Pass Yield: The percentage of products manufactured correctly without requiring rework. A higher yield reflects efficient processes.
- Employee Training Completion Rates: Tracking the number of employees who have completed quality-related training. Higher rates suggest commitment to quality practices.
- Defect Rates: Monitoring the frequency of defects or errors in products/services. Lower defect rates indicate an effective QMS.
By analyzing these KPIs, businesses can make informed decisions about areas needing improvement. They can establish benchmarks over time, allowing for comparisons that highlight progress or the need for changes.
Continuous Improvement Practices
Continuous improvement practices form the backbone of an effective QMS. These practices ensure that the processes are always evolving and adapting to the changing business environment. Some key techniques that small businesses can adopt include:
- Plan-Do-Check-Act (PDCA Cycle): This approach involves planning a change, implementing it, checking the results, and acting on what was learned. It encourages constant refinement of processes.
- Lean Principles: Focusing on minimizing waste within manufacturing systems while simultaneously maximizing productivity. This approach can enhance efficiency and reduce costs.
- Root Cause Analysis: Whenever problems arise, itโs vital to conduct a root cause analysis. Understanding the underlying issue helps prevent reoccurrences and establishes stronger processes.
Implementing these continuous improvement practices enables businesses to stay ahead of potential issues and trends, creating an agile QMS that contributes to sustained growth and quality assurance.
"Measuring the effectiveness of QMS ensures the organization continuously meets its goals, meets stakeholder expectations, and enhances customer trust in the brand."
Case Studies of Successful QMS Implementation
Implementing a Quality Management System (QMS) is essential for small businesses aiming to enhance their operations. The importance of examining case studies in this context cannot be overstated. These case studies provide tangible examples of how QMS can be effectively adopted in real-world scenarios. They showcase the practical benefits achieved, such as improved efficiency, increased customer satisfaction, and enhanced overall performance. By studying successful implementations, businesses can identify best practices, potential pitfalls, and key considerations relevant to their unique situations.
Case studies also demonstrate the scalability of QMS principles across different types of businesses. This knowledge aids small business owners in visualizing their path to QMS integration, ensuring they avoid mistakes made by others and replicate successful strategies.
Small Manufacturing Firms
Manufacturing firms often face unique challenges, such as managing production quality and ensuring compliance with industry standards. A compelling case study is that of an unnamed small manufacturing firm which manufactures metal components. This firm struggled with variability in product quality, leading to frequent customer complaints and returns.
In response, the firm implemented ISO 9001, one of the leading quality management frameworks. By conducting a gap analysis, the firm identified critical areas needing improvement. This analysis allowed the company to redefine its quality objectives and improve its document control processes. Key performance indicators (KPIs) like defect rates were established, ensuring clear targets and measurable outcomes.
After utilizing QMS software, they streamlined their workflows. Employee training was essential as it fostered a culture of quality awareness. As a result, they witnessed a significant reduction in defect rates by 40% within the first year. Moreover, their customer satisfaction ratings improved, leading to repeat business and referrals. This case clearly illustrates how a structured QMS approach can drive operational success in manufacturing settings.
Service-based Small Businesses
Service-based businesses often face the challenge of intangible outputs in terms of quality. A relevant case study involves a small consultancy firm that specialized in marketing strategies. The firm recognized a decline in client satisfaction due to inconsistent service delivery.
To address this, the firm adopted Total Quality Management (TQM) principles, focusing on continuous improvement and customer feedback. They began by mapping their service delivery process. Identifying bottlenecks allowed them to create standardized operating procedures, ensuring consistent quality in all client interactions.
Employee involvement was pivotal in this firmโs transformation. Regular training sessions and workshops were instituted to enhance skills and knowledge. The firm also solicited feedback through surveys, ensuring they were aligned with client expectations. As a result, the firm reported a 30% increase in client satisfaction and a notable rise in client retention rates.
These case studies demonstrate that implementing a QMS is not a mere theoretical exercise; it leads to concrete results. They provide invaluable lessons for small businesses, guiding them toward better practices and successful quality management.
Future Trends in QMS for Small Businesses
In today's rapidly changing business landscape, small businesses increasingly face the challenge of adapting their processes to remain competitive. Quality Management Systems (QMS) play a vital role in achieving this goal. Understanding and implementing future trends in QMS is crucial for small businesses to achieve efficiency, enhance customer satisfaction, and ensure their long-term viability.
Integration with Digital Transformation
The trend of digital transformation is reshaping how businesses operate and interact with customers. For small businesses, integrating QMS with digital technologies can drive unprecedented efficiencies. This integration can include the use of cloud-based QMS platforms, which allow for real-time data access, collaboration, and improved documentation control.
Small businesses can benefit from automating quality assurance processes using software that tracks performance metrics and monitors compliance. This data-driven approach enables decision-makers to address issues promptly before they escalate. Furthermore, the integration can lead to improved customer feedback loops, enhancing responsiveness and tailoring products or services to meet needs more accurately.
"Adopting digital technologies in QMS can create a highly adaptable business infrastructure, essential in a fluctuating market."
Sustainability and Quality Management
Sustainability is emerging as a focal point in business strategy, and Quality Management Systems are no exception. Small businesses are beginning to recognize the importance of incorporating sustainable practices within their QMS. This can involve minimizing waste, using eco-friendly materials, or implementing energy-saving measures throughout their operations.
Sustainability enhances brand image and attracts a more conscious customer base. Customers today often prefer to engage with businesses that demonstrate a commitment to sustainable practices. Implementing a sustainable QMS not only improves environmental performance but also can lead to cost reductions through improved resource efficiency. Stakeholders, including employees and consumers, are likely to respond positively to clear sustainability initiatives embedded in quality management practices.
As the trend of sustainability integrates into QMS, it represents a strategic advantage, making small businesses more resilient and appealing to a wider audience.
Epilogue
In the context of this article, the conclusion serves not merely as a summary, but as a key component that reinforces the significance of Quality Management Systems (QMS) for small businesses. It encapsulates the main themes outlined throughout the sections and emphasizes the practical importance of implementing a QMS in today's business environment.
One fundamental aspect highlighted is the enhancement of customer satisfaction. Businesses that prioritize quality through structured management systems tend to listen more to their customers. This feedback loop creates a culture of continuous improvement, which eventually leads to loyalty.
In addition, the conclusion discusses operational efficiency, which is vital for small enterprises often facing resource constraints. A well-implemented QMS streamlines processes, minimizes waste, and ultimately fosters a culture of productivity. This factor can be a crucial differentiator in a competitive marketplace.
Moreover, compliance and risk management are essential for sustainability. A strong QMS helps organizations ensure that they meet regulatory requirements consistently, reducing the likelihood of costly errors or legal repercussions. It helps create a proactive approach to risk management, allowing businesses to identify potential issues before they escalate.
Altogether, the conclusion serves as a reminder that embracing a Quality Management System is not just about adhering to standards. It's about establishing a foundation for continuous improvement, enhancing customer relations, and ultimately driving growth.
Recap of Key Points
- Customer satisfaction is significantly improved through a QMS, creating valuable feedback cycles.
- Operational efficiency is enhanced as processes become more streamlined, less wasteful, and more productive.
- Strong focus on compliance reduces legal risks and ensures regulatory standards are met consistently.
- A QMS promotes a culture of continuous improvement, essential for long-term business success.
Final Thoughts on QMS for Small Businesses
To sum up, implementing a QMS in a small business context is not an option but a necessity. As the competitive landscape evolves, businesses must adapt proactively. The insightful implementation of a Quality Management System leads to comprehensive benefits, from improved customer experiences to enhanced operational performance. Small businesses often view resources as scarce, making the structured approach that a QMS provides invaluable.
As organizations lay the groundwork for their QMS, leadership commitment and employee involvement are crucial. All levels of the organization must be engaged, ensuring that the QMS is not merely a documentation exercise, but a living framework that drives quality in every aspect of the business.
In closing, quality management is a journey, not just a destination. Small businesses that embrace this concept can position themselves uniquely in the marketplace, attract a loyal customer base, and promote sustainable growth.